The compressor is mounted on the engine block and is driven by a ribbed belt
The compressor circulates the refrigerant in the system.
The compressor shaft is mounted in an aluminum front housing cover on bearings and sealed on the side of the drive pulley with an oil seal
Compressor drive pulley 2 is mounted on a double-row ball bearing and constantly rotates when the engine is running.
When the air conditioner is turned on, torque is transmitted from the pulley to the compressor rotor through a friction clutch with an electromagnetic drive.
If the system is in good order, when the air conditioner is turned on, a click is heard - this is the clutch pressure disk 1, under the action of an electromagnet, engages with the drive pulley 2, and the compressor rotor starts to rotate.
But during the operation of the air conditioner, the following compressor malfunctions may occur.
If, when the air conditioner is off, the clutch makes extraneous sounds during rotation, heats up or smells of burning, then its bearing has probably begun to collapse
In this case, the bearing must be replaced.
In some advanced cases, it may be necessary to replace the compressor clutch assembly or its components.
If you don't hear a click after turning on the air conditioner, then the following problems may occur:
- – a refrigerant leak has occurred and the control system is blocking the compressor from turning on;
- – the pressure sensor in the system has failed;
- - malfunctions in the electrical circuits of the control system;
- - the coil winding of the clutch electromagnet burned out;
- - the engine control unit for some reason (high engine coolant temperature, high engine speed) has blocked the compressor from turning on.
If the clutch rotates easily and freely, but when the air conditioner is turned on, extraneous noises are clearly audible or the engine even stalls, then the compressor is most likely stuck.
The internal pumping part of the compressor cannot be repaired. In this case, the compressor will have to be replaced.
And the last, most unpleasant option.
A click is heard, the clutch easily rotates the compressor shaft, and the air in the cabin is not cooled.
In this case, the compressor runs idle, pumping nothing.
Only an experienced specialist with special monitoring and diagnostic equipment can determine this malfunction.
The cause of the malfunction can be most accurately determined after a complete diagnosis at a specialized service center for the repair of automotive air conditioners.
Replacing the compressor drive pulley bearing
You will need a 10 wrench, a pulley puller, a snap ring puller
Remove the refrigerant from the air conditioning system
Disconnect the negative battery cable
Remove the compressor as described above
Unscrew the fastening bolt, keeping the pressure plate from turning
Removing the bolt
In the photo there is a special device for holding the compressor rotor
Remove the pressure plate from the splines of the compressor shaft
Inspecting the working surface of the pulley friction
We inspect the pressure plate so that there are no deep scratches, scratches, obvious signs of wear and overheating
We also inspect the slots of the pressure plate
Pay attention to the pressure plate damper
There should be no traces of rubber buckling, cracks, breaks on the rubber massif of the damper
Inspecting the surface of the shaft.
If there are signs of oil leakage through the shaft seal, the compressor must be replaced
If you replace the oil seal, then, as a rule, this is not for long, since the working surface of the shaft, or the bearing, has probably already worn out.
Remove the pulley bearing circlip with a puller
Installing the puller
And we press the pulley from the landing neck of the front cover of the compressor
It is convenient to use a three-legged puller to compress the pulley
After removing the pulley, you need to inspect the splines 1 and the threaded hole 2 of the shaft, the grooves 3 for the retaining rings and the seating surface 4 of the bearing neck.
If there is wear, then the compressor needs to be replaced
Cut off on a lathe the rolling of the bearing fixation
We press out the old bearing from the pulley with a mandrel of a suitable diameter
We press in a new bearing.
When pressing, you need to apply force to the outer ring of the bearing
We fix the bearing along the edges of the mounting hole with a core
We press the pulley onto the landing neck of the compressor front cover.
When pressing, you need to apply force to the inner ring of the bearing
Installing the retaining ring
We put a pressure plate on the shaft and screw in the fixing bolt
Installing the compressor in a vise
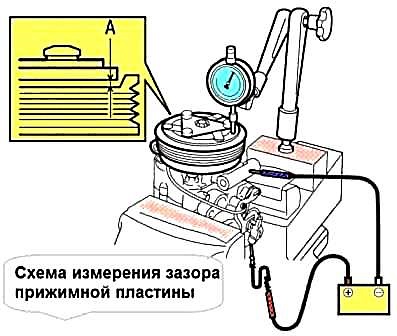
Install the arrow indicator as shown in the figure.
We connect the plus of the battery to the coil winding connector, and the minus of the battery to the compressor housing.
Measure the gap "A" between the friction surfaces of the pressure plate and the pulley.
If the gap is not the same at different points on the circle, then the pressure plate is deformed and needs to be replaced.
The nominal gap is 0.35-0.60 mm.
If the gap is different, remove the plate again.
With the help of shims mounted on the rotor shaft, we adjust the gap.
Then we put on the pressure plate and check the gap obtained.
For adjustment, you need to use special calibration washers
Compressor clutch solenoid replacement
Remove the compressor as described above
Remove the drive pulley
Remove the retaining ring of the compressor clutch electromagnet with a puller
We use such an expanding puller to remove the retaining ring
We unscrew the screw securing the holder of the electromagnet coil connector pad
We move the electromagnet from the landing belt of the front cover of the compressor and remove it
We check the resistance of the winding of the electromagnet coil and the absence of a short to the case with a tester in ohmmeter mode.
The resistance of the coil should be 3.6-3.8 ohms.
Install the electromagnet on the compressor cover and insert the retaining ring
When installing the coil on the compressor, the protrusion "A" on the rear surface of the coil housing must fit into the recess "B" on the compressor cover
After that, we collect all the details in reverse order.
Fill the air conditioning system with refrigerant.