Removal and disassembly of the engine cylinder head is discussed in the relevant articles.
After dismantling the cylinder head, you need to wash all the parts of the head, clean them from carbon deposits.
Preparing details for inspection.
Check the seating surface of the head and the height of the cylinder head.
Height h of the block head should be 137 mm (picture 1).
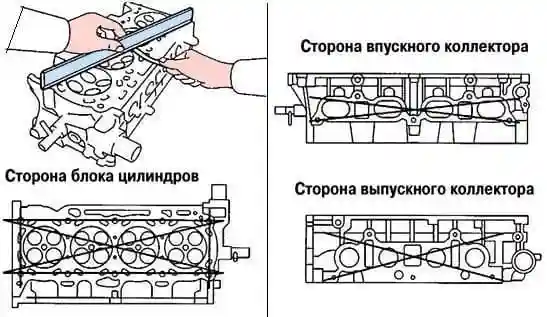
With a ruler and a feeler gauge, we check the non-flatness of the seating surfaces of the cylinder head (Figure 2).
A maximum flatness of 0.05 mm is allowed. Surface grinding is not allowed.
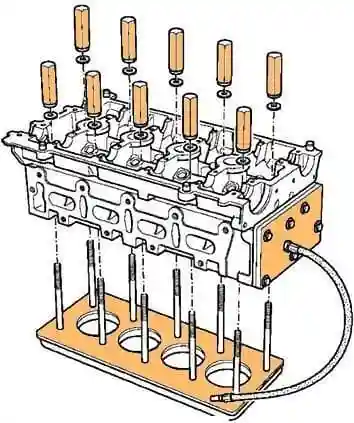
We check the cylinder head (no cracks and through corrosion) using the appropriate tool (Figure 3).
Check the length of the head bolts. The length of the bolts, excluding the head, should not exceed 117.7 mm.
If we install new bolts, then they do not need to be lubricated before installing them, used bolts should be lubricated with engine oil.
Subsequent tightening of the cylinder head bolts is not required and is not allowed, otherwise the probability of bolt destruction during unscrewing increases sharply.
Before tightening the bolts, remove the dirt and oil that remains in the threaded holes of the cylinder block.
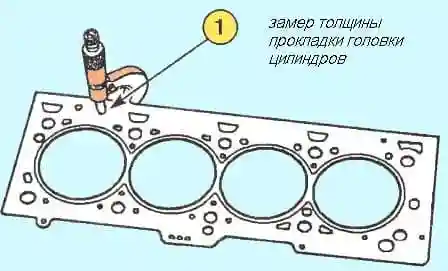
We measure the thickness of the gasket (Figure 4). The thickness is measured in the place indicated by the arrow in Figure 4.
The thickness of the new gasket should be 0.96±0.06 mm; the thickness of the crimped gasket should be 0.90±0.02 mm.
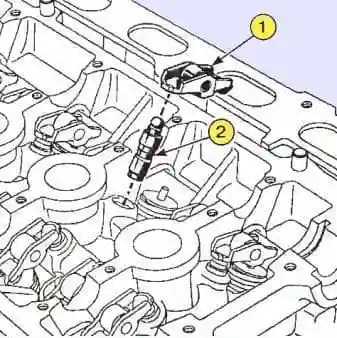
Inspecting the hydraulic tappets and rocker arms.
We measure the valves in accordance with Figure 6.
Valve sizes must match the data in the table.
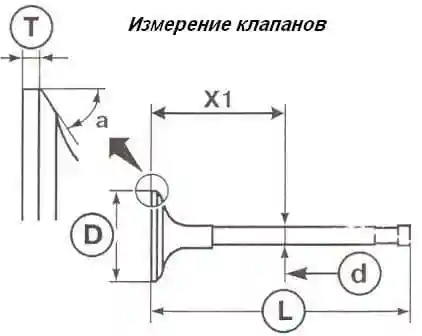
Basic valve dimensions
Name Size mm.
Stub diameter D1:
- Inlet valves 5.470-5.485*
- Exhaust valves 5.456-5.471*
Head diameter D2:
- Inlet valves 32.70±0.12
- Exhaust valves 27.96±0.12
Flap length L:
- Inlet valves 109.32
- Exhaust valves 107.64
Chamfer angle A:
- Inlet valves 45˚ 45′
- 45˚ Exhaust Valves
Minimum plate thickness T:
- Inlet valves 1.15
- Exhaust valves 1.27
Valve travel:
- Inlet valves 9.221
- Exhaust valves 8.075
* valve stem diameter D1 measured at distance X1
- Inlet valves X1 = 75.14±0.35 mm;
- exhaust valves X1 = 77.5±0.35 mm;
Valve guides
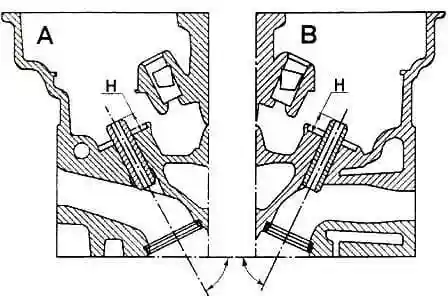
The inlet valve guide has a 63˚30′ slope (Figure 7).
The inclination of the exhaust valve guide is 66°.
The height of the protruding part of the valve guide H is 11±0.15 mm for intake and exhaust valves.
Valve seals
The valve stem seals are removed using tool Mot1335.
Installation of valve stem seals is done with tool Mot1511.
The valve stem seals must not be lubricated before installation.
Install the valve stem seals as shown in figure 8.
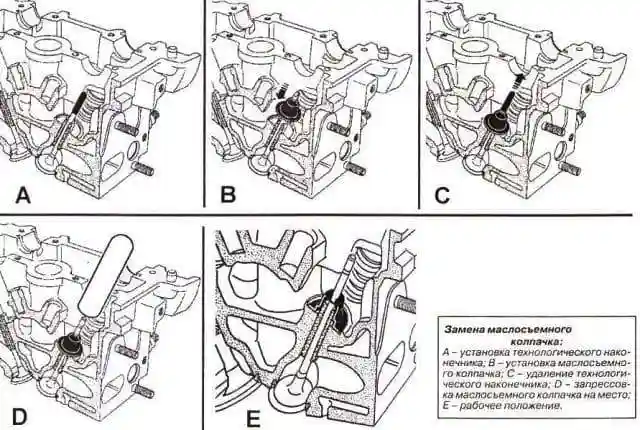
- - Insert the valve into the cylinder head.
- - Place the tip of tool Mot1511 on the valve stem (the inner diameter of the tip must be equal to the diameter of the stem) (see fig. 8).
- - Press the valve against the seat.
- - Install an unlubricated valve stem seal on the tip.
- - Slide the valve stem seal by pushing it through the tip.
- - Remove the tip.
- - Install the mandrel on the valve stem seal. The inner diameter of the mandrel must match the diameter of the valve stem.
In addition, the lower part of the mandrel should partially abut against the valve stem seal, on the surface that serves as a support for the valve spring washer.
- - Gently press on the valve stem seal by tapping the top of the mandrel with your palm until the valve stem seal contacts the cylinder head (see E, Fig. 8).
- - Repeat the above steps for all valves.
Checking valve springs
Spring defects are shown in Figure 9.
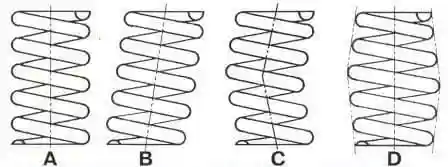
With deformations B and C, the operation of the spring is permissible if the deviation from the vertical is not more than 1.2 mm, in case of loss of shape (D) - the spring must be replaced.
Even if the shape of the spring is maintained, it is necessary to check its mechanical properties (height under a certain load).
Only after such a check is the suitability of the spring determined for further work (see table).
Valve spring parameters
Parameter - mm
Free height 41.30
Spring height in working condition 23.20
Inner diameter 18.80±0.20
Outer diameter 27±0.2
Wire section - Oval
Height / under load
34.50/180-200
24.50/563-617
If you have a new spring, you can compare its characteristics with those of the old springs.
Install the new and old springs one after the other through the washers on the long bolt.
Tighten the bolt nut so that the height of the new spring is reduced by 10 mm.
Measure the height of the old spring.
If the height of the old spring has decreased from 9 to 11 mm (± 10%) - it will still serve, if more - replace the old spring.
Checking the valve clearance in the guide sleeve
There are two ways to check the clearance between the valve stem and the valve guide.
First way
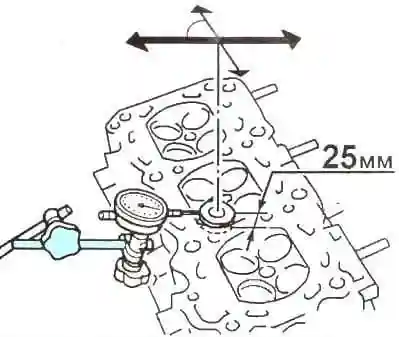
Raise the valve head by 25 mm, then measure the movement of the valve in the direction of the arrows (see Fig. 10) at an angle of 90˚ to the camshaft axis with the indicator.
Half this value will give the clearance between the valve stem and valve guide.
Second method
Measure the valve stem diameter and the inner diameter of the guide sleeve (see fig. 11).
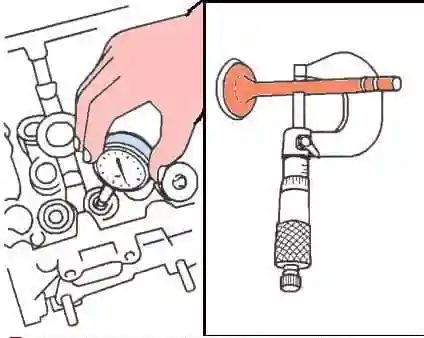
Nominal clearance, mm:
- - inlet valves 0.015—0.048;
- - exhaust valves 0.029—0.062.
Checking the camshafts
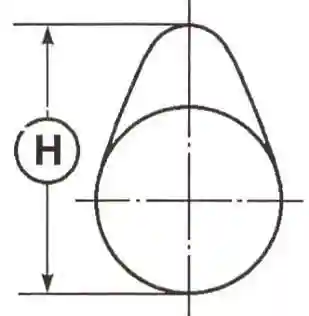
The height of the cams H (see Fig. 12) of the camshafts must correspond to the data in the table.
Camshaft dimensions
Parameters mm
Axial clearance of camshafts:
- intake and exhaust valves 0.080-0.178
- Diametric clearance in supports 0.040-0.082
- Number of supports 6
Diameter of the camshaft journals (see figure 14):
- - necks No. 1; 24,979-25,000
- - necks No. 2, 3, 4, 5; 24,979-25,000
- - Neck No. 6 27.979-28.061
Jaw height H (Fig. 12):
- - inlet valves 40.661±0.030
- - exhaust valves 40.038±0.030
Otherwise, replace the camshaft or rebuild.
The main dimensions of the camshafts are shown in the table.
- - Check the clearance of the camshaft journals in the block head bearings, for this;
- - Replace the block head cover, tighten the bolts of its fastening with the standard tightening torque.
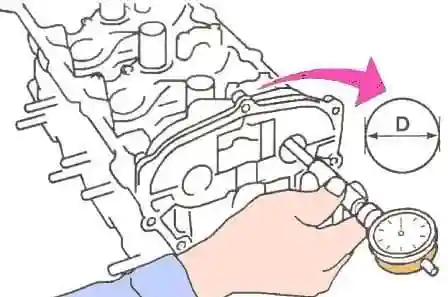
- - Using a bore gauge, measure the diameters of all holes in the camshaft bearings (see Fig. 13), write down the measurement results.
Note. Measurements must be made in the vertical plane of maximum wear.
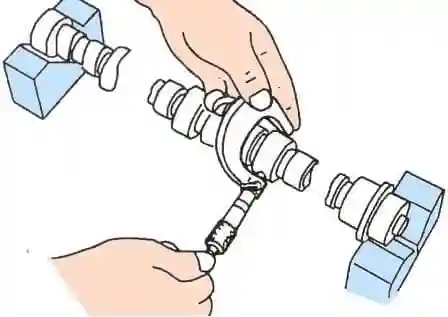
- - Using a micrometer, measure the diameters of the camshaft bearing journals (see Fig. 14).
Measurements should be made on each neck in two perpendicular planes. For the base, take the smallest value on the neck.
- - Compare measurement results with limit values.
Then calculate the gaps for all necks and compare the obtained values with the maximum allowable values.
By results:
- - replace the camshaft, the block head, or both.
Note. If the camshaft and the head of the block are worn out, reconditioning is possible (sputtering followed by processing).
Often, the price of such a repair is much cheaper than buying new parts.
- - If the previous checks did not show the need to replace parts, then check the axial clearance of the camshafts, as described below, replace worn parts if necessary.
If the parts are new, check anyway, it is not difficult, but it is important for confidence in the results of the repair.
- - Install the camshafts, making sure they are in the correct position.
- - Install the cylinder head cover.

- - Tighten in the order shown in fig. 15, required torque:
- - cylinder head bolts 13, 20, 22, 23, Nm 8;
- - bolts for fastening the head cover from 1 to 12, from 14 to 19 and from 21 to 24, Nm 12.
- - Loosen the head cover bolts 13, 20, 22, 23.
- - Tighten the cylinder head cover bolts 13, 20, 22, 23 in the order shown to 12 Nm.
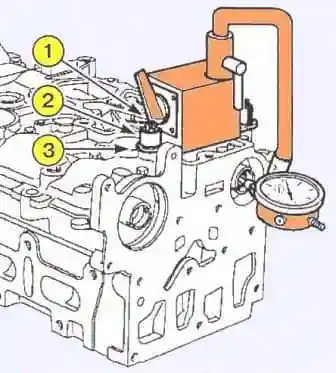
Fix the magnetic pole of the axial clearance tester Mot588 to the cylinder head using the mounting plate (3) of tool Mot588, tighten it with the oil separator mounting bolts (1) and spacers (2) having the following dimensions (see fig. .16):
- - outer diameter, mm - 18;
- - bolt hole diameter, mm - 9;
- - height, mm - 15.
- - Check the axial clearance of the camshaft, which should be between 0.080-0.178 mm.
- - Remove the cylinder head cover and camshafts.