Disassembly of a partially synchronized gearbox
Disassemble in the following order:
Remove the side cover with the switch mechanism.
Remove the input shaft bearing cap
Turn the input shaft with a cutout towards the countershaft drive gear and remove the input shaft with rollers and synchronizer blocking ring.
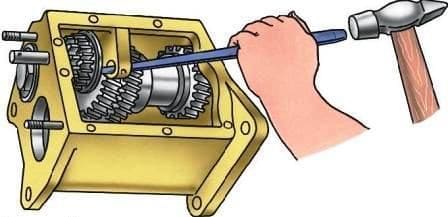
Remove the locking screw of the reverse gear assembly axle and press the axle back, removing the reverse gear assembly (fig. 1).
Remove the plates securing the output shaft rear bearing.
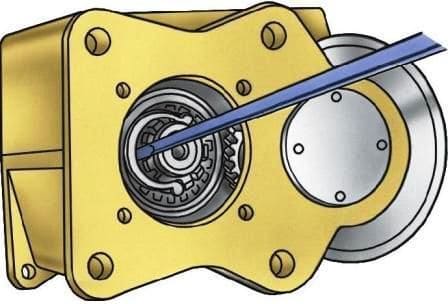
Remove the circlip of the synchronizer hub (Fig. 2) and pull the output shaft back.
In this case, all gears will be removed from the shaft, and the bearing will remain on the shaft.
Unscrew the cover of the intermediate shaft front bearing with a special wrench.
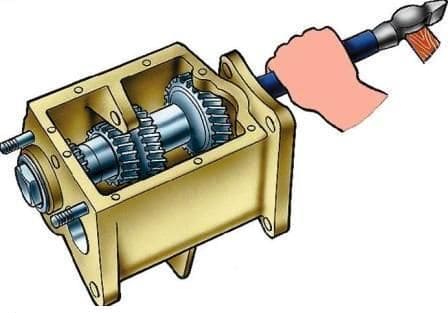
Unscrew the countershaft front bearing nut with a special wrench and pull the countershaft back together with the bearing (Fig. 3). In this case, the drive gears of II and III gears will be removed from the shaft.
Unscrew the input shaft bearing nut, which has a left-hand thread, with a special wrench.
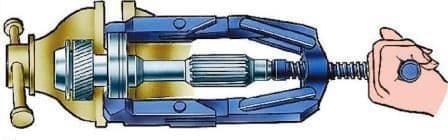
Remove the bearing from the input shaft using a puller (fig. 4).
Remove the countershaft rear bearing using a puller. The bearing bolt has a left-hand thread and is locked by a Belleville spring.
Disassembly of the synchronized gearbox
Disassemble in the following order:
Remove the side cover with the switch mechanism.
Using the M8 threaded hole in the rear end of the reverse idle gear axle, press the axle back, remove the gear.
Remove the input shaft bearing cap.
Remove the countershaft front bearing cap.
Remove the intermediate shaft rear bearing bolt (the bolt has a left-hand thread) and remove the bolt's belleville spring.
Using a puller, remove the input and output shaft rear bearings by their circlips.
Remove the intermediate shaft rear bearing circlip.
Install the box so that the intermediate shaft is at the top, move the intermediate shaft forward until the intermediate shaft gear assembly stops in the crankcase.
Feed the layshaft together with the rear bearing back until the inner race of the front bearing comes out of the rollers and the rear bearing out of the crankcase.
Remove the countershaft rear bearing using a puller.
Install the gearbox with the sunroof under the shift mechanism up.
Remove the input shaft, the 4th gear blocking ring, the output shaft assembly (supporting the 1st gear spacer ring) and the countershaft assembly from the gearbox housing.
Disassembling the secondary shaft
Remove the thrust washer and 1st gear with needle bearing.
Remove the circlips of the synchronizer hubs using a puller and a thrust washer.
Remove the 1st and 2nd gear synchronizer together with the 2nd gear gear.
Remove the circlip, key and 2nd gear bearing.
Remove the 3rd and 4th gear synchronizer together with the 3rd gear gear.
Remove the circlip, key, spacer and 3rd gear bearing.
Assembly of the synchronized gearbox
Assemble the gearbox, starting with the subassembly of its components, in the following order:
Input shaft assembly
Lap the blocking ring on the shaft taper to a size of 0.8-1.25 mm, as shown in fig. 5
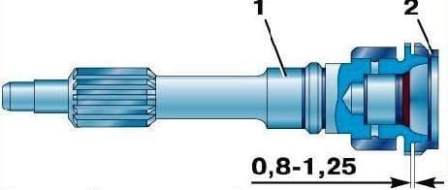
Press the ball bearing against the stop with the sealing ring towards the bearing nut.
Screw on the bearing fastening nut (left-hand thread) and lock it by punching into the groove of the shaft.
Put grease into the hole of the shaft and insert the rollers (14 pieces).
Synchronizer assembly
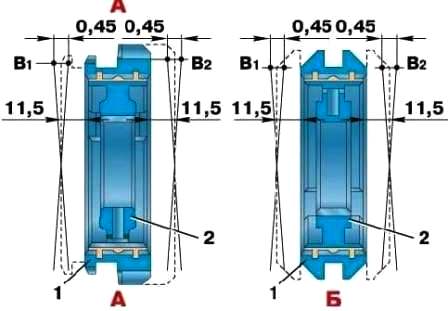
Choose a set of clutch and synchronizer hub with minimum clearances in free movement according to fig. 6 or use factory matched kits 469-1701117 and 469-1701138.
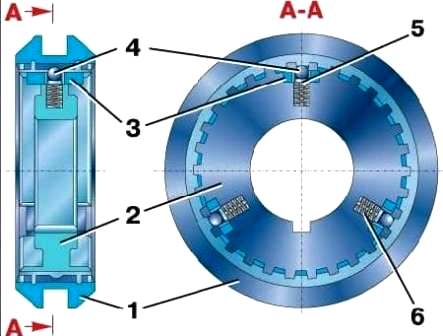
Insert three springs into the hub (fig. 7), three guide springs, three balls and three crackers and install the clutch on the hub (the clutch of I and II gears is made in one piece with the reverse gear).
Install crackers with the side with holes of smaller diameter towards the coupling.
Assembly of output shaft
Install the 3rd gear needle bearing, bearing spacer, circlip and key.
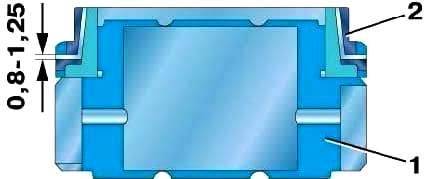
Lap the synchronizer ring on the cone of the 3rd gear gear to a size of 0.8-1.25 mm, as shown in fig. 8.
Lubricate the bearing with gear oil, install the 3rd gear gear with blocking ring, thrust ring, install the 3rd and 4th gear synchronizer and the circlip with a cut to the hub key.
Fit the synchro-rings on the cones of the 1st and 2nd gears to a size of 0.8–1.25 mm, as shown in fig. 8.
Install 2nd gear needle bearing, circlip.
Lubricate the bearing with transmission oil, install the 2nd gear with blocking ring, thrust ring, install the 1st and 2nd gear synchronizer.
Install the thrust ring, retaining ring, 1st gear gear with blocking ring and lubricated bearing, install the spacer ring (oil deflector) so that the pin of the secondary shaft falls into the groove of the spacer ring (oil deflector).
Install the locking sleeve and secure it (the locking sleeve will make it easier to install the output shaft assembly into the transaxle case).
Reverse gear subassembly with bearing
Produced in the same way as assembling the reverse gear with the gearbox bearing, partially synchronized.
Assembly of gearshift mechanisms of cars of the UAZ-31512 and UAZ-3741 families is carried out similarly to the assembly of gearshift mechanisms of a partially synchronized gearbox.
Assembly of the gearbox from sub-assemblies
Further assembly of the gearbox is carried out in the following order:
Insert the assembled (with gear train, circlip and roller bearing inner race) intermediate shaft into the gearbox housing.
Insert the assembled output shaft into the gearbox housing, remove the locking sleeve.
Install (press in) the output shaft rear bearing with the retaining ring installed on it.
When pressing the secondary shaft, make an emphasis with a mandrel against the end of the shaft neck under the synchronizer hub.
When pressing, pay attention to the correct installation of the thrust washer of the 1st gear gear.
Install (press-fit) the assembled input shaft into the gearbox housing so that the groove for the bearing circlip is recessed into the housing.
Reinstall the countershaft by engaging the gears.
Install (press in) the rear bearing of the intermediate shaft with the retaining ring installed on it until the inner race of the bearing stops against the end of the shaft and the retaining ring against the end of the crankcase.
Install the front bearing outer race with cage and rollers onto the front end of the intermediate shaft.
Fix the rear bearing pro intermediate shaft with a bolt with a Belleville spring mounted on it.
Strengthen the input shaft so that the circlip groove comes out of the gearbox housing, install the circlip and seat the input shaft until the circlip rests against the crankcase.
Install (press in) the intermediate shaft front bearing cover until the ends of the cover and crankcase match.
Install the gasket on the front end of the crankcase so that the cutout in it coincides with the oil drain hole.
Install the bearing cover onto the input shaft so that the oil drain channel aligns with the notch in the gasket.
Fix the cover with four bolts and spring washers. Under the two left bolts, install the bracket of the clutch release bearing return spring.
Fix the output shaft rear bearing to the shaft using the thrust and retaining rings.
Insert the reverse gear shaft into the hole in the crankcase from the side of the rear mating plane.
Insert the reverse gear into the crankcase so that the axle enters it from the side opposite the shift fork groove.
Press the reverse gear axle into the crankcase as far as it will go according to fig. 9.
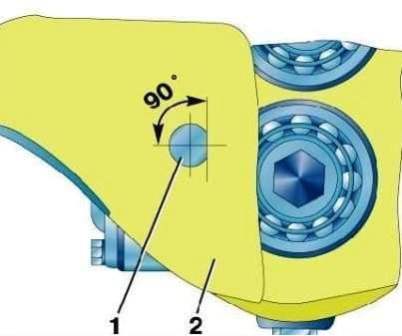
Assembly of the gearbox from sub-assemblies
Further assembly of the gearbox is carried out in the following order:
Insert the assembled countershaft into the gearbox housing.
From the back, sequentially put on it the spacer ring, the 2nd gear gear, the 3rd gear gear and the countershaft drive gear.
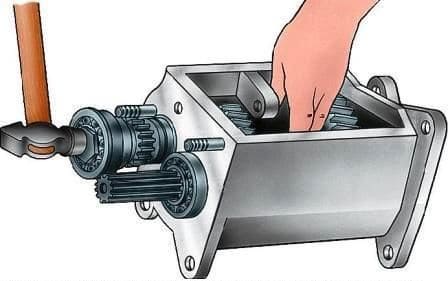
Install the shaft (fig. 10) with the bearing until the bearing ring stops in the crankcase.
Install the washer, bearing and tighten the special nut on the front end of the intermediate shaft.
Unlock the nut to secure it. Axial movement of gears along the shaft is not allowed.
Screw the cover with the rubber sealing ring flush with the end of the crankcase into the front opening of the crankcase.
Do not overtighten the cap to avoid damaging the O-ring.
Lubricate the necks of the II and III gears of the assembled output shaft with liquid oil and, inserting it from behind into the upper hole of the crankcase, sequentially put on it the gear of the 1st gear, the gear of the 2nd gear, the gear of the 3rd gear with the synchronizer ring, the thrust washer, the synchronizer assembly.
Shut down the output shaft bearing together with the shaft to the groove in the bearing.
Lock the entire set of gears with the circlip in the groove on the front end of the mainshaft. The gears of II and III gears should turn freely by hand.
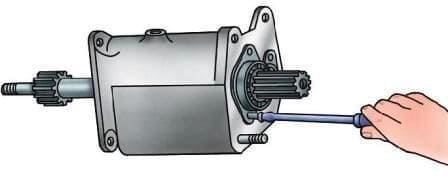
Lock the rear bearing (fig. 11) of the secondary shaft with two plates with screws.
Install the blocking ring, lapped to the input shaft cone, into the synchronizer hub.
Insert the assembled mainshaft into the gearbox housing, with the notch down to the countershaft drive gear.
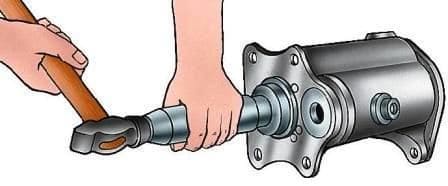
Using a mandrel, install the shaft (fig. 12) and the bearing until the bearing ring stops in the crankcase.
Install the gasket on the front end of the crankcase so that the cutout in it coincides with the oil drain hole.
Install the bearing cover onto the input shaft so that the oil passage of the cover coincides with the oil drain hole in the crankcase.
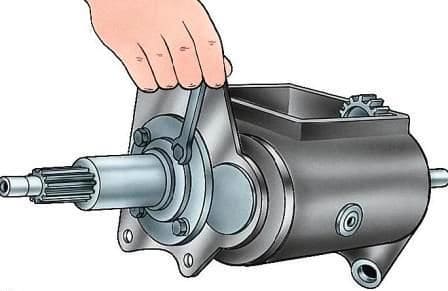
Fix the bearing cover (fig. 13) with four bolts and spring washers.
Under the two left bolts, install the clutch release bearing return spring bracket.
The bolts are tightened e with a torque of 12 to 18 Nm (1.2–1.8 kgf m).
Lubricate the reverse gear block bearing with liquid lubricant, insert the gear block with the large crown against the crankcase bore, and insert the axle into the block through the crankcase bore.
Press the axle of the gear cluster into the crankcase so that the hole in the axle matches the M6 threaded hole in the crankcase wall.
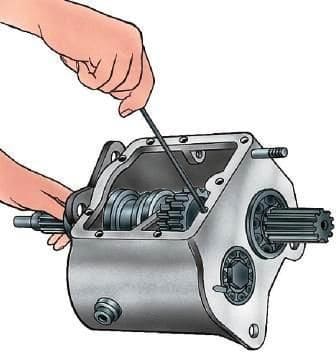
Insert the locking screw flush with the crankcase split plane (fig. 14).
Install the shift mechanism on the gearbox and secure it with bolts and spring washers.
Before installing the shifter, make sure the gears in the gearbox and the shifter forks are in the neutral position.
Tighten the bolts with a torque of 12 to 18 Nm (1.2–1.8 kgf m).
Partially synchronized gearbox assembly
Assemble the gearbox, starting with the subassembly of its components, in the following order:
Input shaft assembly
Lap the blocking ring on the shaft taper to a size of 0.8-1.25 mm, as shown in fig. 15.
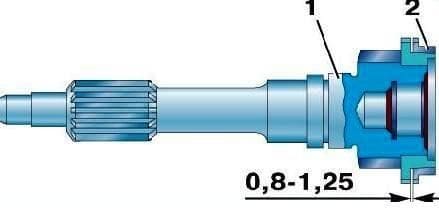
Install the oil deflector.
Press the ball bearing onto the shaft until it stops at the end of the oil deflector so that the groove on the outer ring of the bearing is shifted away from the ring gear.
Screw on the bearing fastening nut (left-hand thread) and lock the nut by punching into the groove of the shaft.
Mount the thrust washer on the ball bearing.
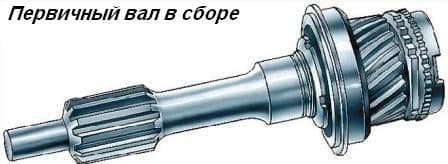
Put grease into the hole of the shaft and insert the rollers (14 pieces).
Insert the roller locking ring.
Assembly of the secondary shaft
Install the oil deflector.
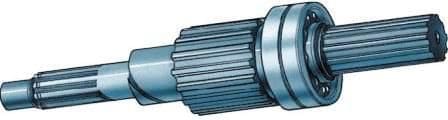
Press on the double row ball bearing with the marking towards the gearbox.
Secure the bearing to the shaft with a thrust washer and retaining ring.
Intermediate shaft assembly
Press the bearing all the way onto the rear end of the intermediate shaft so that the groove on the outer ring of the bearing is offset towards the gear.
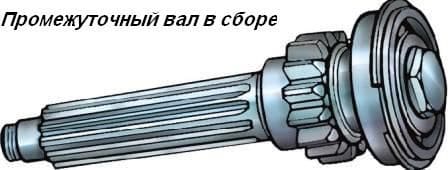
Install the belleville spring with the bulge towards the bolt head.
Tighten the bearing bolt (left-hand thread).
Mount the thrust washer on the bearing.
3rd Gear Kit Assembly
Lap the synchronizer ring on the cone of the 3rd gear gear to a size of 0.8-1.25 mm, as shown in fig. 16.
Reverse gear set subassembly with bearing
Install the circlip into one of the two grooves in the hole in the gear assembly.
Lay the thrust ring, bearing and another thrust ring in succession into the hole.
Insert the retaining ring securely into the groove.
Synchronizer assembly
Select a clutch and synchronizer hub kit with minimum clearances for free movement according to or use a kit 451D-1701116-11, selected by the manufacturer.
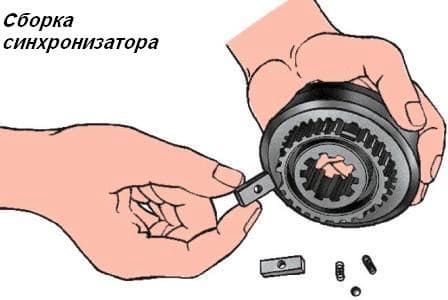
Insert three springs (fig. 17), three crackers, three balls into the hub and install the shift clutch on the hub.
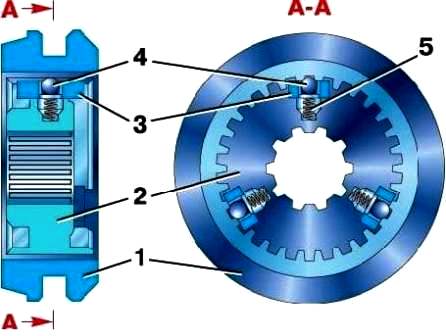
Moreover, position the longer part of the hub towards the end of the coupling, which has a shaped chamfer (Fig. 18).
The holes in the breadcrumbs are stepped. Install crackers with the side with holes of smaller diameter, and the side of the coupling.
It is possible to install whole crackers with protruding hemispheres that act as balls in synchronizers.
Assembly of the intermediate shaft cover
Install the rubber ring into the groove of the cover.