Before inspecting the parts of the gearbox, thoroughly clean, remove all deposits with a brush or scraper and clean the holes and splines from possible contamination; then flush (with kerosene, thinner, etc.) to remove and dissolve any remaining oil.
Blow the parts with compressed air and gently wipe them.
Blow out the bearings especially carefully, directing the jet of compressed air so that the rings do not rotate quickly.
Crankcase and covers
There should be no cracks on the crankcase, and wear or damage on the surface of the bores for bearings, seals, etc..
There must be no damage to the mating surfaces of the clutch housing, rear and bottom covers to prevent oil leakage.
Smooth out minor damage with a file.
If the parts are too damaged or worn, replace them with new ones.

Check the condition of the front cover and make sure that the input shaft does not touch it when rotating.
If shaft and cover misalignment is found, replace damaged parts.
Check if the oil drain hole in the cap is clogged (shown by the arrow in Figure 1).
Clean the drain plug.
Glands
Check the seals for damage, excessive wear, and uneven sealing lips.
Wear of the working edges of the seals in width is allowed no more than 1 mm.
If even a slight defect is found, replace the seals with new ones.
Shafts
On the working surfaces and on the splines of the output shaft, damage and excessive wear are not allowed.
The rolling surfaces of the needles at the front end of the shaft should be free of roughness and burrs.
Check the condition of the needle rolling surface in the input shaft bore.
Inspect the intermediate shaft, which should not be chipped or excessively worn teeth.
The surface of the reverse gear shaft must be perfectly smooth, without any signs of binding.
The size of the mounting gap between the axle and the bushing of the intermediate reverse gear is 0.056-0.09 mm, the maximum allowable gap is 0.15 mm.
Check the clearance by measuring the diameter of the axle and the hole of the gear bushing.
For new parts, the axle diameter is 19.079-19.094 mm, and the inner diameter of the pressed bushing is 20.05-20.07 mm.
Remove minor irregularities on the surfaces with fine emery cloth.
In case of large damages and deformations, replace the shafts with new ones.
Gears
The gears must not show any damage or excessive tooth wear.
Pay special attention to the surface condition of the engagement teeth.
The contact patch of the gear teeth should be located over the entire surface, which should be smooth and without signs of wear.
Check the meshing gap between the gear teeth, the installation value of which should be 0.10 mm; wear limit - gap -0.20 mm.
The mounting gap between the bushings and gears of I and V gears and between the secondary shaft and gears of II and III gears should be 0.05-0.10 mm; wear limit - gap -0.15 mm.
When wear exceeds the allowable limits, replace the gears with new ones.
Bearings
Ball or roller bearings must be in perfect condition. Their radial clearance must not exceed 0.05 mm.
Pressing the inner ring against the outer ring with your fingers, turn one of them in both directions, while rolling should be smooth.
No damage is allowed on the surface of balls or rollers and the raceways of the rings.
Replace damaged bearings with new ones.
When replacing the front bearing of the input shaft, use the ejector A.40006 (Figure 2); in this case, the flywheel can not be removed.
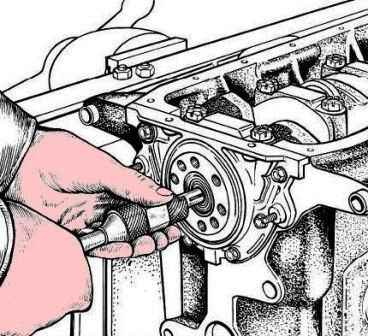
Stems and forks
Deformation of shift forks is not allowed.
The rods should slide freely without significant clearance in the crankcase bores.
Check the condition of the locking crackers of the rods, springs and retainer balls. replace parts that show signs of seizing or wear with new ones.
Hubs, clutches and synchronizer rings.
Check for signs of seizing on the hubs of the couplings, especially on their sliding surfaces.
Pay special attention to the condition of the ends of the coupling teeth.
Excessive wear on the surface of the blocking rings is not allowed.
They must be replaced if nor rest against the end of the synchronizer clutch.
Remove any irregularities that prevent free sliding with a velvet file.
Replace parts that are worn out more than the allowable limits.
Pay special attention to the condition of the short teeth on the synchronizer hubs.
Replace parts with crumpled edges at the ends with new ones.
Gearbox assembly technology
Assemble the gearbox in the reverse order of disassembly.
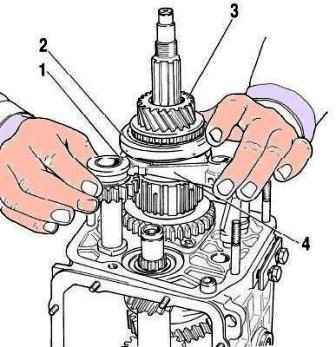
Removing the reverse idle gear, fifth gear assembly with synchronizer and fork: 1 - reverse idle gear: 2 - fifth gear engagement clutch: 3 - fifth gear and reverse gear: 4 - fifth gear and reverse engagement fork move
Note that:
- - the axis of the intermediate reverse gear is attached before the shafts are installed in the gearbox housing with a torque of 78 Nm (7.8 kgcm);
- - before installing the fifth gear and reverse fork rod into the crankcase, install a distance sleeve on it;
- - the inner ring of the bearing is pressed onto the gear unit of the fifth gear and reverse gear, and the outer ring into the seat of the rear cover;
- - the rear bearing of the secondary shaft is pressed onto the shaft to facilitate the installation of the rear cover;
- - intermediate gear 1 (see Fig. 3) reverse, gear 3 and fork 4 install at the same time;
- - tighten the gear block mounting bolt with a torque of 78 Nm (7.8 kgcm);
- -before installation, cover the working surface of the oil seals with Litol-24 grease;
- - when installing oil seals and bearings, use mandrels 41.7853.4028, 41.7853.4032, 41.7853.4039;
- - when assembling the gear selection mechanism, apply grease Litol-21 or LSTs-15 on the surfaces of the gear selection lever that are in contact with the ball joint and the thrust joint housing.
And also apply grease to the inside surface of the spherical washer of the ball joint;
- - when assembling the gearshift control drive, apply grease LSTs-15 to the inner surface of the ball joint housing;
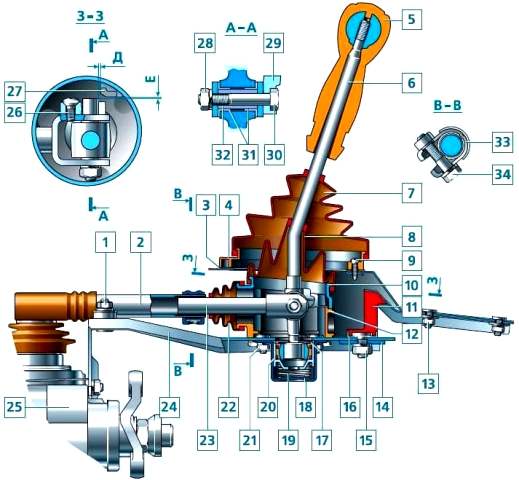
Drive for controlling the gearshift mechanism: 1 - nut for fastening the base plate; 2 - thrust of the gearbox control drive; 3 - manhole cover gasket; 4 - hatch cover of the gear lever; 5 - gear lever handle; 6 - gear lever; 7 - a cover of the gear lever; 8 - sealing case; 9 - screw securing the hatch cover; 10 - the upper housing of the gear lever; 11 - rear support; 12 - lower housing of the gear lever; 13 - nut for fastening the rear support; 14 - rear support washer; 15 - nut; 16 - spacer ring; 17- retaining ring; 18 - body of the ball bearing; 19 - spring of the gear lever; 20 - ball bearing slider; 21 - nut for fastening the body of the ball joint; 22 - protective cover; 23 - thrust tip; 24-base plate; 25 - gearbox; 26 - screw for fastening the blocking stop; 27- reverse block pad; 28 - a nut of a bolt of fastening of a tip of draft; 29 - blocking emphasis; 30 - a bolt of fastening of a tip of draft; 31 - bushing; 32 - remote bushing; 33 - control drive rod clamp; 34 - clamp bolt
- - when installing the gearshift control drive, holding the gearshift lever and the base plate in the relative position determined by the dimensions (see Figure 4) D = (1.5 + 0.5) mm, E = (1 + 0 .5) mm and W = (81.5 + 0.5) mm, tighten the torque control drive rod clamp bolt 24.5 Nm (2.5 kgcm);
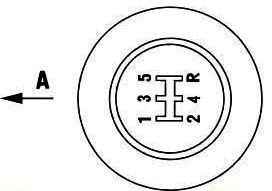
- - when installing the gear selector lever handle, ensure its position relative to the direction of movement of the vehicle, as indicated in view A (Fig. 5).