La extracción de la culata del motor se trató en el artículo - "Desmontaje de la culata"
Desmontaje de la culata en el artículo - "Desmontaje de la culata"
En este artículo, consideraremos revisar y reparar la culata.
Enjuagamos cuidadosamente la culata y limpiamos los canales de aceite de la culata.
Eliminamos los depósitos de carbonilla de las cámaras de combustión y de la superficie de los canales de escape con un cepillo metálico.
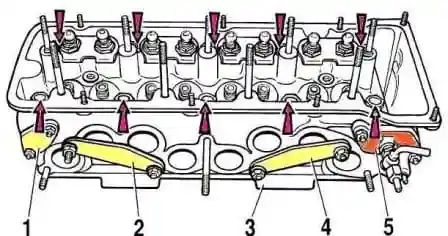
Inspección de la culata. No se permiten grietas en ninguna parte de la cabeza.
Si existe la sospecha de que ha entrado refrigerante en el sistema de aceite, debe comprobar la estanqueidad de la culata.
Para comprobar la estanqueidad, cierre los orificios de la camisa de refrigeración de la culata con tapones.
Existe un juego especial de tapones A.603334. Pero, por supuesto, puede hacerlo usted mismo con materiales auxiliares.
Inyecte agua a una presión de 0,5 MPa (5 kgf/cm2) en la camisa de refrigeración de la culata con una bomba.
No debe haber fugas de agua de la culata durante dos minutos.
Puedes comprobar la estanqueidad de la culata con aire comprimido, para lo cual también instalas los tapones de la herramienta A.60334 en la culata.
Sumergir la culata en un baño de agua calentada a 60-80˚C y dejar que se caliente durante cinco minutos.
A continuación, suministre aire comprimido en el interior del cabezal a una presión de 0,15-0,2 MPa (1,5-2 kgf/cm2). En 1-1,5 minutos, no deben salir burbujas de aire de la cabeza.
Asientos de válvula
La forma de los chaflanes de los asientos de las válvulas se muestra en las figuras 2 y 3.
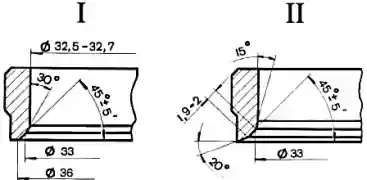
- 2. Perfil del asiento de la válvula de admisión
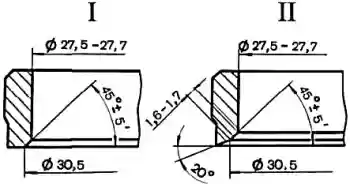
- 3. Perfil de asiento de escape
En los chaflanes de trabajo de los asientos (el área de contacto con las válvulas) no debe haber picaduras, corrosión ni daños.
Los daños menores se pueden reparar puliendo los asientos y eliminando la menor cantidad de metal posible.
El lijado se puede realizar a mano o con amoladora.
Para esmerilar los asientos, coloque la culata sobre un soporte, inserte la varilla A.94059 en la guía de la válvula y limpie los chaflanes de los asientos de los depósitos de carbón con A.94031 y A.94092 avellanadores para asientos de válvulas de escape y Avellanadores A.94003 y A.94101 para asientos de válvulas de admisión.
Las platinas se colocan en el husillo A.94058 y se centran con la varilla guía A.94059.
Estas varillas están disponibles en dos diámetros diferentes: A.94059/1 para guías de válvulas de admisión y A.94059/2 para guías de válvulas de escape.
Coloque el resorte A.94069/5 en la varilla guía A.94059, instale en el husillo A.94069 el círculo cónico A.94078 para asientos de válvulas de escape o el círculo A.94100 para asientos de válvulas de admisión, fije el husillo en un molinillo y muela la válvula de asiento.
- 4. Rectificado de asientos de válvulas
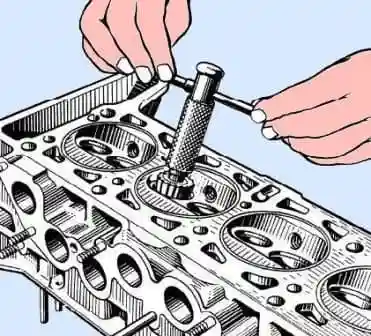
En el momento en que la rueda toca el asiento, la máquina debe estar apagada, de lo contrario se producirán vibraciones y el biselado será incorrecto.
Se recomienda revestir la rueda más a menudo con un diamante.
Para los asientos de las válvulas de escape, lleve el ancho del chaflán de trabajo a los valores indicados en la Figura 2, utilizando una avellanadora A.94031 (ángulo de 20˚), y una avellanadora A.94092, que elimina el trabajo de endurecimiento en el diámetro interior metro.
Las avellanadoras se colocan sobre el husillo A.94058 y, al igual que en el rectificado, se centran con la varilla A.94059.
En los asientos de las válvulas de entrada llevar el ancho del chaflán de trabajo a los valores indicados en la Figura 3, procesando primero el chaflán interior con avellanador A.94003 (Figura 5) hasta obtener un diámetro de 33 mm, y luego un chaflán de 20˚ con avellanado A.94101 hasta obtener un chaflán de trabajo de 1,9-2 mm de ancho.
Válvulas y guías de válvula
Eliminar la carbonilla de las válvulas.
Compruebe si el vástago está deformado o agrietado en el disco de la válvula. Reemplace la válvula dañada.
Compruebe el estado de la cara de la válvula. En caso de desperfectos menores, se puede lijar manteniendo un ángulo de chaflán de 45°30′±5′.
En este caso, las distancias desde el plano inferior del disco de la válvula hasta los diámetros de la base (36 y 30,5 mm) deben estar dentro de los límites indicados en la Figura 6
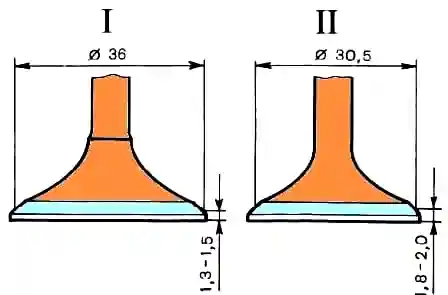
- 6. Límites dimensionales para rectificar chaflanes de válvulas
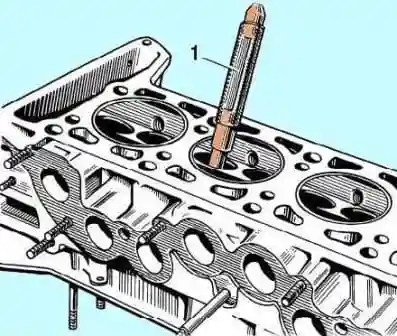
- 7. Extracción de casquillos guía
Compruebe la holgura entre las guías de la válvula y el vástago de la válvula midiendo tanto el diámetro del vástago de la válvula como el orificio del vástago de la válvula.
Espacio estimado para casquillos nuevos: 0,022-0,055 mm para válvulas de entrada y 0,029-0,062 mm para válvulas de escape; el espacio límite máximo permitido (durante el uso) es de 0,3 mm, siempre que no aumente el ruido del mecanismo de distribución de gas.
Si no se puede eliminar el aumento de la holgura entre el casquillo guía y la válvula reemplazando la válvula, reemplace los casquillos de la válvula utilizando el mandril A.60153/R para presionar hacia afuera y hacia adentro (Figura 7).
Presione los casquillos guía con el anillo de retención puesto hasta que haga tope contra el cuerpo de la culata.
Después de prensar, escariar los agujeros en los casquillos guía utilizando A.90310/1 (para casquillos de válvula de entrada) y A.90310/2 (para casquillos de válvula de escape).
Reemplace siempre las tapas deflectoras de aceite de los casquillos guía por otras nuevas cuando repare el motor.
Cambie los sellos de vástago de válvula dañados con la culata desmontada.
Para presionar las tapas, utilice el mandril 41.7853.4016.
Muelles
Asegúrese de que los resortes no estén agrietados y su elasticidad no haya disminuido, para lo cual verifique su deformación bajo carga (figura 8).
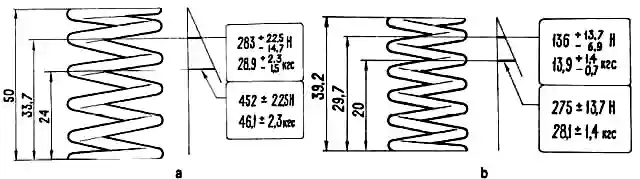
- 8. Datos básicos para comprobar el muelle de válvula exterior (a) e interior (b)
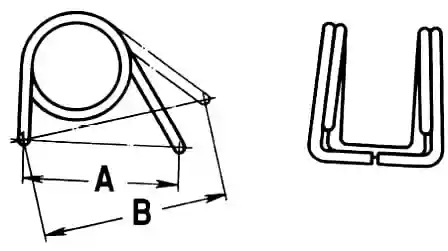
Para resortes de palanca (Figura 8), la dimensión A (resorte en estado libre) debe ser de 35 mm y la dimensión B bajo una carga de 51-73,5 N (5,2-7,5 kgf) - 43 mm.
Tornillos de culata
El uso repetido de pernos los alargará.
Por lo tanto, verifique que la longitud del eje del perno (excluyendo la longitud de la cabeza) no supere los 117 mm y, si es más larga, reemplace el perno por uno nuevo.
Palancas de válvula
Compruebe el estado de las superficies de trabajo de la palanca que se acopla con el vástago de la válvula, con la leva del árbol de levas y con el extremo esférico del perno de ajuste.
Si aparecen muescas o marcas en estas superficies, reemplace la palanca por una nueva.
Si se encuentra deformación u otro daño en el buje del perno de ajuste de la palanca o en el perno mismo, reemplace las piezas.