In the article, we will consider how to disassemble the cylinder head, grind the valves and assemble the head
Preparing the car for the task
Remove the cylinder head as described in the article "How to replace Mazda 6 cylinder head and cover gasket"
Remove the intake manifold, as indicated in the previous article
Remove the exhaust manifold
Unscrew the spark plugs
Cleaning the combustion chambers from soot
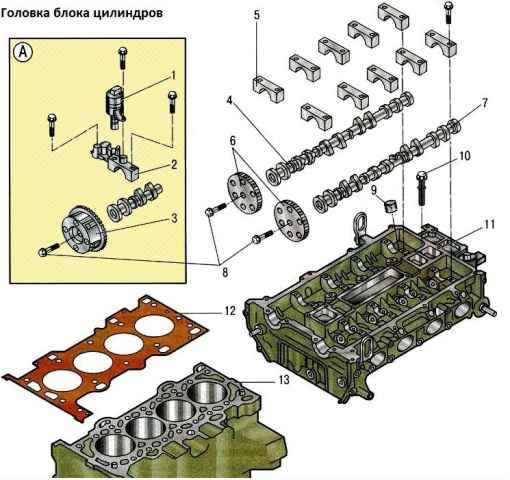
Inspecting the head of the block
If the cylinder head has cracks or traces of burnout in the combustion chambers, replace the head
Removing burrs and nicks on the surface of the block head
Checking the flatness of the surface adjacent to the cylinder block
We put a metal ruler with an edge on the surface of the head, first in the middle along, and then diagonally and measure the gap between the surface of the head and the ruler with a probe
The head must be replaced if the gap exceeds 0.025 mm
Remove the camshafts
Pushers are more convenient to remove with a magnet or suction cup
Pushers cannot be interchanged, so we mark them
Store the tappets in the position in which they are installed on the cylinder head so that oil does not leak out of them
We clean the surfaces of the flanges of the head for installing manifolds from the remnants of gaskets and carbon deposits
Check for deformations for the intake and exhaust manifolds, replace the deformed head
We repair damaged threaded holes by threading with taps or installing a repair sleeve
Check the tightness of the cooling jacket plugs. When their fit is weakened, we restore it by chasing
To check the tightness of the block head, plug the hole in the head under the thermostat socket.
This can be done, for example, by installing a blank gasket made of thick cardboard under the thermostat housing and tightening the bolts of its fastening.
Pour kerosene into the channels of the water jacket.
If the level of kerosene decreases after 15-20 minutes, it means that there are cracks in the head and it must be replaced.
After checking, do not forget to remove the cardboard spacer.
Check the condition of the bearing surfaces under the camshaft journals in the head of the block.
If at least one of them shows signs of wear, scuffing or deep risks, grind the bearing beds and measure the gap between the beds and the camshaft journals after grinding.
If the gap is greater than the nominal, replace the block head.
To check the tightness of the valves, pour kerosene into the inlet and outlet channels of the head.
If within 3 minutes kerosene does not seep from the channels into the combustion chambers, then the valves are tight. Otherwise, lap or replace the valves.
Place a suitable stop under the valve to be removed (for example, a socket from the tool kit)
We install a device for compressing valve springs on the head of the block
Compress the valve springs with the tool and remove the valve cotters
Then, gradually loosening the pressure on the device handle, we completely release the valve spring
Remove the fixture from the head of the block
Prying with a screwdriver, take out the valve spring plate and take out the spring
Remove the valve from the block head
In the same way, we take out the remaining valves and remove the valve stem seals
Removing carbon from the valves and inspecting them
Deformation of the valve stem and cracks on its plate are not allowed. If there is damage, replace the valve
Check if the working bevel is too worn or damaged
Grinding of the working chamfer of valves is allowed
Minor scratches and scratches on the chamfer can be removed by lapping the valve against the seat
Do not clean the valve stems with wire brushes and scrapers, so that there are no marks on the stems
Check the concentricity of the valve disc and the seat: apply a thin layer of graphite (pencil lead) to the chamfer of the valve head, insert the valve into the guide sleeve and, slightly pressing against the seat, turn
Traces of graphite on the chamfer of the seat indicate the concentricity of the valve and seat
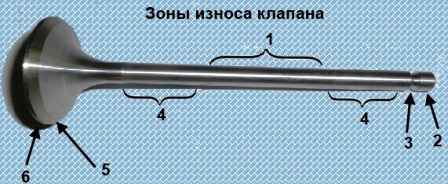
Check the wear of the valve stem in the places shown in the figure
Nominal valve sizes:
- Diameter of inlet valve head 35.95 mm;
- Exhaust valve head diameter 31.45 mm;
- Inlet valve stem diameter 6.980 mm;
- Exhaust valve stem diameter 6.956mm;
- Intake and exhaust valve height 89.95mm;
- The angle of the working chamfer of the intake and exhaust valves is 45º.
Check the condition of the grooves 3 of the valve stem for crackers.
If traces of chipping of the edges of the grooves and wear of the cylindrical part are found, replace the valve
Check the condition of the valve guides by measuring the inner diameter of the hole. The gap should not exceed 0.1 mm
Check the condition of the valve seats. The seat bevels must be free of wear, pitting, corrosion, etc.
Valve seats can be replaced at a specialist workshop.
Minor damage (small marks, scratches, etc.) can be removed by lapping the valves
More significant defects in valve seats are eliminated by grinding, maintaining for engine valve seats, dimensions 45 ° with a belt width after grinding for all valve seats 1.56 mm
It is recommended that saddles be ground in a specialized workshop, as this requires special tools and equipment.
If grinding fails, replace the valve seats.
Replace the valve stem seals regardless of their condition.
Inspect the valve springs. Cracks and reduction of elasticity of springs are not allowed.
If possible, determine the elasticity of the springs by the force developed.
Replace warped springs (deformation in the free state more than 1.6 mm) and springs with cracks.
Always replace the gaskets of the intake pipe, exhaust manifold and cylinder head with new ones, since the gaskets removed, even outwardly not damaged, may be heavily compressed and will not ensure tightness of the seals