This article will cover the preparation of the cylinder block, crankshaft and piston for engine assembly
The following are not allowed: cracks, breaks, dents, gouges, crushed edges, thread damage of more than two turns, presence of traces of wear and work hardening on the teeth of the sprockets (visual inspection).
Parts whose technical condition does not meet the requirements: auxiliary equipment drive belt, timing chain, timing chain tensioner, timing chain tensioner shoe, timing chain damper, cylinder head gasket, cylinder head mounting bolts, camshaft phase regulator filter, crankshaft pulley mounting bolt, exhaust manifold mounting stud nuts, exhaust manifold mounting studs, oil filter, flywheel mounting bolts, connecting rod cap mounting bolts, The crankshaft main bearing cap bolts, crankshaft main bearing shells, connecting rod bearing shells, oil pump drive chain, oil pump chain tensioner must be replaced.
All sealing parts must be replaced
Preparing the Cylinder Block
The crankshaft main journal bore diameter classes are given in Table 1
The main journal diameter classes are indicated on the cylinder block, Figure 1
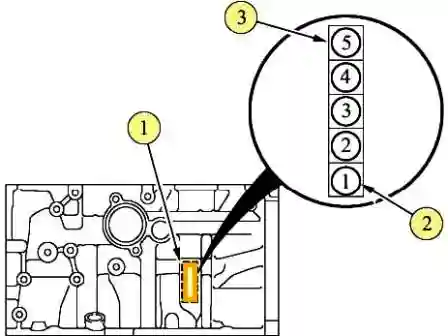
The maximum diameter "D" of the cylinders, which requires replacement of the cylinder block is 78.10 mm.
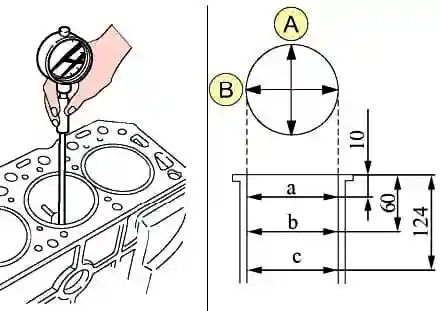
Measuring the cylinder diameter is carried out in three belts in the longitudinal and transverse directions, as shown in Figure 2.
The limiting size is determined by the most worn cylinder using the bore gauge NI 50-100-1
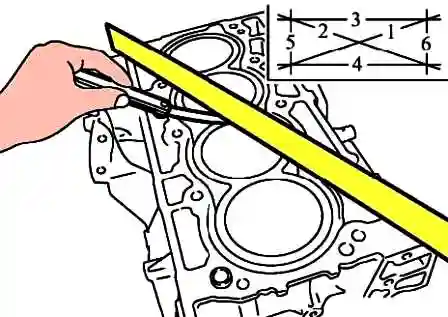
Using a straightedge and a set of feeler gauges, measure the non-flatness of the cylinder block surface mating with the head
Make the measurement as shown in Figure 3
The maximum permissible non-flatness of the cylinder block surface mating with the cylinder head is 0.1 mm per 100 mm of length
Checking the cylinder block reinforcement
Make the measurements as shown in Figure 4
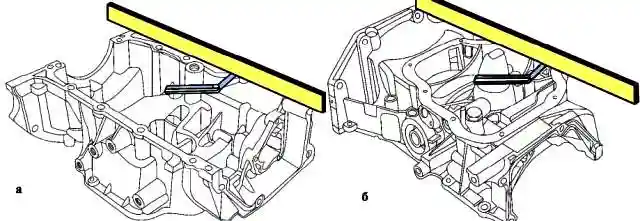
The maximum non-flatness of the mating surfaces of the cylinder block reinforcement on the cylinder block side and on the oil pan side is 0.1 mm per 100 mm of length.
Crankshaft
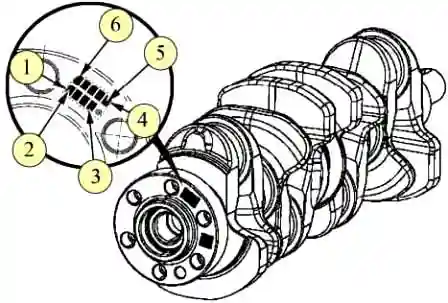
The marking of the size groups of the connecting rod and main journals of the crankshaft is applied to the flange for installing the flywheel, Figure 5.
We take measurements using a micrometer type MK 75-1
Classes of diameters of the holes of the main journals of the crankshaft
Letter on cylinder block indicating the diameters of the main bearings of the crankshaft - Diameter of the hole of the main journals of the crankshaft in the cylinder block, mm:
- A - 51.997 - 51.998
- B - 51.998 - 51.999
- С - 51,999 - 52,000
- D - 52,000 - 52,001
- E - 52.001 - 52.002
- F - 52.002 - 52.003
- G - 52.003 - 52.004
- Н - 52.004 - 52.005
- J - 52.005 - 52.006
- K - 52.006 - 52.007
- L - 52,007 - 52,008
- M - 52.008 - 52.009
- N - 52.009 - 52.010
- P - 52.010 - 52.011
- R - 52.011 - 52.012
- S - 52.012 - 52.013
- T - 52.013 - 52.014
- U - 52.014 - 52.015
- V - 52.015 - 52.016
- W - 52.016 - 52.017
Classes crankshaft journal diameters are given in Table 2:
Letter, crankshaft journal diameter class - Crankshaft journal diameters, mm:
- A - 39.970 - 39.971
- B - 39.969 - 39.970
- C - 39.968 - 39.969
- D - 39.967 - 39.968
- E - 39.966 - 39.967
- F - 39.965 - 39.966
- G - 39.964 - 39.965
- H - 39.963 - 39.964
- J - 39.962 - 39.963
- K - 39.961 - 39.962
- L - 39.960 - 39.961
- M - 39.959 - 39.960
- N - 39.958 - 39.959
- P - 39.957 - 39.958
- R - 39.956 - 39.957
- S - 39.955 - 39.956
- T - 39.954 - 39.955
- U - 39.953 - 39.954
Crankshaft main journal diameter classes are given in Table 3
Letter, main journal diameter class on the crankshaft - Crankshaft connecting rod journal diameters, mm:
- A - 47.978 - 47.979
- B - 47.977 - 47.978
- C - 47.976 - 47.977
- D - 47.975 - 47.976
- E - 47.974 - 47.975
- F - 47.973 - 47.974
- G - 47,972 - 47,973
- H - 47.971 - 47.972
- J - 47.970 - 47.971
- K - 47.969 - 47.970
- L - 47.968 - 47.969
- M - 47.967 - 47.968
- N - 47.966 - 47.967
- P - 47.965 - 47.966
- R - 47.964 - 47.965
- S - 47.963 - 47.964
- T - 47.962 - 47.963
- U - 47.961 - 47.962
- V - 47.960 - 47.961
- W - 47.959 - 47.960
Check the radial runout of the crankshaft main journals using a prism, an ICh-10 indicator, and a ШМ-ПВ-8 tripod
The radial runout should not be more than 0.01 mm
Preparation and inspection of pistons
Pistons are not allowed to have chips or cracks of any kind, burnouts, or destruction of partitions
The outer diameter D, Figure 5, of the piston, measured at a distance of L=10 mm, should be 77.948 – 77.958 mm (micrometer type MK 100-1).

The diameter of the piston pin hole should be 19.008 – 19.014 mm (bore gauge type NI 18-50-1).
Checking the connecting rods
The diameter D, Fig. 6, of the piston pin hole in the upper head of the connecting rod should be 18.958 – 18.978 mm (bore gauge type NI 18-50-1).
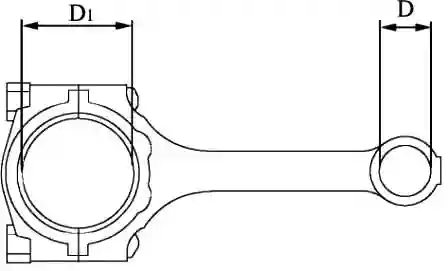
By the diameter of the hole D1 in the lower head, the connecting rods are divided into several classes.
The class of the connecting rod and the cylinder number are marked on the cover and on the body of the connecting rod.
Letter, class of the hole in the lower head of the connecting rod - Diameters of the holes in the lower head of the connecting rod, mm:
- A - 43.000 - 43.001
- B - 43.001 - 43.002
- C - 43.002 - 43.003
- D - 43.003 - 43.004
- E - 43.004 - 43.005
- F - 43.005 - 43.00б
- G - 43.006 - 43.007
- Н - 43.007- 43.008
- J - 43.008 - 43.009
- К - 43.009 - 43.010
- L - 43.010 - 43.011
- М - 43.011 - 43.012
- N - 43.012 - 43.013
The classes of hole diameters in the lower head of the connecting rod are given in Table 4 (bore gauge type NI 18-50-1)
Checking the thickness of the lower connecting rod head
The thickness of the lower connecting rod head should be within 18.748 – 18.800 mm (micrometer type MK 25-1).
Checking the piston pins
No traces of wear or scoring on the piston pins after pressing out are allowed (visual inspection).
Check the outer diameter of the piston pin.
The outer diameter of the piston pin should be within 18.996 – 18.998 mm (micrometer type MK 25-1).
Check the length of the piston pin.
The length of the piston pin should be within 53.4 mm (vernier caliper type ШЦ-1-125-0,1).
We discussed the preparation of the cylinder head in the previous article