The drive gear of the main gear is made integral with the shaft (shank) and is installed in the neck of the gearbox on two tapered bearings.
The outer rings of the bearings are pressed into the sockets of the neck, and the inner rings are put on the shank
A spacer is installed between the inner rings; when the shank nut is tightened, the sleeve deforms, providing a constant preload to the bearings.
The preload of the bearings is controlled by the moment of turning the drive gear (other parts are not installed).
For new bearings, the turning torque should be in the range of 157-197 Ncm, for bearings after a run of 30 km or more - 39-59 Ncm.
At the same time, the shank nut is tightened with a torque of 118-255 Nm, periodically checking the rotation of the drive gear.
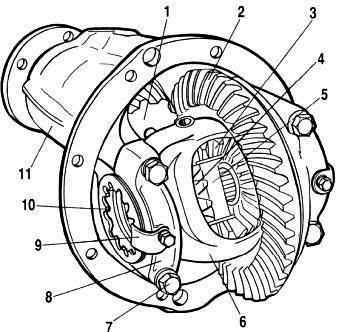
If the specified turning torque has already been reached and the tightening torque of the nut is less than 118 Nm, it is necessary to replace the spacer sleeve with a new one, as the old one is too deformed.
Replacing the bushing is also necessary in the case when the turning torque turned out to be higher than the permissible one (due to inattention when tightening).
If the main pair or pinion bearings are replaced, the thickness of the shim must be re-selected.
It is mounted on the shaft between the drive gear and the inner ring of the large bearing.
The final drive gear is attached to the differential box flange with special bolts without washers. These bolts cannot be replaced by any other.
The differential box rotates in two tapered bearings.
Their preload, as well as the gap between the teeth of the final drive gears, is regulated by nuts wrapped in split bearing beds.
The side gears are installed in the cylindrical sockets of the differential box and rest on it through the support washers.
These washers are selected in thickness so that the gap between the teeth of the satellites and side gears is within 0.0-0.1 mm.
The pinion gears are mounted on an axle with constant engagement with side gears.
The axis has spiral grooves for supplying lubricant to rubbing surfaces.
The axle shaft rests at one end on a single-row ball bearing (with protective washers and a lifetime supply of grease) installed in the seat of the rear axle beam, and the other (splined) end enters the side gear.
The inner race of the bearing is locked to the axle shaft by a locking ring fitted with an interference fit (shrink fit).
The outer ring of the bearing is fixed by a plate, which, together with the oil deflector and the brake shield, is fastened with four bolts and nuts to the rear axle beam.
Determination of gearbox faults by noise
Troubleshoot in the following order.
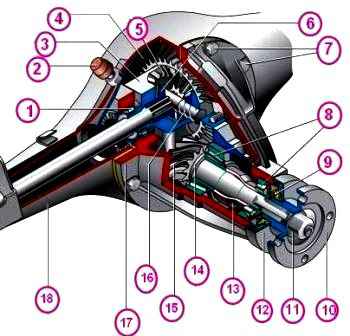
Test 1
To clearly identify the nature of the noise, drive the car on the highway at a speed of approximately 20 km/h.
Then gradually increase your speed up to 90 km/h, listening for different types of noise at the same time and noticing the speed at which they appear and disappear.
Release the throttle pedal and release engine speed without braking.
While slowing down, watch the noise change, as well as the moment when the noise increases.
The noise usually comes and goes at the same speeds, both when accelerating and when decelerating.
Test 2
Accelerate the vehicle to approximately 100 km/h, place the shift lever in neutral and allow the vehicle to roll freely to a stop; follow ha noise detector at different deceleration speeds.
The noise that depends on the manipulation of the accelerator pedal comes from the main pair.
Bearings can also make noise when coasting: the bearings of the drive gear make noise with a hiss and rumble, and the bearings of the differential and axle shafts produce a low-frequency rumble.
Challenge 3
When the car is stationary and braked, turn on the engine and, gradually increasing its speed, compare the resulting noises with those noticed in previous tests.
Noises that are similar to test 1 will indicate that they are not gearbox noise and are caused by other nodes.