Зняття та розбирання головки блоку циліндрів двигуна розглянуто у відповідних статтях.
Після того, як розібрали головку циліндрів, потрібно промити всі деталі головки, очистити їх від нагару.
Підготовляємо деталі для огляду.
Перевіряємо посадкову поверхню головки та висоту головки блоку циліндрів.
Висота h головки блоку повинна становити 137 мм (рисунок 1).
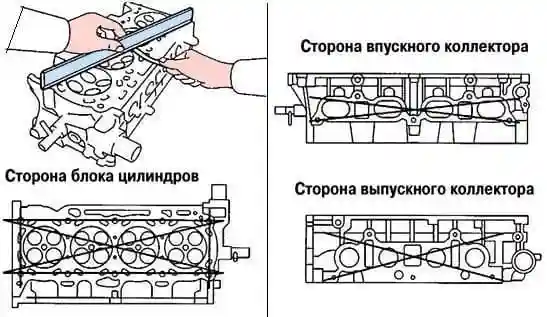
Лінійкою та щупом перевіряємо неплощинність посадкових поверхонь головки блоку циліндрів (рисунок 2).
Допускається максимальна неплощинність 0,05 мм. Шліфування поверхонь не допускається.
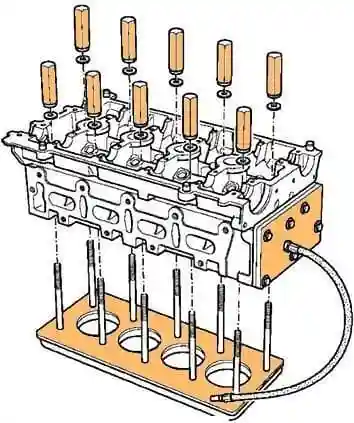
Перевіряємо головку блоку циліндрів (відсутність тріщин та наскрізної корозії) за допомогою відповідного пристрою (рисунок 3).
Перевіряємо довжину болтів кріплення головки. Довжина болтів без урахування головки має бути не більше 117,7 мм.
Якщо встановлюємо нові болти, то перед їх встановленням їх змащувати не потрібно, вживані болти потрібно змастити моторним маслом.
Наступна підтяжка болтів кріплення головки блоку циліндрів не потрібна і не допускається, інакше різко зростає ймовірність руйнування болтів при відкручуванні.
Перед затягуванням болтів видаліть бруд і масло, що залишилося в різьбових отворах блоку циліндрів.
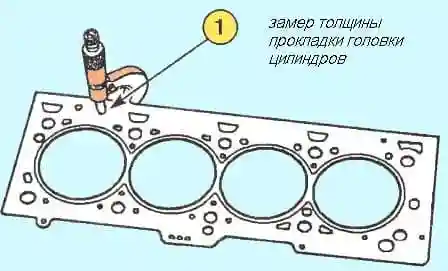
Вимірюємо товщину прокладки (рисунок 4). Товщина заміряється в місці, зазначеному стрілкою на малюнку 4.
Товщина нової прокладки має бути 0,96±0,06 мм; товщина обтиснутої прокладки має бути 0,90±0,02 мм.
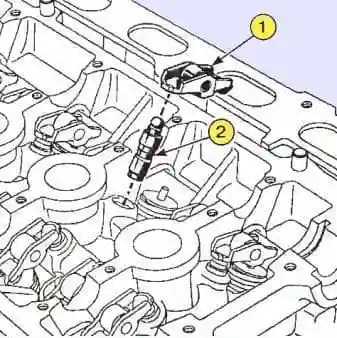
Оглядаємо гідравлічні штовхачі та коромисла.
Вимірюємо клапани відповідно до рисунка 6.
Розміри клапанів повинні відповідати даним у таблиці.
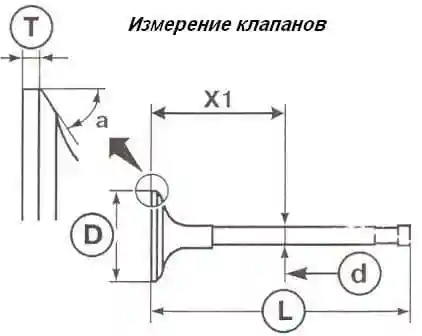
Основні розміри клапанів
Найменування Розмір мм.
Діаметр стрижня D1:
- Впускні клапани 5,470-5,485*
- Випускні клапани 5,456-5,471*
Діаметр головки D2:
- Впускні клапани 32,70±0,12
- Випускні клапани 27,96±0,12
Довжина клапана L:
- Впускні клапани 109,32
- Випускні клапани 107,64
Кут робочої фаски А:
- Впускні клапани 45˚ 45′
- Випускні клапани 45˚
Мінімальна товщина циліндричного поясу тарілки клапана T:
- Впускні клапани 1,15
- Випускні клапани 1,27
Хід клапанів:
- Впускні клапани 9,221
- Випускні клапани 8,075
* діаметр D1 стрижня клапана вимірюється на відстані X1
- Впускні клапани X1 = 75,14±0,35 мм;
- випускні клапани X1 = 77,5±0,35 мм;
Напрямні втулки клапанів
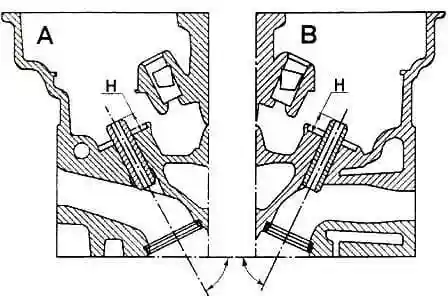
Нахил напрямної втулки впускного клапана становить 63˚30′ (рисунок 7).
Нахил напрямної втулки випускного клапана становить 66°.
Висота виступаючої частини напрямної втулки клапана Н становить для впускних та випускних клапанів 11±0,15 мм.
Маслознімні ковпачки
Зняття олійних ковпачків здійснюється за допомогою пристосування Mot1335.
Встановлення мастильних ковпачків здійснюється пристосуванням Mot1511.
Перед встановленням маслознімні ковпачки не можна змащувати.
Встановлюйте маслознімні ковпачки відповідно до вказівок на малюнку 8.
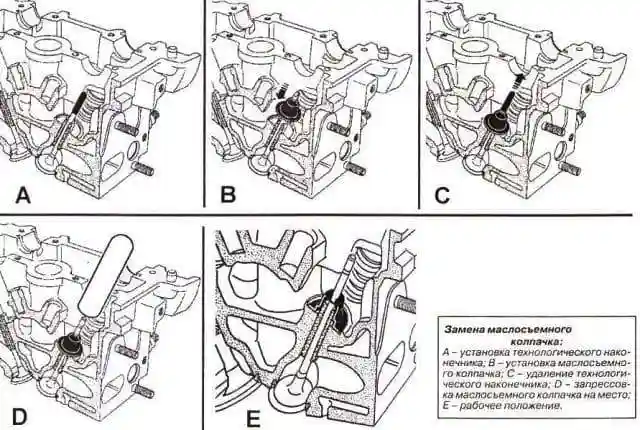
- - Вставте клапан у головку блоку циліндрів.
- - Надягніть наконечник пристосування Mot1511 на стрижень клапана (внутрішній діаметр наконечника повинен дорівнювати діаметру стрижня) (див. рис. 8).
- - Притисніть клапан до сідла.
- - Встановіть незмащений маслознімний ковпачок на наконечник.
- - Просуньте маслознімний ковпачок, проштовхнувши його через наконечник.
- - Зніміть наконечник.
- - Встановіть оправку на маслознімний ковпачок. Внутрішній діаметр оправки має збігатися з діаметром стрижня клапана.
Крім того, нижня частина оправки повинна частково упиратися в маслознімний ковпачок, по поверхні, яка є опорою шайбі пружини клапана.
- - Акуратно напресуйте маслознімний ковпачок, постукаючи долонею по верхній частині оправки, доки маслознімний ковпачок не стикнеться з головкою блоку циліндрів (див. Е, мал. 8).
- - Повторіть наведені вище операції для всіх клапанів.
Перевірка пружин клапанів
Дефекти пружин показані на малюнку 9.
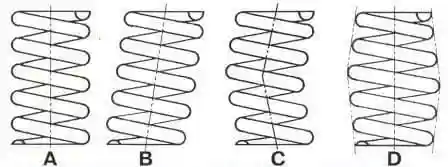
При деформаціях B та C експлуатація пружини допустима, якщо відхилення від вертикалі не більше 1,2 мм, при втраті форми (D) — пружина підлягає заміні.
Навіть при збереженні форми пружини необхідно перевірити її механічні властивості (висота під певним навантаженням).
Тільки після такої перевірки визначається придатність пружини до подальшої роботи (дивимось таблицю).
Параметри пружин клапанів
Параметр - мм
Висота у вільному стані 41,30
Висота пружини в робочому стані 23,20
Внутрішній діаметр 18,80±0,20
Зовнішній діаметр 27±0,2
Переріз дроту - Овальне
Висота / під навантаженням
34,50/180-200
24,50/563-617
За наявності нової пружини можна порівняти її характеристики з характеристиками старих пружин.
Встановіть одну за іншою нову та стару пружини через шайби на довгий болт.
Затягніть гайку болта так, щоб висота нової пружини зменшилася на 10 мм.
Виміряйте висоту старої пружини.
Якщо висота старої пружини зменшилася від 9 до 11 мм (±10%) — вона ще послужить, якщо більше — замініть стару пружину.
Перевірка зазору клапана в напрямній втулці
Перевірку зазору між стрижнем і направляючою втулкою клапана можна проводити двома способами.
Перший спосіб
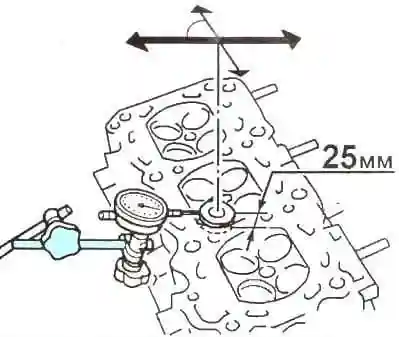
Підніміть головку клапана на 25 мм, потім виміряйте індикатором переміщення клапана у напрямку стрілок (див. мал.10) під кутом 90˚ до осі розподільчого валу.
Половина отриманої величини дасть значення зазору між стрижнем і направляючою втулкою клапана.
Другий спосіб
Виміряйте діаметр стрижня клапана та внутрішній діаметр напрямної втулки (див. мал. 11).
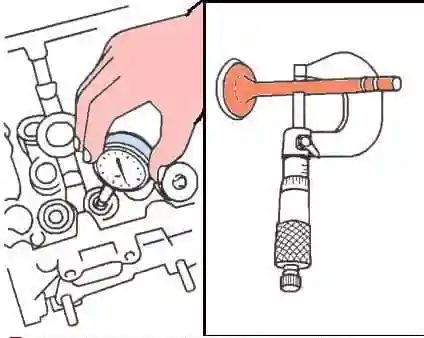
Номінальний зазор, мм:
- - впускні клапани 0,015-0,048;
- - випускні клапани 0,029-0,062.
Перевірка розподільних валів
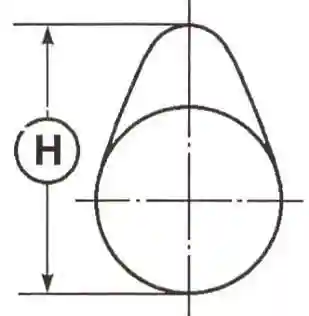
Висота кулачків Н (див. рис. 12) розподільчих валів повинна відповідати даним таблиці.
Розміри розподільних валів
Параметри мм
Осьовий зазор розподільних валів:
- впускних та випускних клапанів 0,080-0,178
- Діаметральний зазор в опорах 0,040-0,082
- Кількість опор 6
Діаметр шийок розподільного валу (див. малюнок 14):
- - шийки №1; 24,979-25,000
- - шийки № 2, 3, 4, 5; 24,979-25,000
- - шийка № 6 27,979-28,061
Висота кулачків Н (рис. 12):
- - впускних клапанів 40,661±0,030
- - випускних клапанів 40,038±0,030
Інакше замініть розподільний вал або проведіть ремонт.
Основні розміри розподільних валів наведені у таблиці.
- - Перевірте зазор шийок розподільних валів в опорах головки блоку, для цього;
- - Встановіть кришку головки блоку на місце, затягніть болти її кріплення штатним моментом затягування.
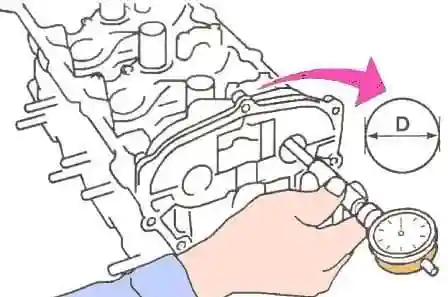
- - Нутроміром виміряйте діаметри всіх отворів в опорах розподільчого валу (див. рис. 13), результати вимірювань запишіть.
Примітка. Вимірювання потрібно проводити у вертикальній площині максимального зношування.
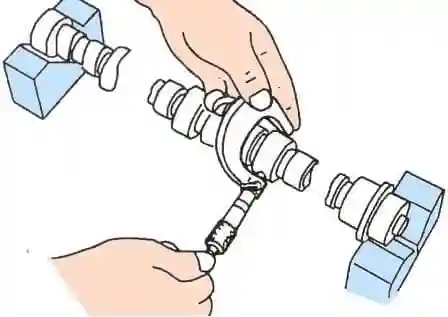
- - Мікрометром виміряйте діаметри опорних шийок розподільчого валу (див. мал. 14).
Вимірювання потрібно проводити на кожній шийці у двох перпендикулярних площинах. За базове беріть найменше значення на шийці.
- - Порівняйте результати вимірювань із гранично допустимими значеннями.
Потім розрахуйте зазори по всіх шийках і порівняйте отримані величини із гранично допустимими значеннями.
За результатами:
- - замініть розподільний вал, головку блоку або те й інше.
Примітка. При зносі розподільчого валу та головки блоку можливий відновлювальний ремонт (напилення з подальшою обробкою).
Часто ціна такого ремонту буває значно дешевшою за покупку нових деталей.
- - Якщо попередні перевірки не показали необхідності заміни деталей, перевірте осьовий зазор розподільчих валів, як описано нижче, при необхідності замініть зношені деталі.
Якщо деталі — нові, все одно проведіть перевірку, вона не важка, але важлива для впевненості в результатах ремонту.
- - Встановіть розподільні вали, забезпечивши правильність їхнього положення.
- - Встановіть кришку головки блоку циліндрів.

- - Затягніть у порядку, вказаному на рис. 15, потрібним моментом:
- - болти кріплення головки блоку циліндрів 13, 20, 22, 23, Нм 8;
- - болти кріплення кришки головки блоку з 1 по 12, з 14 по 19 і з 21 по 24, Нм 12.
- - Ослабте затягування болтів кришки головки 13, 20, 22, 23.
- - Затягніть у зазначеному порядку болти кріплення кришки головки циліндрів 13, 20, 22, 23 моментом 12 Нм.
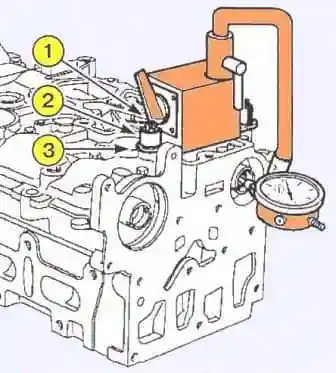
Закріпіть магнітну стійку пристрою для перевірки осьового зазору Mot588 на головці блоку циліндрів, використовуючи для цього кріпильну планку (3) пристрою Mot588, притягніть її болтами (1) кріплення масловідділювача і розпірними втулками (2), що мають наступні розміри (див. 16):
- - зовнішній діаметр, мм - 18;
- - діаметр отвору під болт, мм - 9;
- - висота, мм - 15.
- - Перевірте осьовий зазор розподільчого валу, який повинен перебувати в межах 0,080—0,178 мм.
- - Зніміть кришку головки блоку циліндрів та розподільні вали.