We check and repair the unit during the overhaul of the engine.
All cylinder block measurements should be taken with the block on a level surface and all main bearing caps installed.
Check the surface of the cylinder for hones.
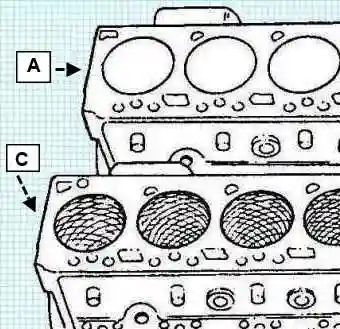
Crossing lines should be visible on the surface of the cylinder, running at an angle of 20 - 25 ° relative to the upper plane of the cylinder block.
Hone the cylinders if necessary.
Check the main bearing beds.
- a) Install the main bearing caps without shells.
- b) Tighten the main bearing bolts.
Tightening torque 176 Nm
Measure the diameter of the main bearing bed.
Main bearing bed diameter 87.983 - 88.019 mm
Note: If the diameters of the main bearing seats do not correspond to the nominal ones, check the correct installation and orientation of the main bearing caps.
If the main bearing caps are installed correctly, replace the cylinder block.
Check the flatness of the cylinder block with a precision ruler and feeler gauge.
Maximum flatness:
- - along 0.076 mm;
- - across 0.051 mm.
Check for small bumps or defects.
If present, the upper surface of the cylinder block must be sanded.
Note: Grinding the upper surface of the cylinder block is only permitted if the required piston protrusion can then be achieved.
After grinding the upper surface of the cylinder block, the use of repair gaskets is provided.
If the required piston protrusion cannot be achieved after grinding, replace the cylinder block.
Measure the inside diameter of the cylinder.
Note: When measuring, honing or reboring cylinders, all main bearing caps must be installed and bolts tightened to rated torque.
Check the surface of the cylinders for damage and excessive wear.
Using a bore gauge, measure the cylinder diameter at 4 points 90° apart at the extreme positions of the piston stroke.
Measure the cylinder diameter at a depth of more than 50 mm from the top surface of the cylinder block.
- Cylinder bore 102.01 - 102.03 mm
- Maximum ovality 0.038mm
- Max taper 0.076mm
Check the inside diameter of the camshaft bore with the sleeve removed.
Maximum diameter 59.248 mm
Check the tappet bores for damage and wear.
Push bore diameter 16,000 - 16,055 mm
Cylinder block repair
Note: do not allow foreign particles formed during repair operations to enter the engine oil channels.
Failure to do so will result in engine failure.
After boring or honing at a third-party repair shop, it is recommended that you always flush and blow out the cylinder block.
Before repairing the cylinders, be sure to seal the oil channels and the tappet holes in the upper part of the cylinder block with waterproof tape.
Restoring honing of the cylinder liner mirror when gloss is formed on the walls (if necessary).
Honing ensures that oil is retained on the cylinder walls, which is necessary for the normal operation of the piston rings.
Honing is allowed only if the dimensions of the cylinders correspond to the nominal ones.
Note: New piston rings will not fit tightly in glossy cylinders.
Use a round honing head (#382Z612 or equivalent) at 300-400 rpm, one cycle in the vertical direction per second.
Use a high quality honing oil or a mixture of equal parts SAE30W engine oil and diesel fuel.
Note: The vertical passages must be smooth and continuous throughout the height of the cylinder.
Check the cylinder bore after 10 passes.
The angle of the crossed lines depends on the rotational speed and vertical movement of the honing head.
Too high or too low a travel speed will cause this angle to be abnormal.
On a properly honed surface of the cylinder bore, the honing lines should run at an angle of 20 - 25° relative to the upper plane of the cylinder block.
Rinse the cylinder block with hot water and detergent concentrate until all abrasive residues are removed.
Wash the surface of the cylinders with solvent. Dry the cylinder block with compressed air.
Replacing the cylinder liner
The cylinder block must be bored out to fit overhaul liners.
The use of repair sleeves allows the use of pistons and rings of nominal size.
Rebore the cylinder to the desired size.
Cylinder bore diameter 104.500 - 104.515 mm
Maximum cylinder bore depth 192.65 mm
As a result, a step 6.35 mm high should form at the bottom of the cylinder, on which the sleeve will be seated.
Thoroughly clean the cylinder block of metal filings.
Place the repair sleeves in a freezer below -12°C for at least 1 hour.
Note: take out the shells one at a time just before installation.
Apply Loctite620 to the top of the cylinder block bore just before installing the liner
Put on protective gloves, use your hands to push the cooled sleeve into the cylinder block as far as possible.
Using a press, press the liner into the cylinder block until it contacts the step at the bottom of the bore.
Rebore the installed sleeve to nominal size.
Nominal diameter - 101.956 mm
Make the top of the liner less than 0.05mm above the surface of the cylinder block
After boring with a honing stone, make a 1.25 mm deep chamfer at a 15° angle to the vertical
After boring the repair sleeve, two-stage honing is required to complete the cylinder.
Use quality honing equipment.
When honing, the speed of rotation of the honing head should be 300 - 400 rpm, and the up and down travel time should be 1 second.
Use a good quality honing oil or mix equal parts SAE30W engine oil and diesel fuel.
Use 80 grit silicon carbide stones for the first honing step.
Hone the cylinders to the final size.
Diameter 102.00 - 102.04 mm
Use 285 grit silicon carbide stones for second honing or final honing
Make 15 - 20 passes, giving the desired hone angle.
After completion of processing, thoroughly rinse and blow out all channels from chips, dirt, metal particles and oil.