GAZelle Next vehicles equipped with a manual transmission are equipped with a dry single-plate clutch with a central diaphragm pressure spring.
The clutch is located between the engine and the gearbox.
It is designed to disconnect and connect the flywheel located on the engine crankshaft and the input shaft of the gearbox.
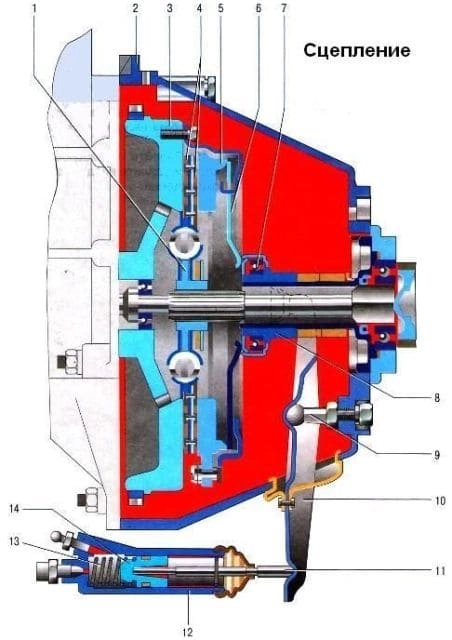
The clutch consists of a driven (friction) disk, a clutch housing with a pressure plate and a diaphragm spring, and a clutch release mechanism.
The pressure plate is mounted in a stamped steel casing bolted to the engine flywheel.
The driven disk is mounted on the splines of the gearbox input shaft and clamped by a diaphragm spring between the flywheel and the pressure plate.
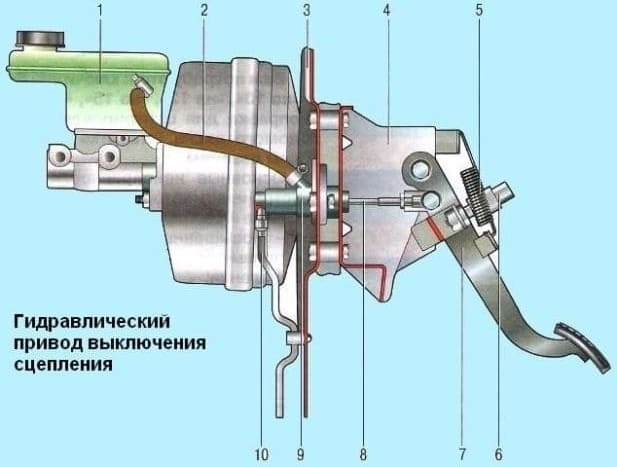
The clutch release hydraulic line consists of the master and slave cylinders, clutch pedal, clutch release hydraulic line and connecting hose.
The clutch pedal is connected to the master cylinder by means of a pusher, which is equipped with an adjustment unit.
The pedal is returned to its original position by a spring.
The sensor informs the electronic unit of the engine control system about the position of the clutch pedal at any given moment.
The master cylinder is connected by a hose to a reservoir installed on the master brake cylinder (the reservoir is common for both master cylinders).
The clutch release hydraulic line uses brake fluid.
Possible clutch malfunctions and troubleshooting methods
Cause of malfunction (Methods elimination)
- 1. Incomplete disengagement of the clutch (clutch drags):
- Difficulty in moving the driven disk hub on the splines of the gearbox input shaft - Clean the splines
- Warping of the driven disk - Replace the driven disk
- The petals of the diaphragm spring do not lie in the same plane or are worn - Replace the pressure plate
- Air in the hydraulic clutch drive system - Bleed the system
- 2. Incomplete clutch engagement (slippage, reduced acceleration dynamics):
- Reduced diaphragm spring force - Replace the pressure plate assembly
- Worn friction linings, flywheel and pressure plate working surfaces - Replace the driven disk. Replace the flywheel or pressure plate
- Oiling of the friction linings of the driven disk - Eliminate the causes of oil getting on the friction linings. Replace the driven disk
- Difficult movement of the driven disk hub on the splines of the gearbox input shaft - Clean the splines
- The diaphragm spring petals lie in the same plane or are worn - Replace the pressure plate
- Slow return of the slave cylinder piston to its original position when the clutch pedal is fully released; clogging of the compensation hole of the master cylinder or swelling of the cuff - Clean the cylinder from contamination or replace the cuff
- 3. Incomplete clutch engagement (noticeable jerks when engaging):
- Worn friction linings - Replace the driven disc
- Oiling of the friction linings of the driven disc - Eliminate the causes of oil getting on the friction linings. Replace the driven disc
- The petals of the diaphragm spring are not in the same plane or are worn out - Replace the pressure plate
- Loss of elasticity of the leaf springs and damper springs of the driven disc - Replace the driven disc
- 4. Increased noise and vibration during clutch operation:
- Breakage or loss of elasticity of the damper springs of the driven disc - Replace the driven disk
- Lack of lubrication or defects of the clutch release bearing (release bearing) - Replace the bearing or coupling with bearing
- Worn friction washer of the driven disk - Replace the driven disk
- 5. The pressure in the clutch release drive is not maintained (when smoothly pressed, the pedal reaches the stop, but the clutch does not disengage):
- The master cylinder is dirty or its surface is heavily worn - Flush or replace the master cylinder
- The master cylinder piston seal is worn or damaged - Replace the seal
- Fluid is leaking through the seal of the clutch release drive slave cylinder, the pipeline is not tight - Replace the seal or slave cylinder, tighten the pipeline fastening
- Air in the clutch release hydraulic drive - Bleed the drive, remove air
- 6. Increased noise in the clutch when the engine is running:
- Lack of lubrication or defects in the release bearing - Replace the bearing or coupling with the bearing
- Weak tightening of the hydraulic clutch release drive connections - Tighten the connections
- 7. Squeaking clutch pedal bushings:
- Lack of grease in the plastic clutch pedal bushings - Lubricate the bushings with graphite grease
- Worn plastic clutch pedal bushings - Replace the bushings
- Breakage or loss of elastic properties of the return spring - Replace the spring
Changing the fluid and bleeding the clutch
Since the clutch release hydraulic drive and the service brake system are combined in one reservoir, the working fluid in the clutch release hydraulic drive is replaced when the brake fluid in the brake hydraulic drive is changed.
According to the manufacturer's recommendation, the fluid should be replaced after thirty thousand kilometers or 2 years of operation (whichever comes first)
The clutch release hydraulic drive uses brake fluid DOT-4.
This fluid is hygroscopic (quickly absorbs moisture from the air).
The condensate formed in the master and slave cylinders causes corrosion of parts and failure of the hydraulic drive, so we recommend replacing the fluid regardless of the mileage.
Remove the protective cap from the air bleed valve on the clutch slave cylinder.
Put a hose on the valve and lower its end into a container with a small amount of brake fluid. fluid.
Ask your assistant to press the clutch pedal sharply four to five times at intervals of one to two seconds, and then hold it down.
Unscrew the valve by ¾ of a turn.
Old (dirty) fluid will flow out of the hose into the container.
As soon as the fluid stops flowing, tighten the air release valve.
Constantly monitor the fluid level in the tank, not allowing it to drop to the "MIN" mark on the tank wall, since at a lower level you may not notice the moment when the clutch release hydraulic drive section in the tank is completely dry and air will enter the system.
In this case, the hydraulic drive will have to be bled. If necessary, add new brake fluid.
This ensures that the old fluid is gradually replaced with the new one without draining the hydraulic system.
Repeat the operation until the fluid is completely replaced (clean fluid without air bubbles should flow out of the hose).
After replacing the fluid, put the protective cap on the release valve.
Add brake fluid to a level of 15-20 mm from the upper edge of the reservoir. Close the reservoir with a plug.