En el artículo, consideraremos las operaciones para desmontar y reparar la culata del motor
Desmontaje de la culata
Lavamos la culata y la instalamos en un banco de trabajo o herramienta de desmontaje
Retiramos los levantaválvulas de la culata y marcamos su posición con respecto a la culata
Usando la herramienta comprimimos los resortes de las válvulas y retiramos las galletas con unas pinzas
Presionamos los sellos del vástago de la válvula con unos alicates especiales o un extractor inercial
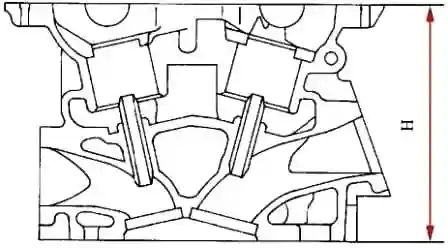
Comprobación de la altura de la culata
Altura H, (dibujo) las culatas deben ser de 125 mm
Usando una regla y un juego de palpadores, verificamos la planitud de la superficie de la culata que se acopla con el bloque de cilindros
Planitud máxima permitida de la superficie de contacto de la culata 0,1 mm
Revisar el diámetro de los soportes para los árboles de levas, para ello:
Instalamos casquillos de centrado, tapas de cojinetes de árbol de levas en la culata
Apriete los pernos de la tapa a 9,0-11,0 Nm (0,9-1,1 kgcm)
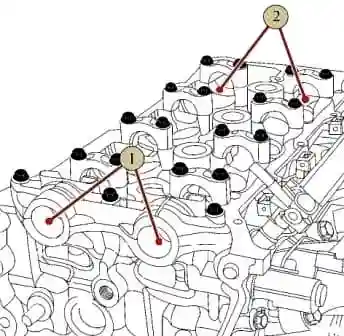
Medimos los agujeros de cada tapa con calibre NI 18-50-1
El diámetro de los agujeros para la primera tapa 1 (imagen) debe ser 28.000-28.021 mm, para los agujeros 2 de las tapas restantes 25.000-25.021 mm
Después de eso, desenrosque los pernos de montaje y retire las tapas de los cojinetes del árbol de levas y los casquillos de centrado
Comprobación del diámetro de los agujeros en las guías de válvula
El diámetro máximo permitido no debe exceder los 5,03 mm
Comprobación del diámetro de los nidos de empujadores en las culatas
El diámetro de los casquillos debe ser de 30.000-30.021 mm
Comprobación del diámetro exterior de los levantaválvulas
El diámetro de los taqués debe estar entre 29.977-29.987 mm
En la superficie de los empujadores no debe haber signos de desgaste y grietas en el recubrimiento
Comprobación de las válvulas
No se permite el desgaste unilateral del vástago de la válvula en la superficie de trabajo
Determinamos visualmente el desgaste y estado de los discos de válvula. No se permiten astillas, grietas ni desgaste unilateral.
Determinamos el desgaste del extremo del vástago de la válvula, si es necesario, puede rectificar el extremo
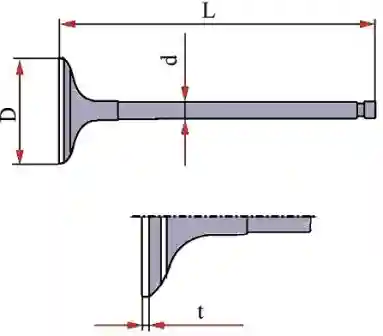
Dimensiones admisibles de válvulas según dibujo y según tabla
Tamaños de válvula permitidos
Válvula de entrada:
Diámetro del disco de la válvula D, mm 31,6±0,15
Diámetro del vástago de la válvula d, mm 4.965 - 4.980
Longitud de válvula L, mm 101,48
Altura de la parte cilíndrica del disco de válvula t, mm 1,00
Válvula de escape:
Diámetro del disco de la válvula D, mm 25,3±0,15
Diámetro del vástago de la válvula d, mm 4.955 - 4.970
Longitud de válvula L, mm 102,24
Altura de la parte cilíndrica del disco de válvula t, mm 1,00
Comprobación de los resortes de válvula
Longitud libre del resorte - 42,26 mm
Longitud del muelle bajo carga 145 ± 9 N (14,5 ± 0,9 kgf) - 34,4 mm
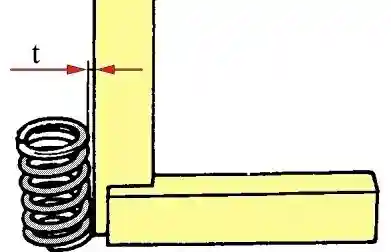
La desviación "t" (imagen), el resorte de la perpendicularidad no debe ser superior a 1,6 mm
Comprobación de asientos de válvulas y pulido de válvulas
Después de eso, lavamos y soplamos todos los agujeros y partes de la culata
Conseguir el gol Cilindros
Instale válvulas de admisión y escape en la culata
Para hacer esto, instale la culata en el accesorio 67.7823-9567 para romper y romper válvulas
Lubricar los vástagos de las válvulas con aceite de motor
Usando un mandril 67.7853-9732, presionamos los sellos del vástago de la válvula hasta el final en la superficie de apoyo de la culata
Instalación de las arandelas elásticas en la culata
Instalación de resortes de válvula y placas de resorte
Lubrica las superficies exteriores de los taqués con aceite de motor e instala los taqués en la culata de acuerdo con la marca
Usando una llave para espárragos, atornillamos nuevos espárragos de montaje del colector de escape en la culata, con una parte corta en el cuerpo de la culata
Retire la culata del accesorio
Instalación de la culata
Presionamos dos manguitos de centrado de la culata en el bloque de cilindros (si no están instalados).
Protrusión del manguito por encima del plano de contacto del bloque de cilindros 6-8 mm
Aplicamos dos puntos de sellador en la superficie del bloque motor lado distribución, como se muestra en la figura
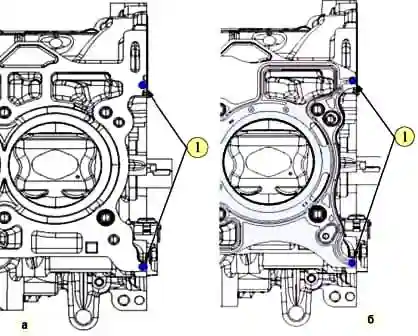
Instalamos una nueva junta de culata en el bloque de cilindros y aplicamos dos puntos de sellador en la junta lado distribución, como se muestra en la figura
Usamos sellador de silicona TB1217L, tasa de consumo - 1 gramo
Enroscamos el tornillo de la polea del cigüeñal en el cigüeñal e instalamos los pistones en la mitad de la carrera
Instalamos la culata, arandelas de los tornillos de la culata, nuevos tornillos de montaje en el bloque de cilindros.
Torcemos y apretamos los tornillos de la culata
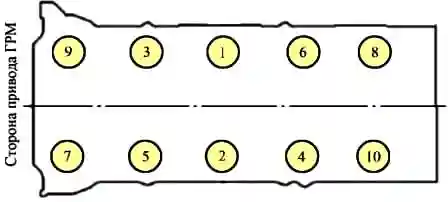
Apriete los tornillos de la culata en el orden que se muestra en la figura en la siguiente secuencia (cabeza reemplazable 11, perilla, extensión, llave dinamométrica, cabeza para medir el ángulo de rotación):
- - apriete los tornillos con un par de apriete de 35,0…44,0 Nm (3,5…4,4 kgf.m);
- - apretar los tornillos con un ángulo de 60º…65º.
- - desenroscar todos los tornillos;
- - apriete los tornillos con un par de apriete de 35,0…44,0 Nm (3,5…4,4 kgf.m);
- - apriete los tornillos con un ángulo de 75º…80º.