Wheel drives with equal angular velocity joints are used to transmit torque from the main gear to the drive wheels at different wheel angles and suspension travels
When designing, they try to make drives of the same length, since this condition ensures the equality of forces and moments that occur on the drive wheels.
It is difficult to fulfill this condition on a vehicle with a transverse powertrain, therefore, on such vehicles, as a rule, the right-hand drive is much longer than the left-hand drive.
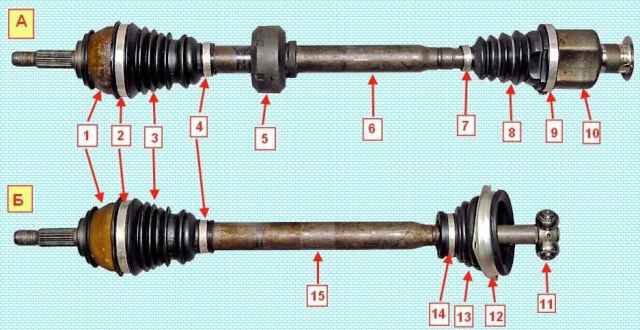
Drives of the right "A" and left "B" wheels: 1 - outer hinge housing; 2.9 - large clamps of hinge covers; 3, 8,13 - covers of drive hinges; 4, 7 - small clamps of hinge covers; 5 - damper; 6 - right wheel drive shaft; 10 - body of the inner hinge of the right wheel drive; 11 - three-studded inner joint of the left wheel drive; 12 - holder of the cover of the inner hinge of the left wheel drive; 15 - wheel drive shaft
For a car with a manual transmission, design solutions were applied to bring together the lengths of the drives of the drive wheels.

This was achieved due to the different design of the internal hinges.
In order to increase the length of the left wheel drive, the internal drive joint is made inside the gearbox housing.
In order to reduce the length of the right wheel drive, the inboard joint housing is moved away from the gearbox housing.
For this, an additional element was introduced into the design of the gearbox - a splined shaft, which is made in one piece with the side gear of the differential.
A rubber damper is installed on the right wheel drive shaft.
External internal hinges of drives (tripod type) have different designs.
The hinges of the drives are covered with dirt covers.
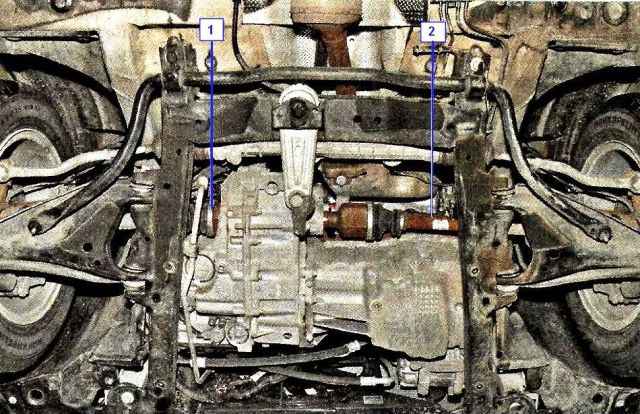
Internal hinge of the drive provides the possibility of angular movements of the suspension and compensates for the mutual movements of the suspension and the power unit by changing the length of the drive.
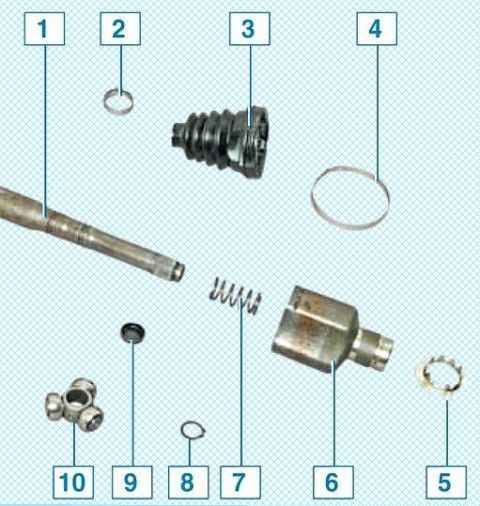
The inner hinge is collapsible.
At the splined end of the drive shaft, on the side of the internal hinge, there is a hub with three spikes - a three-stud, on each of the spikes (trunnion) of which there is a roller with an outer spherical surface, rotating on a needle bearing.
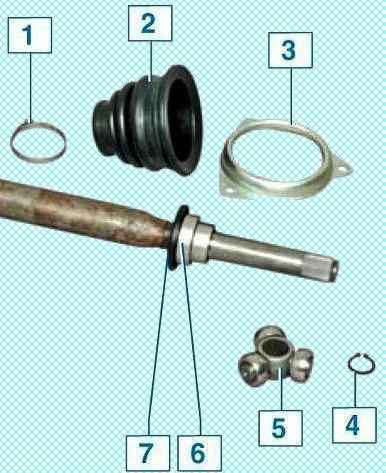
The needle bearing is fixed against displacement along the tire axis by a locking ring, put on a retaining ring located in the groove of the tire.
The three-stud is fixed on the drive shaft with a retaining ring.
The mutual movements of the suspension and the power unit are compensated by the movement of the three-stud rollers in the longitudinal grooves of the internal hinge body.
The inner joints of the left and right wheel drives are not interchangeable.
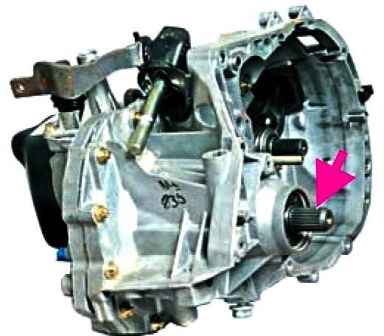
The tip of the housing of the inner hinge of the right wheel drive is put on the splined shaft coming out of the gearbox housing and made integral with the side gear of the differential (for clarity, shown on the dismantled gearbox).
A spring installed inside the housing of the right wheel drive inner joint ensures that the joint housing is pressed against the side gear of the differential during suspension operation.
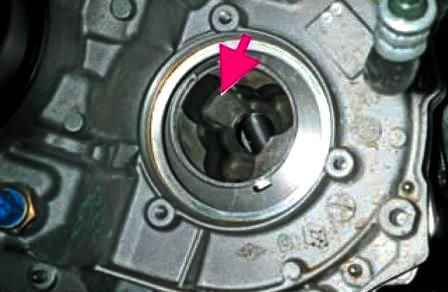
The body of the inner joint of the left wheel drive is located in the gearbox and is made integral with the left side gear of the differential (shown with the drive removed).
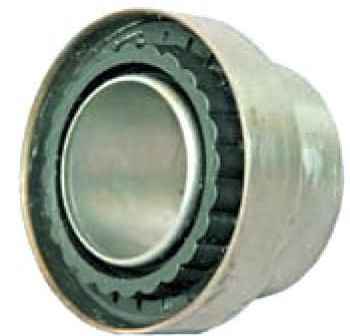
A needle bearing assembly with an oil seal is installed on the left wheel drive shaft behind the three-pin inner joint.
The bearing inner race is pressed onto the drive shaft and rotates with it.
A protective cover of the inner joint is clamped to the stationary outer ring of the bearing.
At its other end, the hinge cover is attached to the gearbox housing using a metal flange holder.
An oil seal installed in the outer ring of the bearing prevents oil leakage from the gearbox along the drive shaft.
The bearing seal is protected from dirt by a plastic dirt deflector mounted on the shaft.
If the mudguard of the hinge or the bearing seal is damaged, oil will leak from the gearbox.
The outer drive joint provides torque transmission at various angles of rotation of the drive wheels.
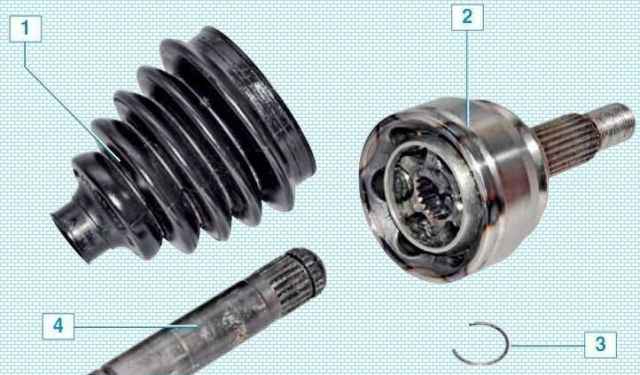
The outer hinge consists of a body, a separator, a cage and six balls, which are placed in the profiled grooves of the body and cage.
The separator constantly keeps the balls in the bisector plane between the body and the hinge cage and ensures uniform transmission of rotation from the cage to the body.
In the body and cage, the grooves are made along the radius.
Hinge parts are made with high precision, balls are selected from the same sorting group.
Therefore, the worn joint is replaced as an assembly.
The hinge cage is mounted on the splines of the shaft and secured against longitudinal displacement with a retaining ring.
The splined shank of the outer joint housing, at the end of which a thread is cut, is inserted into the front wheel hub and fastened with a nut.
The outer joints of the drives of the left and right wheels are the same.
Replenishment or replacement of lubricant, as well as any other maintenance of the wheel drive shafts during the operation of the vehicle is not required.
The owner of the car only needs to monitor the condition of the protective covers of the hinges and the clamps for their fastening, as well as the condition of the oil seal of the bearing of the inner hinge of the left drive.
A damaged boot must be replaced as soon as possible, since the ingress of dirt into the lubricant causes rapid wear of the hinge parts and failure, and damage to the rubber boot or seal of the left drive inner joint bearing will lead to oil leakage from the gearbox and gearbox failure out of order.
When installing a new hinge cover, the clamps of its fastening should also be replaced with new ones.
The bearing (complete with the oil seal) of the inner joint of the left wheel drive is supplied as spare parts along with a protective cover.