The generator is designed to generate electricity while the engine is running
The car is equipped with a three-phase alternator with electromagnetic excitation, a diode rectifier unit and a built-in voltage regulator.
The generator is driven by a V-ribbed auxiliary drive belt from the crankshaft pulley.
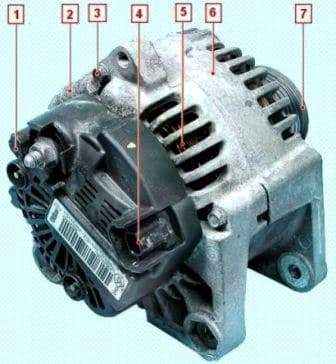
The generator consists of a rotor, a stator, a rectifier unit, a brush assembly with a voltage regulator and two covers.
A pulley is mounted on the rotor shaft.
For cooling the parts of the generator, ventilation holes are made in its covers, and an impeller is made on the rotor from the side of the front cover.
The stator has a three-phase winding connected by a "star".
The winding leads are soldered to the rectifier unit.
The rectifier unit is installed under the generator casing together with the brush assembly and voltage regulator.
The rotor has an excitation winding, the leads of which are soldered to two slip rings.
The generator rotor shaft rotates on two ball bearings.
The front bearing is pressed into the front cover of the generator, and the rear bearing is pressed onto the rotor shaft and held on the rear cover of the generator.
Voltage regulator - non-contact, electronic, combined with a brush assembly in a common non-separable housing.
Brushes - carbon, spring-loaded.
The model of the generator that the vehicle is equipped with depends on the type of engine installed.
For the K4M engine, the generator model is Valeo TG11C063 8200667607 110A
For F4R 2.0 engine generator model - Valeo TG12C092 231007562R 140A
If the battery indicator light on the instrument panel lights up, do not rush to immediately remove the generator for repair or replacement.
First, make sure that the problem is caused by a failure of the generator itself, and not by the wires of its electrical circuit or by loosening the drive belt.
Generator troubleshooting
To perform the work, you will need a multimeter (in voltmeter mode with a measurement limit of 15-20 V) and a technical stethoscope.
It is convenient to do the work with an assistant.
We prepare the car for maintenance and repair.
Checking the condition of the accessory drive belt
Wear of the drive belt leads to its slipping along the pulley and does not allow the generator to develop the necessary power.
Indirectly, belt slippage can be determined by the dim glow of headlights at night and by the whistling sound in the front of the engine when you sharply press the gas pedal.
We start the engine and observe the battery charge indicator lamp on the instrument panel (it should light up when the ignition is turned on and go out after the engine starts).
If the battery warning light does not go out after starting the engine, check for +12V to the alternator excitation winding.
To do this, disconnect the wire block from terminal 4 (Figure 1) of the generator and measure the voltage on it with a multimeter in voltmeter mode.
If there is no voltage, it is necessary to check the power circuit, the protection and switching unit in accordance with the vehicle electrical circuit.
We warm up the engine to operating temperature (at least 80˚ C).
We turn on all the powerful consumers of the car's electricity: rear window heating, air conditioning electric fan, high beam headlights.
The assistant, pressing the gas pedal and controlling the operation of the engine using the tachometer, maintains the engine speed within 3000-3500 min -1.
In the absence of an assistant, you can connect the multimeter to the battery using two pieces of wire.
The length of the wires must be sufficient so that the device can be placed in the car.
Using a multimeter in voltmeter mode, we measure the voltage at the terminals of the battery.
With a working generator, the voltmeter should show a voltage of at least 14 V.
If the voltage is lower, the accessory drive belt may be worn, the alternator circuit may be faulty, the voltage regulator may be faulty, the brushes in the alternator may be oily or worn, or the alternator itself may be faulty.
A malfunction of the generator can be caused by poor electrical contact in the connections due to the formed oxides.
Disconnect the tip and the wire block from the generator (see below) and process them with an agent for cleaning and protecting electrical contacts.
Removing and installing the generator
Disconnect the negative battery terminal
Removing the front bumper
With a 10 head, unscrew the nut securing the air conditioner tube holders on the engine compartment mudguard
With a 10 head, unscrew the nut securing the air conditioner pipe holders on the mudguard cup
Remove the tube holders from the studs
We unscrew the two bolts of the power steering radiator
Remove the radiator deflector
Remove the retainer of the upper support of the electric fan casing
Pressing the bushing of the upper support of the fan shroud with your hand from below, use a screwdriver to press the four clamps of the bushing
Remove the sleeve from the hole in the upper cross member of the radiator frame.
We also take out the other bushing of the upper support of the fan casing.
Having lifted the fan, we remove the lower supports of the fan casing from the holes in the subframe and, having moved the radiator forward along the vehicle, we place the lower supports of the fan casing on the subframe.
Having disconnected the wiring block from the air conditioning compressor connector and unscrewed its fastening bolts, we take the compressor to the side and place it on the stretcher (the arrow shows the lower support of the fan casing).
With a 10 head, unscrew the lower generator mounting bolt
Remove the bolt
With a 13 head, unscrew the nut securing the wire tip
Remove the wire tip from the generator output
Using a screwdriver, we press the lock of the wire block
Disconnect the block from the generator connector
With a 10 head, unscrew the upper bolt of the generator
Remove the bolt
We press the generator with a mounting blade to take the threaded bushings of the generator away from the bracket
Remove the generator from the engine compartment
Having prying with a screwdriver, we shift the generator casing from three pins
Remove the casing (the arrows show the casing fastening studs)
Using a 7-head, we unscrew the stud and two bolts of the brush holder for the hexagon
Remove the brush holder with voltage regulator assembly
To check the voltage regulator, we connect a lamp (1-3 W, 12 V) to the brushes, and a DC source to the brush holder terminals, first with a voltage of 12 V, and then 15-16 V.
In the first case, the lamp should be on, in the second, it should not.
If the lamp is on in both cases - there is a breakdown in the regulator, if it is not on, there is an open or broken contact between the voltage regulator terminals and the brushes.
In both cases, the brush holder with voltage regulator must be replaced.
To check the breakage of the rotor winding, we connect the probes of a digital tester (in ohmmeter mode) to slip rings
If the tester shows infinity, then there is a break in the winding.
To check the short circuit of the rotor winding to ground, we connect the tester probes (in ohmmeter mode) to the contact ring and the generator case.
The tester should show infinity, otherwise the winding is shorted to ground.
In both cases, you need to replace the rotor or generator.
We examine the stator windings, there should be no signs of overheating on the winding insulation, which is the result of a short circuit in the rectifier unit valves.
If there are signs of overheating on the windings, the stator or generator must be replaced.
To check for an open in the stator windings, we connect the tester probes (in ohmmeter mode) to the winding terminals.
If the tester shows infinity, then there is a break in the winding and the stator or generator needs to be replaced.
We also check the rest of the stator windings.
To check the short circuit of the stator winding to ground, we connect the tester probes (in ohmmeter mode) to the winding output and the generator case.
The tester should show infinity, otherwise the winding is shorted to ground and the stator or generator needs to be replaced.
We also check the rest of the windings.
To check the diodes of the rectifier unit, plus a digital tester (in the diode test mode) we connect to the “B +” terminal of the generator, and the minus to its case.
The tester should show infinity.
Otherwise, there is a short circuit in both the positive and negative diodes.
To check the short circuit in positive diodes, we connect the plus of the tester (in the diode test mode) to the “B +” terminal of the generator, and the minus to the output of one of the stator phase windings.
The tester should show infinity.
If the tester shows a circuit, one or more positive diodes are broken.
To check the short circuit in negative diodes, we connect the tester plus (in the diode test mode) to the output of one of the stator phase windings, and the minus to the generator case.
The tester should show infinity.
If the tester shows a circuit, one or more negative valves are broken.
Before installing the brush holder, we sink the brushes and, by sliding the brush cover, fix the brushes.
We install the brush holder in place, twist and tighten the bolts and the pin of the brush holder.
By pressing the cover, we release the brushes, which, under the action of the springs, will move forward to the slip rings.
Replace the generator cover.
Before installing the generator, we shift the threaded bushings towards the generator casing by 2-4 mm.
To do this, resting the hammer on the eye of the generator, we twist the generator fastening bolt into the sleeve until it stops against the hammer and, turning the head by 10 bolts, shift the sleeve.
We also move another threaded bushing.
Install the generator in reverse order.
Generator repair
To repair the generator, you will need keys for 7, 10, 27, a TORX T50 key, a tester, a puller, a hammer, screwdrivers.
Retaining the shaft from turning, unscrew the pulley fastening nut.
Remove the pulley and spacer
We mark with a marker the relative position of the covers and the stator housing
Pry off the edge of the casing with a slotted screwdriver
Remove the cover
Remove the two screws securing the brush holder
Unscrew the brush holder nut
Remove the brush holder assembly with the voltage regulator
Checking the protrusion of the brushes.
If the dimension "A" is less than 5 mm, replace the brush assembly.
We also check the ease of movement of the brushes.
Checking the resistance of the rotor winding.
The tester readings should show infinity, otherwise there is a break in the rotor winding and the rotor is replaced
Unscrew the four tie bolts
Insert a screwdriver between the covers to separate them
Remove the cover from the drive side together with the rotor
We press the rotor out of the front bearing
To replace the front rotor bearing, unscrew the four screws securing the pressure plate
Remove the plate
Press the bearing out of the cover
We press the new bearing into the cover with a mandrel of a suitable size, applying force to the outer ring.
We press the bearing off the rotor shaft using a puller
We press the new bearing onto the rotor shaft until it stops, applying force to the inner ring of the bearing
We check the absence of a short circuit of the rotor winding to the body by connecting it in turn to each slip ring and to the rotor body.
The tester should show infinity.
Assemble the generator in reverse order.
We orient the covers according to the established marks.