UMP-4178, -4179, -4218 or ZMZ-4021, -4104 engines are installed on the car.
They all have basically the same design
Engine - carbureted, four-cylinder, in-line, four-stroke, with two valves per cylinder.
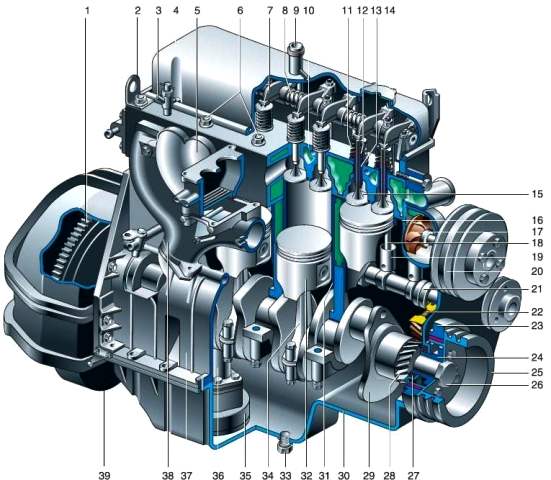
Engine: 1 - flywheel; 2 - mounting eye; 3 - heater valve; 4 - cylinder head cover; 5 - inlet pipeline; 6 - nuts of the studs for fastening the cylinder head; 7 - valve rocker; 8 - axis of rocker arms; 9 - crankcase ventilation pipe; 10 - cylinder head; 11 - valve springs; 12 - oil cap; 13 - valve sleeve; 14 - oil filler cap; 15 - valve; 16 - cylinder head gasket; 17 - coolant pump; 18 - rod; 19 - pusher; 20 - fan pulley; 21 - camshaft; 2 - driven gear of the camshaft drive; 23-torsional vibration damper; 24 - pulley hub; 25 - pulley; 26 - pulley bolt; 27- cuff; 28 - camshaft drive gear; 29 - crankshaft; 30 - oil pan; 31 - cylinder liner; 32 - piston; 33 - oil drain plug; 34 - connecting rod; 35 - oil intake; 36 - oil pump; 37 - cylinder block; 38 - exhaust manifold; 39 - crankcase
Cylinder firing order: 1-2-4-3.
The cylinder block is cast from aluminum alloy.
Cast-iron cylinder liners, removable (wet type) or cast into a block on the UMZ-4218 engine
Motor Specifications
The sealing of "wet" sleeves along the lower joint is provided by copper gaskets or rubber rings.
An aluminum clutch housing is bolted to the rear end of the block.
Pistons are cast from aluminum alloy.
Each of them has two compression rings and one oil scraper ring.
Compression rings - cast iron, top - chrome-plated, bottom - tin-plated.
Piston pins are of a floating type, they are held from axial movement by retaining spring rings.
Steel, forged, I-section connecting rods with a split lower head, the cover of which is fastened with two bolts and nuts.
A bronze bushing is pressed into the upper (piston head) of the connecting rod.
The crankshaft is cast iron, cast, full support, with counterweights, dynamically balanced assembled with a flywheel and installed in the cylinder block on five split main plain bearings.
Main and connecting rod bearings are made in the form of liners made of steel tape coated with anti-friction aluminum-tin alloy.
The shaft is kept from axial displacement by two thrust rings, which are installed on both sides of the front main bearing.
The ends of the crankshaft are sealed with rubber cuffs.
On the ZMZ-4021 and ZMZ-4104 engines, the rear end of the crankshaft was sealed with asbestos cord packing.
A hub is pressed onto the front toe of the crankshaft, to which a damper pulley is bolted.
The cylinder head is cast from aluminum alloy.
It has cast-iron seats and ceramic-metal valve bushings pressed into it.
The head is attached to the block with ten studs and nuts through a metal-asbestos gasket.
On the right side, the exhaust manifold and intake manifold are attached to the head.
The cast iron camshaft is installed in the bored holes of the lower part of the cylinder block.
On engines manufactured before 1996, the camshaft was mounted on anti-friction bushings pressed into the cylinder block.
At its front end, on the key, a textolite or polyamide helical drive gear is installed.
The camshaft cams, when it rotates, act on cylindrical pushers that are installed in the holes of the block.
Aluminum push rods with steel spherical tips actuate valve rockers mounted on a common fixed steel axle.
On the short arm of the rocker there is a screw with a lock nut for adjusting the clearance in the valve actuator.
Thin-walled bronze bushings are pressed into the rocker holes.
The valves are made of heat-resistant steel.
Each valve is equipped with two right-handed and left-handed springs and is installed in a ceramic-metal guide bush made of sintered copper-iron-graphite powder with molybdenum disulfide.
The valve stems are sealed with rubber oil seals that prevent oil penetration into the combustion chambers.
The top of the block head is closed with a stamped steel cover.
Combined lubrication system - under pressure and spray.
Under pressure, the main and connecting rod bearings of the crankshaft, camshaft bearings, rocker bushings, upper tips of the push rods are lubricated.
Camshaft and accessory drive gears are lubricated with a jet of oil, and the rest of the parts are splash lubricated.
The cylinder walls are additionally lubricated by a jet of oil, which is ejected from the hole in the lower head of the connecting rod.
The gear oil pump is driven together with the ignition distributor sensor by a screw gear from the camshaft.
The pump body is aluminum, and its working spur gears are made of sintered metal.
Oil is drawn by a pump from a stamped steel sump through a meshed oil intake, then it passes the pump, a full-flow filter and is fed into the oil line.
The oil pressure in the system is limited by the pressure reducing valve.
On ZMZ engines, the oil filter is collapsible, with a replaceable filter element.
UMP engines use a non-separable oil filter.
There are bypass and anti-drain valves in the filter housing.
An emergency oil pressure signal lamp sensor (triggered when the pressure drops to 0.4–0.8 kgf / cm3) and an oil pressure indicator sensor are connected to the oil line.
An oil cooler with a tap is also integrated into the lubrication system.
The radiator is connected parallel to the main oil flow and is installed before the radiator of the cooling system.
When the tap is open, part of the oil passes through the radiator, cools and drains into the sump.
The radiator valve should be opened when the air temperature is above 20°C and (regardless of temperature) when driving in difficult road conditions.
The crankcase ventilation system is closed, forced, with the removal of crankcase gases into the intake system through an oil separator with a vacuum regulator.
The power unit (engine complete with clutch, gearbox and transfer case) is attached to the vehicle frame on four supports, two of which are located on the sides of the cylinder block.
The other two are supported by a plate installed between the gearbox and transfer case.
Possible engine malfunctions and solutions
The engine does not start, but the crankshaft is turned by the starter
- No fuel supply or insufficient fuel supply:
Clogged strainers in the fuel intake, carburetor, fuel pump or fine fuel filter, clogged fuel sediment filter
Wash the filters in solvent, blow with compressed air
- Clogged fuel line
Blow out the fuel line with compressed air, after opening the fuel tank caps
- Air ingress through fuel line connections
Tighten fuel line connections
- The fuel pump valves are leaking, the diaphragm is damaged, the diaphragm spring is weakened, the drive lever is worn
Check the fuel pump, repair or replace it
- The float sticks in the carburetor when the float mechanism valve is closed
Remove the jam, flush and blow out the valve with compressed air
- Water frozen in fuel filters, carburetor or fuel lines
Place the car in a warm room. Warm up the pipelines and remove water from the fuel system by blowing with compressed air
- The air damper does not close completely (when starting a cold engine)
Adjust damper actuator
- Clogged fuel jets
Clean and blow jets with compressed air
- - Carburetor float chamber overflows:
- - The float sticks when the float mechanism valve is open
Remove jamming, replace worn parts
- The tightness of the float is broken
Replace float
- The tightness of the valve of the float mechanism is broken due to separation or the absence of a sealing washer on the valve
Install new sealing washer
- The unbalance valve of the carburetor float chamber does not work
Check the operation of the valve and fix the problem
- - Coolant entering the cylinders:
- - damaged cylinder head gasket;
Replace gasket
- crack or sink in the cylinder head;
Replace cylinder head
- the tightening of the nuts of the studs for fastening the head of the block has loosened
Replace cylinder head gasket, check head flatness
- Malfunctions of the ignition system
Check ignition system See "Ignition system"
Engine idling erratically
- Incorrect hour adjustment idle crankshaft speed
Adjust low crankshaft speed
- Air leakage through the intake manifold gasket
Replace gasket. Check the condition of the ends of the nozzles and in case of non-flatness exceeding 0.2 mm, replace the pipeline
- The location of the high voltage wires on the distributor cap does not correspond to the order of operation of the cylinders
Connect wires correctly
- Malfunctions of the ignition system
Check ignition system See "Ignition system"
Engine stalls when throttle is suddenly opened
- The accelerator pump does not work (diaphragm damaged, pump drive malfunction, non-return valve leakage)
Troubleshoot the accelerator pump or check valve, replace the pump
- The injection valve of the accelerator pump has turned out
Close the discharge valve
- The accelerator pump nozzle is clogged
Clean and blow out the sprayer with compressed air
- Jamming of the injection valve of the accelerator pump in its seat due to wear of its conical part
Replace valve
The engine does not develop full power
- The engine is not warmed up
Warm up the engine
- Incomplete throttle opening when the accelerator pedal is pressed all the way
Adjust throttle actuator
- Air filter dirty
Rinse filter element
- - Compression reduction in cylinders:
- - Loose fitting of valves to seats
Lap the valves to the seats, adjust the thermal gaps in the actuator
- Burning exhaust valves
Replace valves and lap them into seats
- Severe wear, breakage or burning of piston rings
Replace the piston rings, pre-clean the grooves in the pistons
- Wear of cylinder liners and pistons to limit values (maximum clearance between the piston and the sleeve is more than 0.30 mm)
Replace sleeves (block) and pistons with rings
- Damaged cylinder head gasket
Replace gasket
- Poor combustible mixture
Rinse and blow out the carburetor metering systems with compressed air, adjust the fuel level in the float chamber
- Early or late ignition
Adjust ignition timing
- Silencer or exhaust pipe clogged with soot
Replace muffler, clean exhaust pipe
Engine is overheating
- Insufficient amount of coolant in the cooling system
Add liquid. Check for leaks in the cooling system
- The blinds are not fully open when the handle of their drive is fully recessed
Adjust blind drive
- Fan belt slips
Tighten the fan belt
- The upper thermostat valve does not open
Replace thermostat
- Scale deposits on the internal surfaces of the cooling system
Rinse the cooling system with special descalers
- Contamination of the inside of the radiator or clogging of the gaps between the cooling plates of the core
Remove the radiator from the car, wash it from the inside and outside with a jet of water under pressure
- Large friction losses in the chassis of the car
Check the free rolling path of the vehicle and adjust the brakes, toe and wheel bearings if necessary
- Ignition too late
Check and adjust ignition timing
- Faulty viscous fan
Replace viscous coupling
- The oil cooler is not turned on when driving in hot weather or difficult road conditions
Enable Heatsink
The engine slowly warms up to operating temperature
- The blinds are not completely closed when the drive handle is pulled out to the end
Adjust blind drive
- The upper thermostat valve is constantly in the open position
Replace thermostat
Increased fuel consumption
- Increased fuel level in the carburetor float chamber
Adjust fuel level
- The air jets of the main dosing system of the carburetor are clogged
Clean, wash in gasoline and blow out the air jets with compressed air
- The float chamber of the carburetor is constantly in communication with the atmosphere due to a malfunction of the unbalance valve
Troubleshoot the imbalance valve
- The carburetor choke sticks in the closed position
Adjust damper actuator
- Air filter dirty
Rinse filter element
- Fuel leak in fuel line connections or through a damaged fuel pump diaphragm
Tighten fuel line connections or replace diaphragm
- Large power losses due to friction in the chassis of the car
Check Check the free rolling path of the vehicle and adjust the brakes, toe and wheel bearings if necessary
Oil pressure reduction
- Faulty sensor or pointer
Check the oil pressure with a control pressure gauge and replace the gauges if necessary
- Low oil level in the crankcase, which affects the pressure when the car is moving up or down
Check the level and add oil if necessary
- The gasket in the oil pump or under the pressure pipe flanges is damaged
Replace damaged gaskets
- Entry of foreign particles under the pressure reducing valve in the oil pump
Disassemble and clean the oil pump
- Breakage of the pressure reducing valve spring or loss of its elasticity
Replace the spring or place 1-2 washers, 1 mm each, under it
- Wear of oil pump parts
Replace pump assembly
- Fuel entering the crankcase through a damaged fuel pump diaphragm
Change oil, repair fuel pump
- Decrease in oil viscosity due to overheating
Do not overheat the engine, turn on the oil cooler in time
- Clogging of the oil intake screen of the oil pump
Rinse the oil pickup screen
- The increase in clearances in the crankshaft bearings is higher than the maximum allowable due to wear of the liners
Replace crankshaft bearing shells
Increased oil consumption
- - Oil carryover with crankcase gases:
- - Leakage in the seal of the oil level indicator (oil dipstick)
Replace the probe seal
- Oil filler cap seal leakage
Replace cover seal
- Increased breakthrough of gases into the crankcase due to wear, breakage or burning of piston rings, as well as wear of cylinder liners and pistons
Repair the cylinder-piston group
- Clogged air filter element
Rinse filter element
- Oil ingress into the intake channels through the gaps of the valve stems due to wear and aging of the material of the valve stem seals
Replace oil seals
- Oil leakage through seals and seals
Replace seals, tighten connections, replace gaskets
Extraneous knocks in the engine (if the ignition is set correctly and the recommended fuel is used)
- - Large gaps between rocker arms and valve stems:
- - Adjustment of thermal gaps is violated
Adjust thermal gaps
- Excessive wear of rocker heads and valve stem ends
Replace worn parts, adjust gaps
- "Drowning" of crackers with a valve in the sleeve of the spring plate
Replace damaged parts
- Destruction of bearing shells
Replace Earbuds
- Scuffing on the surface of the piston skirt
Replace piston and cylinder liner (or adjust cylinder block)
- Excessive wear on the ends of the pushers or camshaft lobes
Replace tappets or camshaft
- The gaps between the cylinders and pistons have been increased above the permissible limit (the knock is heard only on a cold engine)
Repair the cylinder-piston group
- Increased axial play of the camshaft due to wear of the end face of the gear hub on the side of the thrust flange
Replace the camshaft gear
- Increased axial play of the crankshaft due to wear of the thrust rings
Replace front thrust bearing washers and press in new pins
Engine won't start or runs intermittently
- Ignition timing incorrectly set
Set ignition timing
- Breakdown of the high-voltage wire from the ignition coil to the distribution sensor
Replace wire
- Large gap in spark plugs
Adjust Gap
- - Breakdown of the cover of the sensor-distributor
- - There is no spark discharge on the candles when starting the engine:
- Failure of the ignition coil or additional resistance
Replace cover
- There is no contact in the outputs of the distribution sensor
Replace coil or additional resistance
Restore contact
- Breakage of the stator winding of the sensor-distributor
Switch to emergency mode. Replace stator