The air conditioning compressor is used to circulate the refrigerant in the system
The compressor shaft is installed in the aluminum front housing cover on bearings and sealed on the side of the drive pulley with an oil seal.
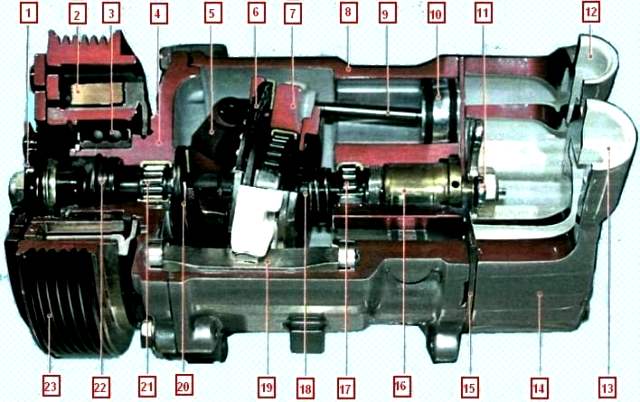
The compressor drive pulley is mounted on a double-row ball bearing and constantly rotates when the engine is running.
When the air conditioner is turned on, the torque is transmitted from the pulley to the compressor shaft through a friction clutch with an electromagnetic drive.
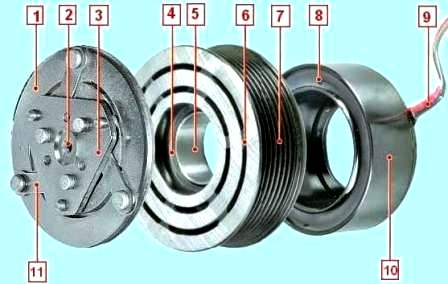
If the system is working, when the air conditioner is turned on, a click is heard - this is the clutch pressure plate, under the action of an electromagnet, engages with the drive pulley, and the compressor rotor starts to rotate.
But during the operation of the air conditioner, the following compressor malfunctions may occur.
If, when the air conditioner is off, the clutch makes extraneous sounds during rotation, heats up or smells of burning, then its bearing has probably begun to collapse.
In this case, the bearing must be replaced.
In some advanced cases, it may be necessary to replace the compressor clutch assembly or its components.
If you don't hear a click after turning on the air conditioner, then the following problems may occur:
- - a refrigerant leak has occurred and the control system is blocking the compressor from turning on;
- - the pressure sensor in the system has failed;
- - malfunctions in the electrical circuits of the control system;
- - the winding of the coil of the clutch electromagnet burned out;
- - the engine control unit for some reason (high engine coolant temperature, high engine speed) has blocked the compressor from turning on.
If the clutch rotates easily and freely, but when the air conditioner is turned on, extraneous noises are clearly audible or the engine even stalls, then the compressor is most likely stuck.
The internal pump part of the compressor cannot be repaired.
In this case, the compressor will have to be replaced.
If a click is heard, the clutch easily rotates the compressor shaft, and there is no coolness in the cabin.
In this case, it only seems that the compressor is working, but in reality it is not pumping anything.
Only an experienced specialist with special control and diagnostic equipment can establish the truth.
The cause of the malfunction can be most accurately determined after a complete diagnosis at a specialized service center for the repair of automotive air conditioners.
Removing the air conditioning compressor
Preparing the vehicle for work
We discharge the air conditioning system, as described in the article - Removing and installing the Renault Duster heater
Disconnect the negative battery terminal
We remove the front bumper (article - Removing and installing Renault Duster bumpers)
We remove the auxiliary drive belt (article - Checking and replacing the Renault Duster auxiliary drive belt)
We remove the lower radiator deflector and unscrew the two bolts securing the power steering radiator to the front suspension subframe (article - Removing the Renault Duster car subframe)
We take out the bushings of the upper supports of the fan casing from the holes of the upper cross member of the radiator frame.
Having raised the radiator, we remove the lower supports of the fan casing from the holes in the subframe and, having moved the radiator forward along the vehicle, we place the lower supports of the fan casing on the subframe.
Push the lock of the block and disconnect the block of wires from the block of wires of the compressor clutch.
With a 10 head, we unscrew the three bolts securing the compressor and place the compressor on the stretcher.
With a head of 10, unscrew the bolt securing the tube flange
Disconnect the low pressure pipe from the compressor
Remove the O-ring from the tube
In the same way, we disconnect the high pressure pipe from the compressor.
Remove the sealing ring
Remove the compressor from the engine compartment
Install the compressor in reverse order.
We tighten the compressor mounting bolts with a torque of 21 Nm.
When buying a new compressor, you need to clarify how much oil is poured into the compressor in order to fill in the required amount when refueling the air conditioner.
Replacing the compressor drive pulley bearing
The compressor pulley is mounted on a double-row ball bearing.
When pressing out, the bearing is destroyed, so we only press it out for replacement.
We bleed the refrigerant from the air conditioning system and remove the compressor as described above.
Holding the compressor rotor from turning with a special tool
Adjustment for fixing the compressor rotor
Unscrew the clamping plate nut
using a puller, we press the pressure plate from the compressor shaft
If the pressure plate is tight and rusted to the splines of the shaft, do not try to remove it by inserting a screwdriver into the gap between the pulley and the plate.
This will deform the plate.
To remove the pressure plate, use a special puller
We screw the bolts of the puller into the threaded holes of the pressure plate and turn the stop screw of the puller
Compressing the plate
Some plates do not have threaded holes. Then you need to cut the M6 thread
Inspecting the working surfaces of the pulley
We inspect the working surfaces of the plate for the absence of deep scratches, scuff marks and signs of wear and overheating.
If necessary, replace parts
We examine the rivet connections "A" and "B", as well as the elastic steel leashes "C" of the plate.
If the drivers are broken or the rivet connections are loose, replace the pressure plate.
Inspecting the slots of the pressure plate.
When the splines are worn, we replace the plate.
Inspecting the surface of the shaft seal
If there are signs of oil leakage through the shaft seal, the compressor must be replaced.
In some cases, if a leak is detected, the gland can be replaced.
But you need to know that the leak is caused by shaft play due to wear of the bearings or wear of the shaft in the seal area.
It is better to replace the compressor immediately.
Using an expanding puller, remove the pulley bearing circlip
Installing the puller
We press the pulley from the landing neck of the front cover of the compressor.
It is convenient to use a three-fingered puller
After removing the pulley, inspect the splines 3 and the threaded tip 2 of the shaft, the groove 4 for the retaining ring and the seating surface 1 of the bearing neck (for clarity, the magnet coil is removed).
When they are worn or damaged, we replace the compressor.
On a lathe, we cut off the rolling to fix the bearing in the pulley
Using a mandrel of a suitable diameter, we press the old bearing off the pulley.
After removal, the bearing is no longer suitable, we replace it.
We press in a new bearing.
Be careful when pressing.
The outer race wall of the pulley bearing is very thin.
Slight misalignment during press fitting can lead to bearing failure.
After pressing, we fix the bearing by punching the edge of the pulley mounting hole
We press the pulley onto the front cover of the compressor.
When pressing on, you need to apply force to the inner ring of the bearing.
Installing the retaining ring
After pressing on the compressor, we check the condition of the pulley. It should rotate silently, without jamming, evenly.
There should be no axial or radial runout.
If the check reveals axial or radial runout, the pulley is replaced.
Press the pressure plate onto the shaft
Screw on the old fastening nut
The pressure plate can only be installed on the shaft in one position.
When installing, we combine the protrusion "A" on the inner splined surface of the plate and the depression on the outer splined surface of the shaft.
Installing the compressor in a vise
Installing the arrow indicator.
Connect the positive battery terminal to the coil winding connector, negative terminal to the compressor housing.
Measure the gap "A" between the friction surfaces at different points.
If the gap is not the same, replace the pressure plate.
The nominal gap is (0.35±0.02) mm.
If the gap differs from the nominal size, remove the pressure plate.
To adjust the gap, we use special calibration washers.
After adjustment, unscrew the old bolt from the shaft end and screw in the new bolt.
We install the compressor and all the removed parts. Filling the air conditioning system.
Compressor clutch solenoid replacement
To work, you will need tools: a set of screwdrivers, an 18 wrench, pullers to remove the pulley, a puller to remove the electromagnet and a tester
Remove the refrigerant from the system.
Remove the compressor.
Remove the pressure plate
Remove the drive pulley as above
Remove the retaining ring of the compressor clutch electromagnet
To remove the retaining ring, use a special expanding puller
We move the electromagnet from the landing belt of the front cover of the compressor and remove it
We check with an ohmmeter the resistance of the winding of the electromagnet coil and the absence of a short circuit to the case.
Resistance should be 3.6-3.8 ohms.
We install the electromagnet on the front cover of the compressor. You need to make sure that the retaining ring is fully inserted into the groove
When installing the coil on the compressor, the fixing protrusion "A" on the rear surface of the coil housing must fit into the recess "B" on the compressor cover.
We press the pulley onto the landing neck of the compressor front cover.
You need to apply force to the inner race of the bearing.
After pressing, check the rotation of the pulley.
Install the compressor and other parts in reverse order.
Fill the system with refrigerant.