Two types of front axles are installed on cars - with a single final drive or with additional wheel reduction gears
Axle with a single final drive consists of a cast-iron crankcase split in a vertical plane and steel tubular casings of the axle shafts pressed into it, additionally fixed by welding
Crankcase halves are bolted together through a gasket
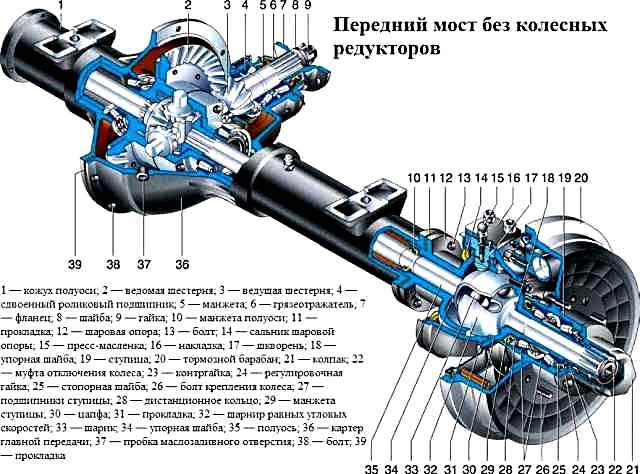
Front axle without wheel reduction gears: 1 - axle housing; 2 - driven gear; 3 - drive gear; 4 - double roller bearing; 5 - cuff; 6 - mud deflector; 7 - flange; 8 - washer; 9 - nut; 10 - half shaft cuff; 11 - gasket; 12 - ball bearing; 13 - bolt; 14 - ball bearing seal; 15 - grease fitting; 16 - overlay; 17 - kingpin; 18 - thrust washer; 19 - hub; 20 - brake drum; 21 - cap; 22 - wheel off clutch; 23 - locknut; 24 - adjusting nut; 25 - lock washer; 26 - wheel bolt; 27 - hub bearings; 28 - remote ring; 29 - hub cuff; 30 - trunnion; 31 - gasket; 32 - hinge of equal angular velocities; 33 - ball; 34 - thrust washer; 35 - axle shaft; 36 - main gear housing; 37 - oil filler plug; 38 - bolt; 39 - gasket
The main gear with differential is located in the left half of the crankcase and forms the axle gearbox
The drive gear of the final drive is installed in the crankcase on roller radial-contact double and roller radial bearings located on both sides of its ring gear
The driven gear is bolted to the pinion box
Gears - bevel with spiral tooth, gear ratio - 4.625
The satellite box consists of two halves connected by bolts. It is installed in the crankcase on two tapered roller bearings.
The box contains two pinion axles, four pinion gears and two side gears with thrust washers
Adjustment of the bearings and engagement of the final drive gears is done by changing the thickness of the spacers between the inner rings of the pinion bearing and the number of washers at the inner rings of the satellite box bearings
For an axle without wheel reduction gears, a ball joint with two holes, into which bronze bushings are pressed, is bolted to the flange of each of the axle shaft covers
The bushings include two pins pressed into the steering knuckle
A hollow trunnion is bolted to it, on which two identical tapered roller wheel bearings are mounted.
Five bolts are pressed into the hub, to which a stamped steel wheel with a bore diameter of 15 or 16 inches is fastened with flare nuts
The hub bearings are adjusted by nuts mounted on the threaded end of the trunnion
Each semi-axis consists of a driving and driven parts connected by a Weiss ball joint of equal angular velocities
The hinge is located inside the ball joint and consists of two profiled fists, interlocking with each other by means of four balls placed in their grooves
The fifth (central) ball is located in the center of the hinge on the same axis as the pivots
The driven part of the axle shaft passes inside the trunnion and is connected to the drive flange of the hub through the splined wheel disconnect coupling
The flange is fastened with studs through the gasket to the end of the hub
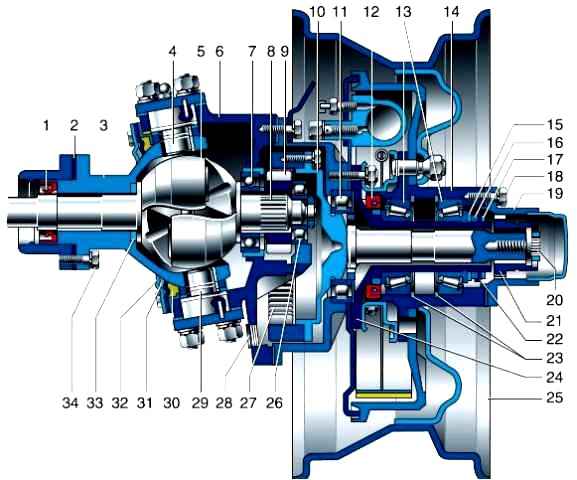
Knuckle with wheel gear: 1 - cuff; 2 - gasket; 3 - ball bearing; 4 - upper kingpin; 5 - hinge of equal angular velocities; 6 - rotary fist; 7 - ball bearing; 8 - hinge shaft; 9 - drive gear; 10 - driven shaft; 11 - roller bearing of the driven shaft; 12 - cuff; 13 - roller bearings of the hub; 14 - hub; 15 - lock washer; 16 - adjusting nut; 17 - locknut; 18 - bolt; 19 - leading flange; 20 - clutch bolt; 21 - clutch; 22 - lock washer; 23 - retaining rings; 24 - trunnion; 25 - wheel; 26 - roller bearing of the drive gear; 27 - driven gear; 28 - oil drain plug; 29 - lower kingpin; 30 - rubber cuff; 31 - felt ring; 32 - cover; 33 - thrust washer; 34 - flange bolt
The front axle with wheel reduction gears is different in that:
- - a gearbox with a spur internal gear and a gear ratio of 1.94 is attached to the steering knuckle body;
- - the final drive gear is cantilevered on two tapered roller bearings with a spacer sleeve between them;
- - gear ratio about the main gear is reduced to 2.77, and accordingly, the dimensions of the main gear housing are reduced
The drive gear of the gearbox is mounted on the splines of the driven part of the axle shaft
Thanks to the use of wheel gears, the vehicle's ground clearance is increased by 80 mm, which increases its cross-country ability
The main gear and wheel reduction gears are lubricated with gear oil poured into their crankcases
The final drive housing and wheel reduction gears have oil change holes closed with tapered thread plugs
Hub bearings, constant velocity joints and kingpins are lubricated with grease
To prevent leakage of oil and grease, as well as to protect against the penetration of dirt inside, the front axle is equipped with gaskets between fixed parts, cuffs in the hubs and on the pinion shaft, as well as combined felt-rubber oil seals sliding on the spherical surface of the ball bearings
In order to prevent oil from the gearboxes from penetrating into the cavity of the ball bearings, cuffs are installed on the axle shafts, and the ball bearing of the wheel gearbox has an oil deflector
Relubrication of the front axle
It is advisable to change the lubricant after a trip while the oil is warm
We install the car on a viewing ditch or lift
Cleaning the filler and drain plugs of the reducer
We substitute a container to drain the oil from the gearbox
Unscrew the gearbox drain plug with a 12 hexagon and drain the oil into a container
We clean the cork from metal particles and twist it into place
Unscrew the filler plug with a 12 hexagon
Pour fresh gear oil into the gearbox with an oil syringe to the level of the lower edge of the filler hole
We wrap the cork in place and tighten it.
If the used oil is dark in color and metal particles are visible in it, before filling in fresh oil, we flush the gearbox, for which, after draining the old oil, pour into the gearbox about 0.5 liters of a mixture of gear or engine oil with 20–30% kerosene or diesel fuel
Having wrapped the cork, we hang out one side of the car (until the wheels are off the ground) and turn on the front axle
Start the engine and turn on the first gear for 2–3 minutes, after which we completely drain the flushing oil and fill the gearbox with fresh gear oil, up to the lower edge of the filler hole
Similarly, we change the oil in the wheel gears
To lubricate the pivot joint, we clean the grease nipples of the pivots
Unscrew the 12 grease fitting with a wrench
Using keys 12 and 8, unscrew the grease fitting valve
We wash the removed parts in kerosene, blow with compressed air
Checking the mobility of the valve ball and assembling the grease fitting
Replace a defective valve
Install the grease fitting in place
We inject Litol-24 grease with a syringe through the grease fitting of the upper kingpin
Lubrication of the lower kingpin is not required, as it gets there by spreading during the rotation of the constant velocity joint
Similarly, we lubricate the upper kingpin of the other steering knuckle
Possible malfunctions of drive axles and methods of elimination
Increased driving noise
Increased lateral clearance in the main gear engagement due to:
- Wear of the gear teeth of the final drive
Replace worn gears
It is not necessary to adjust the position of the gears to compensate for wear, since the required contact in the meshing of the gears is achieved only at a certain relative position
- Wear of the bearings of the final drive gear
Adjust or replace worn bearings
- Differential bearing wear
Replace worn bearings
- Loosening the bolts of the driven gear to the differential
Tighten the driven gear bolts
- Incorrect adjustment of the main gear engagement on the contact
Adjust the gearing in the absence of tooth wear (for UAZ-3151 drive axles)
- Damage to differential parts (wear of gear teeth, rubbing surfaces of the satellite box and other parts associated with them). In this case, noise appears when turning or slipping one of the wheels
Replace worn parts
- Reduced oil level in the final drive housing
Add oil to the crankcase up to the lower edge of the oil filler hole
Oil leak through the cuff of the final drive gear
- Wear of the cuff or the surface of the flange of the driveshaft to the final drive gear
Replace the collar together with the flange