The K4M engine is gasoline, four-stroke, four-cylinder, in-line, sixteen-valve, with two overhead camshafts.
The order of operation of the cylinders: 1-3-4-2, counting - from the flywheel.
Power system - distributed fuel injection (Euro 4 toxicity standards).
An engine with a gearbox and a clutch form a power unit - a single unit mounted in the engine compartment on three elastic rubber-metal supports.
The right support is attached to the top cover of the timing gear drive, and the left and rear support are attached to the gearbox housing.
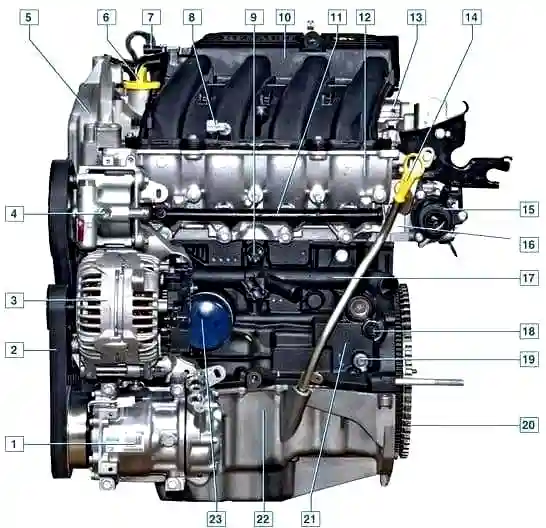
Front on the engine (in the direction of the car) are located: inlet pipeline; oil filter; oil level indicator; low oil pressure indicator sensor; fuel rail with injectors; knock sensor; coolant pump inlet pipe; generator; power steering pump; air conditioning compressor.
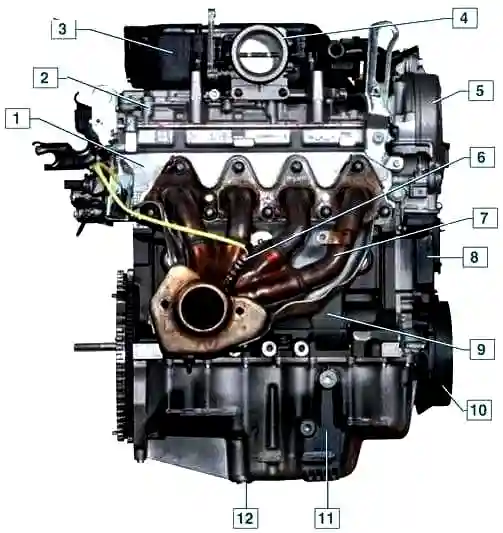
Behind the engine are:
- - air filter housing with idle speed control;
- - exhaust manifold with a control oxygen concentration sensor;
- - starter.
Right - coolant pump; timing gear and coolant pump drive (toothed belt); drive of auxiliary units (poly V-belt).
On the left are: flywheel; crankshaft position sensor; thermostat; thermostat housing with coolant temperature sensor.
Top - coils and spark plugs; oil filler neck; a receiver with sensors for absolute pressure and intake air temperature, a throttle assembly with a throttle position sensor.
The engine cylinder block is cast iron, the cylinders are bored directly in the block.
In the lower part of the cylinder block there are five crankshaft main bearing supports with removable covers, which are attached to the block with special bolts.
The bores in the cylinder block for the bearings are machined with the covers installed, so the covers are not interchangeable and are marked on the outer surface to distinguish them (the covers are counted from the flywheel side).
On the end surfaces of the middle support, sockets are made for thrust half rings that prevent axial movement of the crankshaft.
To cool the pistons during engine operation, their bottoms are washed from below with engine oil through special nozzles pressed into the cylinder block in the area of the second and fourth supports (on both sides of the supports) of the main bearings.
Crankshaft with five main journals and four crankpins.
The shells of the main and connecting rod bearings of the crankshaft are steel, thin-walled with an anti-friction coating applied to the working surfaces of the shells.
The shaft is equipped with four counterweights integral with the shaft.
To supply oil from the main journals to the connecting rod journals, channels are made in the necks and cheeks of the shaft.
At the front end (toe) of the crankshaft are installed: an oil pump drive sprocket, a timing gear drive pulley (timing) and an auxiliary drive pulley.
The toothed pulley is fixed on the shaft by a protrusion that fits into the groove on the toe of the crankshaft.
Similarly, it is fixed on the shaft and the drive pulley is auxiliary x units.
The crankshaft is sealed with two oil seals, one of which (on the timing drive side) is pressed into the cylinder block cover, and the other (on the flywheel side) is pressed into the socket formed by the surfaces of the cylinder block and the main bearing cover.
A flywheel is attached to the crankshaft flange with seven bolts.
It is cast from cast iron and has a pressed steel crown for starting the engine with a starter. In addition, a ring gear for the crankshaft position sensor is cut into the flywheel.
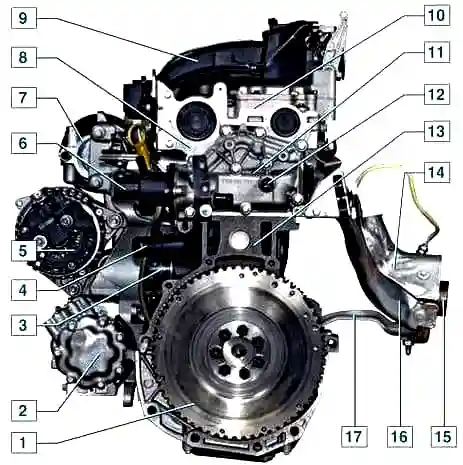
Connecting rods - forged steel, I-section, processed together with covers.
The covers are attached to the connecting rods with special bolts and nuts.
With their lower (crank) heads, the connecting rods are connected through liners to the connecting rod journals of the crankshaft, and the upper heads are connected through the piston pins to the pistons.
Piston pins are tubular steel.
The pin, pressed into the upper head of the connecting rod, rotates freely in the piston bosses.
Pistons are made of aluminum alloy.
The piston skirt has a complex shape; barrel-shaped in longitudinal section, and oval in transverse section.
Three grooves for piston rings are machined in the upper part of the piston.
Two upper piston rings are compression rings, and the lower one is oil scraper.
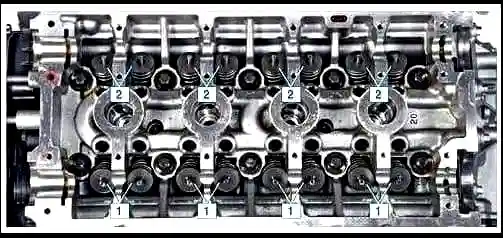
Cylinder head cast from aluminum alloy, common to all four cylinders.
The cylinder head is centered on the block with two bushings and secured with ten screws.
A non-shrinking metal gasket is installed between the block and the head.
On opposite sides of the cylinder head there are windows for intake and exhaust channels.
Spark plugs are installed in the center of each combustion chamber.
Steel valves, arranged in two rows in the cylinder head, V-shaped, two intake and two exhaust valves for each cylinder.
The inlet valve plate is larger than the outlet valve.
The valve seats and guides are pressed into the cylinder head.
Oil caps are put on top of the valve guides.
The valve closes under the action of a spring.
The lower end rests on the washer, and the upper end rests on the plate, which is held by two crackers.
The folded crackers have the shape of a truncated cone on the outside, and on the inside they are equipped with persistent beads that enter the groove on the valve stem.
Two camshafts are mounted on top of the cylinder head.
One shaft drives the intake valves of the gas distribution mechanism, and the other drives the exhaust valves.
Eight cams are made on each shaft - an adjacent pair of cams simultaneously controls the valves (inlet or exhaust) of each cylinder.
The design feature of the camshaft is that the cams are pressed onto the tubular shaft.
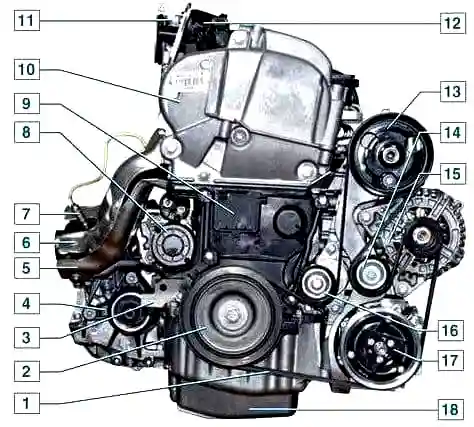
Distribute supports (beds) shafts (six bearings for each shaft) detachable - located in the cylinder head and in the head cover.
Camshaft drive - toothed belt from the crankshaft pulley.
On each camshaft, on the side of the toothed pulley, a thrust flange is made, which, during assembly, enters the groove of the cylinder head, thereby preventing axial movement of the shaft.
The camshaft pulley is fixed on the shaft not with the help of a tight fit, key or pin, but only due to the friction forces that occur on the end surfaces of the pulley and shaft when the pulley fastening nut is tightened.
The toe of the camshaft is sealed with an oil seal, put on the neck of the shaft and pressed into the socket formed by the surfaces of the cylinder head and the head cover.
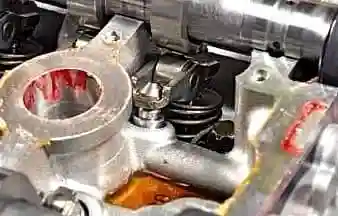
Valves are driven by camshaft lobes through valve levers.
To increase the life of the camshaft and valve levers, the cam of the shaft acts on the lever through a roller rotating on the axis of the lever.
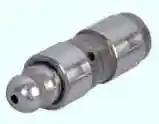
The hydraulic bearings of the valve levers are installed in the sockets of the cylinder head.
The oil inside the hydromount comes from the line in the cylinder head through the hole in the hydromount body.
Hydrosupport automatically ensures backlash-free contact of the camshaft cam with the valve lever roller, compensating for wear on the cam, lever, valve stem end, seat chamfers and valve disc.
Engine lubrication - combined.
Under pressure, oil is supplied to the crankshaft main and connecting rod bearings, camshaft bearings and valve lever hydraulic bearings.
Other engine components are splash lubricated.
The pressure in the lubrication system is generated by a gear oil pump located in the sump and attached to the cylinder block.
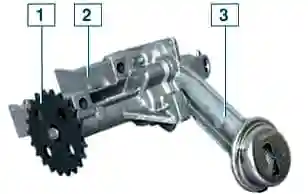
The oil pump is driven by a chain drive from the crankshaft.
The pump drive sprocket is mounted on the crankshaft under the cylinder cover.
A cylindrical belt is made on the sprocket, along which the front crankshaft oil seal works.
The sprocket is installed on the crankshaft without tension and is not fixed with a key.
When assembling the engine, the pump drive drive sprocket is clamped between the timing gear pulley and the crankshaft shoulder as a result of the package of parts being pulled together by the accessory drive pulley mounting bolt.
The torque from the crankshaft is transmitted to the sprocket only due to the frictional forces between the end surfaces of the sprocket, the toothed pulley and the crankshaft.
If the accessory drive pulley bolt is loosened, the oil pump drive sprocket may begin to rotate on the crankshaft and the engine oil pressure will drop.
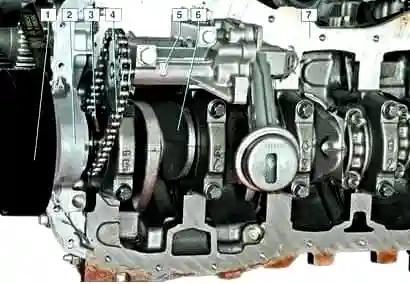
The oil receiver is made in one piece with the cover of the oil pump housing.
The cover is fixed with five screws to the pump body.
The pressure reducing valve is located in the cover of the pump housing and is kept from falling out by a spring retainer.
The oil from the pump passes through the oil filter and enters the main oil line of the cylinder block.
Oil filter - full-flow, non-separable.
From the main line, oil flows to the main bearings of the crankshaft, piston cooling nozzles and further (through the channels in the crankshaft) to the connecting rod bearings of the shaft.
Two vertical channels in the cylinder block supply oil from the main line to the cylinder head - to the extreme supports of the camshafts from the side of the plugs and the valve hydraulic supports.
Through the grooves and drillings in the extreme bearing journals of the camshafts, oil enters the shafts and then through the drillings in other shaft journals to the rest of the camshaft bearings.
From the cylinder head, oil flows through vertical channels into the engine sump.
Crankcase ventilation system - closed, forced type.
Gases that have penetrated from the combustion chambers of the cylinders through the piston rings into the crankcase of the engine enter through the channels in the block and the cylinder head into the head cover.
After passing through the oil separator located in the cylinder head cover, crankcase gases are cleaned of oil particles and then flow through the air filter housing, throttle assembly, receiver and inlet pipeline into the engine cylinders.
Control, power, cooling and exhaust systems are described in the relevant articles