VAZ-2112 engine Petrol, four-stroke, four-cylinder, in-line, transverse, sixteen-valve, with two camshafts.
The order of operation of the cylinders: 1-3-4-2, counting - from the crankshaft pulley.
Power system - phased distributed injection.
Engine control - controller (Bosch, "January" or GM).
Most engines are equipped with an exhaust gas converter.
An engine with a gearbox and a clutch form a power unit mounted in the engine compartment on four elastic rubber-metal bearings.
The right and left bearings are the same as on the 2110 and 2111 engines.
The front and rear supports are the same, representing rods.
One end of the rod is attached to the bracket on the engine, the other - to the bracket on the body.
On the right side of the engine (along the vehicle) are located: camshaft drives and coolant pump (toothed belt) and generator (V-ribbed belt).
On the left are: thermostat, coolant temperature sensors, oil pressure sensor, starter (on the clutch housing).
Front: intake manifold, fuel rail with injectors, knock sensor, oil dipstick, crankcase breather hose, alternator (bottom right), phase sensor (top right).
Rear: exhaust manifold, oil filter, crankshaft position sensor (lower right).
At the top (under a plastic cover) there are a receiver, candles (in guide pipes sealed with rubber rings) and high-voltage wires.
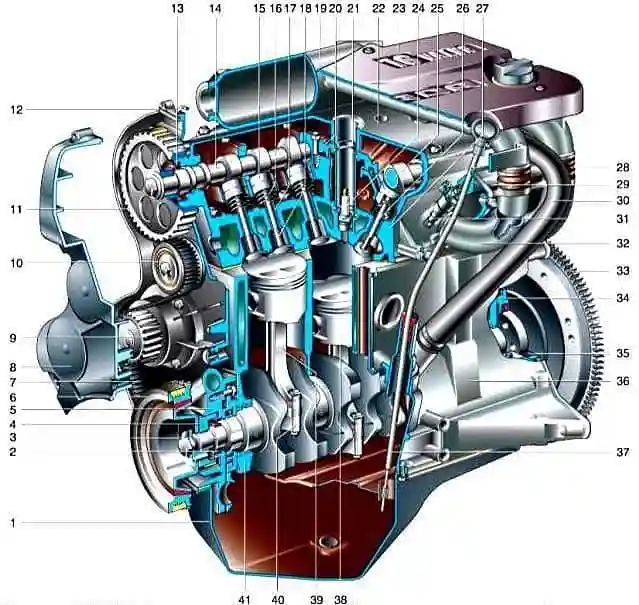
VAZ-2112 engine: 1 - oil pan; 2 - front crankshaft oil seal; 3 - crankshaft; 4 - toothed pulley of the crankshaft; 5 - oil pump; 6 - generator drive pulley; 7 - toothed belt; 8 - front cover of the timing mechanism drive; 9 - toothed pulley of the coolant pump; 10 - tension roller; 11 - a gear pulley of a camshaft; 12 - rear cover of the timing mechanism drive; 13 - camshaft seal; 14 - exhaust camshaft; 15 - hydraulic pusher; 16 - valve spring; 17 - valve guide sleeve; 18 - exhaust valve; 19 - receiver; 20 - camshaft bearing cover; 21 - guide pipe; 22 - cylinder head cover; 23 - plastic cover; 24 - spark plug; 25 - intake camshaft 26 - intake valve; 27 - cylinder head; 28 - coupling; 29 - fuel rail; 30 - crankcase ventilation hose; 31 - nozzle; 32 - intake manifold; 33 - flywheel; 34 - holder of the rear oil seal of the crankshaft; 35 - crankshaft rear oil seal 36 - cylinder block; 37 - oil dipstick; 38 - piston; 39 - connecting rod; 40 - connecting rod cover; 41 - crankshaft main bearing cap
The cylinder block is cast from cast iron and has the index "21083" - like the engines 2110 and 2111, however, they are not interchangeable: the holes for the cylinder head screws are threaded M10x1.25 (unlike M12x1, 25 for engine blocks 2110 and 2111) and shallower.
Another difference is related to the more intense thermal conditions of the 2112 engine compared to the 2110 and 2111 engines.
To cool the pistons during engine operation, their bottoms are washed from below with oil through special nozzles pressed into the second, third, fourth and fifth main bearing supports.
The cylinders are bored directly into the block. The nominal diameter of 82 mm can be increased by 0.4 or 0.8 mm during repairs.
The class of the cylinder is marked on the lower plane of the block in Latin letters in accordance with the diameter of the cylinder in mm: A - 82.00-82.01, B - 82.01-82.02, C - 82.02-82.03, D - 82.03-82.04, E - 82.04-82.05.
The maximum allowable cylinder wear is 0.15 mm per diameter.
In the lower part of the cylinder block there are five main bearing supports with removable covers, which are attached to the block with special bolts.
The covers are non-interchangeable (the bearing bores are machined complete with the covers) and are marked to distinguish the risks on the outer surface.
In the middle support there are nests for thrust half rings that prevent axial movement of the crankshaft.
A steel-aluminum semi-ring is placed in front (from the side of the crankshaft pulley), and a metal-ceramic one is placed in the back.
Rings are produced with nominal and increased by 0.127 mm thickness.
When the axial clearance of the crankshaft exceeds 0.35 mm, one or both half rings change (the nominal clearance is 0.06-0.26 mm).
The shells of the main and connecting rod bearings are thin-walled steel-aluminum.
Top main bearings 1st, 2nd, 4th and 5th bearings installed in the cylinder block are equipped with a groove on the inner surface.
The lower main bearings, upper third bearing bearing and crank bearings do not have grooves.
Repair inserts are available for crankshaft journals reduced by 0.25, 0.50, 0.75 and 1.00 mm.
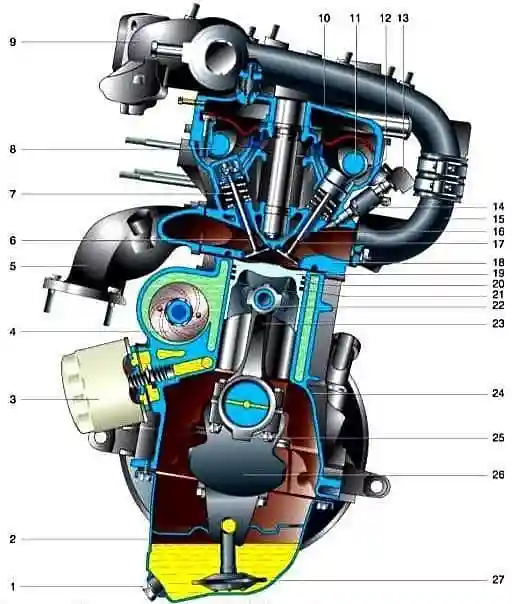
Cross section of the VAZ-2112 engine: 1 - drain plug of the oil pan; 2 - oil pan; 3 - oil filter; 4 - coolant pump; 5 - exhaust manifold; 6 - exhaust valve; 7 - valve spring; 8 - final camshaft; 9 - receiver; 10 - cylinder head cover; 11 - intake camshaft; 12 - hydraulic pusher; 13 - fuel rail; 14 - nozzle; 15 - intake manifold; 16 - valve guide sleeve; 17 - inlet valve; 18 - cylinder head; 19 - piston; 20 - compression rings; 21 - oil scraper ring; 22 - piston pin; 23 - connecting rod; 24 - cylinder block; 25 - connecting rod cover; 26 - crankshaft; 27 - oil pump receiver
The crankshaft is made of ductile iron.
It has five main journals and four crankpins and is equipped with eight counterweights cast integrally with the shaft.
The crankshaft of the 2112 engine differs from the crankshaft of the 2110 and 2111 engines in the form of counterweights and increased strength.
Therefore, it is not allowed to install the crankshaft from engines 2110 and 2111 in the engine 2112.
To supply oil from the main journals to the connecting rods, channels are drilled in the crankshaft, the outlets of which are closed with pressed plugs.
At the front end of the crankshaft, a camshaft drive gear pulley is mounted on a segment key, a generator drive pulley is attached to it, which is also a crankshaft vibration damper.
Two teeth out of 60 are missing on the gear ring of the pulley - the cavities are used for the operation of the crankshaft position sensor.
A flywheel (index 2110) is attached to the rear end of the crankshaft with six self-locking bolts through a common washer.
The cone-shaped hole near the flywheel ring should be opposite the crankpin of the fourth cylinder (this is necessary to determine the TDC after engine assembly).
Connecting rods - steel, I-section, processed together with covers.
On the covers, as well as on the connecting rods, the cylinder number is stamped (it must be on the same side of the connecting rod and the cover).
The connecting rods are divided into three classes in increments of 0.004 mm according to the diameter of the steel-bronze bushing pressed into the upper head.
The class number is stamped on the connecting rod cap. Also, connecting rods are divided into classes by weight - they are marked with paint or a letter on the connecting rod cover.
Piston pin - steel, tubular section, floating type (rotates freely in the upper head of the connecting rod and in the piston bosses).
It is fixed from falling out by two retaining spring rings, which are located in the grooves of the piston bosses.
There are three classes of fingers according to the outer diameter (through 0.004 mm): 1 - with blue, 2 - green, 3 - red (smallest diameter) marks.
Piston - aluminum alloy. The piston skirt in the longitudinal section is conical, in the transverse section it is oval.
Three grooves for piston rings are machined in the upper part of the piston.
The oil scraper ring groove has drillings leading into the bosses, through which the oil collected by the ring from the cylinder walls flows to the piston pin.
The hole for the piston pin is offset from the diametral plane of the piston by 1 mm.
When installing the piston, it is necessary to follow the arrow stamped on the bottom (it must be directed towards the crankshaft pulley).
The 2112 engine pistons have a flat bottom with four valve recesses (the 2110 and 2111 engine pistons have an oval bottom).
Pistons by outer diameter (measured in a plane perpendicular to the piston pin, at a distance of 51.5 mm from the piston bottom), like cylinders, are divided into five classes (marking - on the bottom).
Piston diameter (for nominal size, mm): A - 81.965-81.975; B - 81.975-81.985; C - 81.985-81.995; D - 81.995-82.005; E - 82.005-82.015.
Pistons of classes A, C and E (nominal and repair sizes) go on sale: the calculated gap between them is 0.025-0.045 mm, and the maximum allowable wear gap is 0.15 mm.
It is not recommended to install a new piston in a worn cylinder without boring it: the groove for the upper piston ring in the new piston may be slightly higher than in the old one, and the ring can break on the "step" formed at the top of the cylinder when it wears out.
At repair pistons, a triangle (+ 0.4 mm) or a square (+ 0.8 mm) is knocked out on the bottom.
According to the diameter of the hole for the piston pin, pistons are divided into three classes: 1 - 21.978-21.982; 2 - 21.982-21.986; 3 - 21.986-21.990.
The piston class is also stamped on its bottom.
Piston and pin must be of the same class.
The pistons of one engine are selected by weight (the spread should not exceed 5 g) - this is done to reduce the imbalance of the crank mechanism.
The upper two piston rings are compression rings that prevent the breakthrough of gases into the engine crankcase.
They also contribute to the removal of heat from the piston to the cylinder. The lower ring is oil scraper.
Cylinder head - common to all four cylinders - made of aluminum alloy.
It is centered on the block with two bushings and secured with ten screws.
A non-shrink metal-reinforced gasket is installed between the block and the head (their surfaces must be dry) (it must not be reused).
The order and tightening torque of the block head screws are indicated in the appendix.
At the top of the cylinder head are the camshaft bearings - five on each side of the head.
The holes in the split supports are machined complete with the bearing housing.
It is necessary to replace the body assembly with the cylinder head.
Loctite No. 574 sealant is applied to the surfaces of the cylinder head mating with the bearing housing.
See the appendix for the order and tightening torque of the bearing housing nuts.
Camshafts - cast, cast iron, five-bearing, each with eight cams (a pair of adjacent cams simultaneously open two valves in the cylinder).
Camshafts are driven by a toothed belt from the crankshaft.
Due to the increased loads on the toothed belt, its width in the 2112 engine, compared to 2110 and 2111, has been increased from 19.0 to 25.4 mm (respectively, the width of the toothed pulleys and rollers has been increased).
There is a support roller under the intake camshaft pulley, and a tensioner under the exhaust camshaft.
For the operation of the phase sensor, a disk is welded to the toothed pulley of the intake camshaft.
There are alignment marks on the drive gears: if the mark on the crankshaft pulley matches the mark on the oil pump housing (the mark on the flywheel is opposite the middle division of the scale on the clutch housing), then the marks on the camshaft pulleys must match the marks on the rear cover camshaft drive.
Seats (cermet) and valve guides (brass) are pressed into the cylinder head.
The holes in the bushings are machined after pressing. The inner diameter of the bushings has been reduced, compared to the engines 2110 and 2111, from 8 to 7 mm.
Repair bushings with an outside diameter of 12.279-12.290 mm (increased by 0.2 mm compared to the nominal) are also supplied with the spare parts kit.
On the inner surface of the bushings for lubrication, grooves similar to threads are made: for the bushings of the inlet valves - for the entire length, for the exhaust valves - up to half the length of the hole.
On top of the bushings, oil deflector caps made of oil-resistant rubber are put on.
Valves - steel, exhaust - with a head made of heat-resistant steel with welded chamfer.
The area of the intake valve plate is larger than the exhaust valve.
They are smaller than the valves of the 2110 and 2111 engines.
The valves are arranged in two rows, V-shaped.
They are driven by camshaft cams through hydraulic pushers.
The axis of the cam is offset by 1 mm relative to the axis of the hydraulic pusher.
Due to this, when the engine is running, the pusher body rotates around its axis, which contributes to its more uniform wear.
Hydraulic pushers select the gap between the cam and the pusher body during engine operation, which reduces the noise of the gas distribution mechanism, and also eliminates its maintenance (gap adjustment is not required).
For the operation of hydraulic pushers, a constant supply of oil under pressure is required.
For this, the cylinder head has a channel with a check ball valve (it prevents oil from draining from the channels after the engine is stopped), as well as channels on the lower plane of the bearing housing (they also supply oil to the camshaft journals).
Hydraulic tappets are very sensitive to oil quality and purity.
If there are mechanical impurities in the oil, a quick failure of the plunger pair of the hydraulic pusher is possible, which is accompanied by increased noise in the gas distribution mechanism and intensive wear of the camshaft cams.
A defective hydraulic pusher cannot be repaired, it should be replaced. The valve closes under the action of one spring.
Lower with its end it rests on the puck, and with its upper end it rests on a plate held by two crackers.
Folded crackers on the outside have the shape of a truncated cone, and on the inner surface there are three resistant collars included in the grooves on the valve stem.
Engine lubrication - combined.
Under pressure, main and connecting rod bearings, "support - camshaft journal" pairs, hydraulic pushers are lubricated.
By spraying, oil is supplied to the cylinder walls (further to the piston rings and fingers), to the bottom of the pistons, to the "camshaft cam - pusher" pair and valve stems.
The rest of the nodes are lubricated by gravity.
Oil pump - with internal gears and pressure reducing valve - mounted on the front wall of the cylinder block.
The drive gear is mounted on two flats on the front end of the crankshaft.
The maximum diameter of the socket for the driven (large) gear during wear should not exceed 75.10 mm, the minimum width of the segment on the housing separating the drive and driven gears is 3.40 mm.
The axial clearance for the drive gear should not exceed 0.12 mm, for the driven gear - 0.15 mm.
An oil receiver is bolted to the cover of the second main bearing and the pump housing.
Oil filter - full-flow, non-separable, equipped with bypass and anti-drain valves.
Crankcase ventilation system - closed, forced, exhaust gases through the oil separator located in the cylinder head cover.