La unidad de control del motor Cummins ISF tiene un conector de dos piezas.
El bloque "A" está conectado al arnés de cableado del vehículo. Su composición puede variar mucho según la configuración del coche
A través de este bloque, entre otras cosas, la centralita recibe alimentación y se conecta a la masa del vehículo.
El bloque "B" combina el cableado del motor: sensores y actuadores.
Su composición elemental depende de los estándares de toxicidad que cumpla el motor en cuestión.
Sensor de posición del cigüeñal
El sensor de posición del cigüeñal está instalado en la zona de la polea del cigüeñal.
El principio de funcionamiento del sensor de posición del cigüeñal se basa en el efecto Hall.
El sensor determina la posición del cigüeñal y convierte estos datos en señales (pulsos rectangulares).
En base a estas señales, la unidad electrónica de control del motor determina la velocidad del cigüeñal del motor y corrige el momento en que se abre la tobera, así como la duración de su estado abierto y el ángulo de avance de la inyección de combustible.
El sensor tiene tres cables: alimentación, tierra y cable de señal.
La alimentación del sensor está estabilizada, es de aproximadamente 5 V y la proporciona la unidad de control del motor (terminal B13).
El contacto de tierra también está conectado a la unidad de control (terminal B14).
La señal del sensor se envía al terminal B38 de la unidad de control y es un pulso rectangular con un nivel bajo de aproximadamente 0 V y un nivel alto de aproximadamente 5 V.
Los principales fallos de funcionamiento del sensor se encuentran en tres áreas:
Fallo del propio sensor
Un mal funcionamiento de los sensores de efecto Hall se manifiesta principalmente después de que el motor se haya calentado: la electrónica integrada en el sensor falla debido al calentamiento.
Se producen intervalos de pulso.
Fallo de cableado
Se manifiesta en forma de ausencia total o parcial de una señal del sensor.
Se diagnostica comprobando la tensión en los contactos de los sensores con el contacto puesto y los conectores conectados. Y también la continuidad del cableado desde el sensor hasta la centralita con los conectores retirados.
Falla del rotor del sensor (rueda motriz)
Cabe señalar que la reparación de los dientes del rotor en caso de daño es inaceptable; el rotor debe ser reemplazado.
La soldadura cambia las propiedades magnéticas del material y es probable que la señal del sensor falle al pasar por el diente reparado.
La ausencia de movimiento de la aguja del tacómetro en caso de intentos fallidos de arrancar el motor puede servir como indicador de un posible mal funcionamiento del sensor de posición del cigüeñal.
Sensor de posición del árbol de levas
El sensor de posición del árbol de levas está ubicado en la culata y detecta el momento en que el pistón del cilindro n.° 1 llega al punto muerto superior en la carrera de compresión.
Basándose en la señal del sensor, la unidad de control electrónico del motor determina la secuencia de inyección de combustible para cilindros individuales.
El principio de funcionamiento del sensor de posición del árbol de levas se basa en el efecto Hall.
El sensor tiene tres cables: alimentación, tierra y cable de señal.
La alimentación del sensor está estabilizada, es de aproximadamente 5 V y la proporciona la unidad de control del motor (terminal B87).
El contacto de tierra también está conectado a la unidad de control (terminal B63).
La señal del sensor se envía al contacto B62 de la unidad de control y es un pulso rectangular con un nivel bajo de aproximadamente 0 V y un nivel alto de aproximadamente 5 V.
Los principales fallos de funcionamiento del sensor se encuentran en tres áreas:
1) Mal funcionamiento del propio sensor.
Un mal funcionamiento de los sensores de efecto Hall se manifiesta principalmente después de que el motor se haya calentado: la electrónica integrada en el sensor falla debido al calentamiento.
Se producen intervalos de pulso.
2) Cableado defectuoso, incluidos los conectores. Se manifiesta en forma de ausencia total o parcial de una señal del sensor.
Diagnosticado comprobando el voltaje en los contactos sensor con el encendido conectado y los conectores enchufados. Y también la continuidad del cableado desde el sensor hasta la centralita con los conectores retirados.
3) Mal funcionamiento del rotor del sensor (rueda motriz).
Conjunto de sensor de presión de refuerzo y sensor de temperatura del aire
El sensor de presión de sobrealimentación está montado en el colector de admisión y es un sensor de tipo piezorresistivo.
El sensor detecta la presión de sobrealimentación generada por el turbocompresor directamente en el colector de admisión, produciendo una señal de salida a la unidad de control.
El sensor de temperatura del aire de carga está integrado en el sensor de presión de sobrealimentación.
El sensor tiene cuatro cables: alimentación, tierra, cable de señal del sensor de presión de sobrealimentación y cable de señal del sensor de temperatura del aire de carga.
La alimentación del sensor está estabilizada, es de aproximadamente 5 V y la proporciona la unidad de control del motor (terminal B89). El contacto de tierra también está conectado a la unidad de control (terminal B65).
La señal del sensor de presión de refuerzo se envía al terminal B70 de la unidad de control y representa un voltaje que aumenta con el aumento de la presión.
La señal del sensor de temperatura del aire de carga se envía al contacto B23 de la unidad de control.
Sensor de presión del colector de combustible
El sensor de presión de combustible está montado en el acumulador de combustible (múltiple de combustible) y mide valores instantáneos de presión de combustible en el acumulador con precisión y velocidad adecuadas.
El combustible ingresa al sensor a través de un orificio en el acumulador y un canal en la carcasa del sensor, cerrado en el extremo por un diafragma, por lo que el combustible presurizado actúa sobre el diafragma.
El elemento sensor del sensor, a su vez, convierte la presión en una señal eléctrica.
Esta señal se envía al ECM.
Basándose en la señal del sensor de presión de combustible y en función de las señales de otros componentes del sistema de combustible, la unidad de control electrónico del motor realiza los ajustes necesarios para el funcionamiento del sistema de combustible (la presión de combustible necesaria se crea en el acumulador controlando el elemento ejecutivo de la bomba de inyección).
El sensor tiene tres cables: alimentación, tierra y cable de señal.
La alimentación del sensor está estabilizada, es de aproximadamente 5 Voltios y la proporciona la unidad de control del motor (terminal B92).
El contacto de tierra también está conectado a la unidad de control (terminal B68).
La señal del sensor se envía al contacto B69 de la unidad de control y representa un voltaje que aumenta al aumentar la presión.
Sensor de temperatura del refrigerante
El sensor de temperatura del refrigerante está instalado en la caja del termostato.
Detecta la temperatura del refrigerante del motor y transmite una señal a la unidad electrónica de control del motor.
El sensor es un termistor.
La resistencia del sensor disminuye al aumentar la temperatura del refrigerante.
La unidad electrónica de control del motor, basándose en el voltaje de la señal del sensor, estima la temperatura del refrigerante y realiza los ajustes necesarios para el funcionamiento del sistema de combustible.
El sensor tiene dos cables: tierra (terminal B43 de la unidad de control) y un cable de señal, que también es fuente de alimentación (terminal B46 de la unidad de control).
Con el encendido conectado, debe haber una fuente de alimentación estabilizada de aproximadamente 5 V en el pin 2 del conector del sensor desconectado.
Sensor de posición del pedal del acelerador
El sensor de posición del pedal del acelerador es necesario para determinar cuánto ha presionado el conductor el pedal del acelerador.
El sensor consta de dos potenciómetros (resistencias variables) con circuitos independientes (alimentación, señal y tierra).
Por lo tanto, el sensor consta de dos canales: 1 y 2.
Cuando presiona el pedal del acelerador, la resistencia de las resistencias del sensor cambia suavemente en proporción al grado de presión del pedal.
Las señales del sensor de posición del pedal del acelerador que llegan a la unidad electrónica de control del motor se comparan con las curvas características programadas (las señales de los canales 1 y 2 también se comparan entre sí, esto es necesario para controlar la exactitud de las lecturas).
La unidad electrónica, a su vez, genera señales de control de salida, en base a las cuales se controla el funcionamiento del sistema de combustible (por ejemplo, determina el suministro de combustible requerido).
Sensor de presión de aceite de emergencia
El sensor de presión de aceite de emergencia es un sensor de relé (conmutación), cuyos contactos se cierran cuando la presión de aceite en el sistema de lubricación del motor cae por debajo de cierto nivel.
La señal del sensor ingresa a la unidad de control en el pin 37V; el sensor cierra este circuito a tierra.
Cuando se recibe una señal de este sensor mientras el motor está funcionando (se recibe una señal del sensor de posición del cigüeñal), la unidad de control del motor ordena que se encienda el indicador de mal funcionamiento "STOP" en el panel de instrumentos.
Dependiendo de la implementación del sistema de intercambio de datos entre cuadro de instrumentos y unidad de control del motor, este comando se puede transmitir tanto a través de un circuito separado (terminal A49) como a través del bus de datos CAN (terminales 14A y 15A).
Sensor de presión atmosférica
El sensor de presión atmosférica detecta la presión atmosférica actual y envía una señal a la unidad de control del motor.
Este sensor es necesario para el correcto funcionamiento del motor a diferentes altitudes.
El sensor tiene tres cables: alimentación, tierra y cable de señal.
La alimentación del sensor está estabilizada, es de aproximadamente 5 V y la proporciona la unidad de control del motor (terminal B88).
El contacto de tierra también está conectado a la unidad de control (terminal B64).
La señal del sensor se envía al terminal B72 de la unidad de control y representa un voltaje que cambia con la presión.
Actuadores
Bomba de combustible de alta presión (bomba de combustible de alta presión)
Hay un regulador de presión de combustible electromagnético en la bomba de inyección.
Mantiene la presión de funcionamiento del combustible en el acumulador en función de la carga del motor.
Si es necesario aumentar la presión del combustible en el acumulador, la electroválvula reguladora se cierra ante una señal de la unidad electrónica de control del motor, cerrando la etapa de alta presión desde la línea de baja presión (retorno de combustible).
Si es necesario reducir la presión de combustible en el acumulador, la válvula solenoide reguladora, por el contrario, se abre ante una señal de la unidad de control electrónico del motor, desviando parte del combustible hacia la línea de retorno y reduciendo así el combustible. presión en el acumulador.
Inyectores
Los inyectores inyectan combustible en los cilindros del motor según una señal de la unidad electrónica de control del motor.
En un sistema de combustible common rail common rail, se instalan inyectores con accionamiento electromagnético.
Accionamiento de cambio de geometría del turbocompresor
Algunas modificaciones del motor tienen un turbocompresor de geometría variable.
El accionamiento del sistema de cambio de geometría está instalado en el turbocompresor y controla el sistema de cambio de geometría (posición de las palas) del turbocompresor.
La unidad de control electrónico del motor, que recibe datos del sensor de posición del cigüeñal, el sensor de temperatura del refrigerante, el sensor de temperatura del aire de carga, el sensor de presión de sobrealimentación y el sensor de presión atmosférica, que determinan la carga del motor y sus condiciones de funcionamiento, calcula la posición óptima de las cuchillas y suministra señal al motor de accionamiento.
Así, se regula el rendimiento del aparato compresor del turbocargador.
Bus de datos CAN
El bus de datos CAN (Controller Area Network) es un enlace de datos en serie de alta velocidad desarrollado por Bosch.
Alta inmunidad al ruido y protección contra errores.
Se utiliza para reducir la cantidad de cables cuando se comunica en un automóvil.
Cada una de las unidades de control que operan en este bus transmite y recibe datos de forma selectiva.
El bus está hecho según un esquema de dos hilos: canal Can-High (H) y CAN-Low (L).
Los cables están trenzados en un par trenzado para mejorar la inmunidad al ruido del bus.
La longitud máxima de los cables sin trenzar no debe exceder los 40 mm, para garantizar la diferencia de potencial necesaria entre los canales H y L., así como para evitar errores en los mensajes, posibles cuando las señales se reflejan, dentro de los bloques, en los extremos. del bus, en paralelo a los pines CAN, las barras colectoras tienen resistencias integradas, generalmente de 120 ohmios.
Estas resistencias también ayudan a determinar el estado del cableado del bus en sus diferentes ramas: midiendo la resistencia en los contactos correspondientes de los conectores retirados de las unidades de control que operan en el bus CAN, generalmente debería obtener alrededor de 120 o 60 ohmios (una resistencia de 120 ohmios o su conexión en paralelo).
Dependiendo del conector de bloque que se elimine (es posible que haya variaciones).
Dependiendo de la implementación del sistema, estas resistencias se pueden instalar dentro de las unidades de control, dentro de los conectores de bus CAN intermedios o dentro de terminadores de bus CAN especiales.
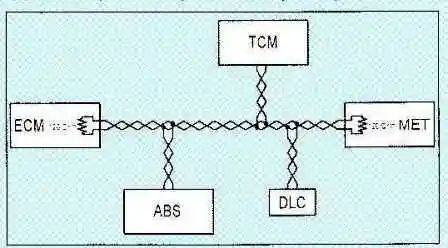
Un ejemplo de construcción de un bus de datos CAN en un automóvil (son posibles varias opciones)
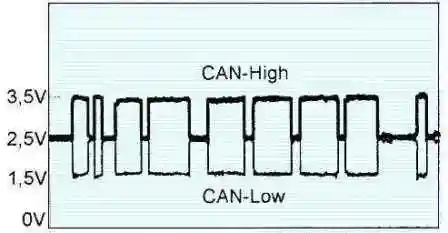
La carga del bus de información depende del número de bloques en él y de la cantidad de información transmitida.
Las señales en ambos canales son siempre simétricas entre sí y están en oposición de fase.
En reposo, ambos canales de bus (alto y bajo) deberían recibir unos 2,5 V (correspondientes a un "1" lógico).
La señal del canal CAN-Low (1) alterna entre su nivel alto de 2,5 V ('1' lógico) y su nivel bajo de 1,5 V ('0' lógico).
La señal del canal CAN-High (H) alterna entre su nivel bajo de 2,5 V (lógico "1") y su nivel alto de 3,5 V (lógico "0").
Por lo tanto, cuando el bus se cambia a la lógica "0", la diferencia de potencial entre los canales es de 2 V.
Los posibles fallos de funcionamiento del bus CAN se encuentran en tres áreas:
- 1) Falla de cableado/conector (abierto, corto, corto a tierra o alimentación).
- 2) Mal funcionamiento de las unidades de control que operan en el autobús.
- 3) Superposición de captadores en el cableado del bus CAN (enrutamiento de cableado incorrecto, el cableado no está trenzado en un par trenzado).
Sistema de control de emisiones
Los motores modernos deben cumplir requisitos de emisiones cada vez más estrictos.
Para que el motor cumpla con los requisitos ambientales más estrictos, se optimiza su diseño, se mejoran el sistema de control y el equipo de combustible, y se instalan subsistemas adicionales para reducir la toxicidad de los gases de escape.
Además, se debe utilizar el combustible correcto.
La siguiente figura muestra un gráfico aproximado del efecto de la implantación de los subsistemas de control de emisiones sobre los correspondientes parámetros de emisión de NOx óxidos de nitrógeno. PM - materia particulada incl. hollín.
Subsistema de recirculación de gases de escape (EGR)
El subsistema de recirculación de gases de escape (EGR) está instalado en algunos modelos de motor para cumplir con los estándares de toxicidad Euro-3, y junto con los estándares de corrección de combustible y Euro-4.
Es posible que no esté disponible en los modelos con motor Euro 3.
El subsistema EGR reduce las emisiones de óxidos de nitrógeno (NOx) a la atmósfera.
El nitrógeno molecular está presente en el aire y en condiciones normales es inerte y no reacciona con el oxígeno, que también está presente en el aire.
Pero, al ingresar a la cámara de combustión del motor, bajo la influencia de altas temperaturas, el nitrógeno se oxida, lo que resulta en la formación de óxidos de nitrógeno tóxicos.
Y cuanto mayor es la temperatura, más óxidos de nitrógeno aparecen.
El sistema EGR dirige parte de los gases de escape desde el colector de escape del motor a través del colector de admisión de regreso a las cámaras de combustión, lo que reduce la temperatura de combustión de la mezcla de aire y combustible y, por lo tanto, reduce la formación de óxidos de nitrógeno.
Composición del subsistema EGR
Hay varias versiones del subsistema EGR. en motores Cummins ISF, dependiendo de cuál varía su composición.
En los motores ISF3.8, el subsistema EGR incluye: un conjunto de válvula EGR, un enfriador EGR y elementos de un sistema de control electrónico.
La válvula EGR dispone de un accionamiento eléctrico que, al mando de la centralita, abre y cierra el canal de recirculación en la medida requerida.
La cantidad de gases recirculados está determinada por el sensor de flujo de masa de aire: una disminución en el flujo de aire le permite a la unidad de control saber que los gases de escape están ingresando al motor.
Un servo del acelerador está montado en el colector de admisión y es necesario para controlar la posición del acelerador.
El servo consta de un motor de CC y un sensor de posición del acelerador.
Un servo de válvula de mariposa en el sistema de admisión de un motor diésel sirve para aumentar el grado de recirculación de gases de escape al reducir el aumento de presión en el colector de admisión (esto se logra cerrando la válvula de mariposa), como resultado de lo cual el escape los gases son aspirados en la admisión.
El control del acelerador se lleva a cabo solo a bajas velocidades.
Desventajas de EGR
Durante el funcionamiento, el hollín contenido en los gases de escape obstruye los canales de recirculación y la válvula EGR.
Por lo tanto, tarde o temprano el movimiento de la válvula se bloquea y deja de realizar sus funciones.
Normalmente, el bloqueo de la válvula se produce cuando está parcialmente abierta, por lo que los gases recirculados siempre se alimentan al conducto de admisión, incluso cuando esto no debería ocurrir.
Esto conduce a una violación de la composición de la mezcla de aire y combustible y, como resultado, la pérdida de potencia disponible, un aumento en el humo de escape pa.
Este problema no siempre se resuelve lavando la válvula: puede fallar y debe ser reemplazada.
Las partículas de escape también obstruyen el colector de admisión y las válvulas de admisión.
La obstrucción puede ser tan grave que el automóvil simplemente puede pararse: el aire deja de fluir hacia el motor.
Lavar el colector de admisión resuelve este problema. Además, debido a la EGR, el aceite de motor pierde sus propiedades más rápidamente.
Además, la EGR empeora la eficiencia de combustible de un motor diésel, lo que provoca una disminución de su eficiencia térmica.
Como puede ver, este subsistema causa algunos daños al motor, por lo que muchos propietarios de automóviles eliminan sus elementos: todas las tuberías de recirculación de gas, una válvula de recirculación, un enfriador de gas (un intercambiador de calor en el que se recircula el calor de los gases de escape transferidos al sistema de enfriamiento del motor) se quitan), se instalan tapones en lugar de todas las boquillas.
Pero esto no es suficiente: si solo se limita la extracción física del subsistema EGR, entonces la unidad de control que controla su funcionamiento detectará un mal funcionamiento e informará al conductor al respecto encendiendo el indicador en el panel de instrumentos.
Por lo tanto, se requiere un parpadeo adicional de la unidad de control del motor (reemplazo del programa de control - ajuste de chip), como resultado de lo cual la unidad ya no controlará los elementos de EGR, y las tarjetas de control de trabajo se reemplazarán con tarjetas que cumplen con los estándares Euro-3.
Filtro de partículas (DPF)
El hollín de los gases de escape de los motores de combustión interna, actuando como carbón activado, recoge sustancias nocivas y es cancerígeno, por lo que su inhalación es altamente indeseable.
Para reducir la cantidad de hollín y otras partículas en los gases de escape de un automóvil, se diseñó el filtro de partículas diésel (Diesel Particulare Filter, DPF).
Su función es captar las partículas de los gases de escape y quemarlas periódicamente (regeneración DPF).
El área de superficie total del elemento filtrante es similar al área de dos campos de fútbol.
Como puede ver en el gráfico anterior, el DPF funciona junto con la EGR: la EGR reduce los óxidos de nitrógeno, pero aumenta la cantidad de partículas en los gases de escape, que a su vez se resuelve con el DPF.
Composición del subsistema DPF
El subsistema DPF consta de un filtro de partículas diésel y un sensor de presión diferencial en el filtro de partículas.
En esta composición, este sistema se instala, por ejemplo, en los autobuses Next Bus.
Se requiere un sensor de presión diferencial en el filtro de partículas para controlar el llenado del filtro.
Sus lecturas permiten que la unidad de control determine el momento en que se requiere la regeneración.
La regeneración del filtro de partículas se realiza calentándolo a una temperatura de unos 700 grados, por lo que las partículas sólidas que se han depositado en sus canales se queman por completo, formando óxidos de carbono gaseosos.
Desventajas del DPF
Los errores en el funcionamiento del vehículo, la mala calidad del combustible, los lubricantes inadecuados, el uso de aditivos de aceite y combustible inadecuados, la conducción frecuente en distancias cortas y la conducción en la ciudad a menudo provocan fallos fatales en el filtro de partículas diésel.
Se vuelve imposible de regenerar.
Ante este problema, el propietario del coche, como en el caso de un catalizador, tiene dos formas de solucionarlo: reemplazándolo por uno nuevo o eliminando el hollín.
El costo de un nuevo filtro de partículas diésel es alto y, a menudo, quitarlo es la única forma de que su automóvil vuelva a funcionar.
Y en este caso, también será necesario un parpadeo de la unidad de control del motor para desactivar mediante programación el filtro de partículas.
Convertidor de reducción catalítica selectiva (SCR)
Este subsistema está diseñado para reducir los óxidos de nitrógeno tóxicos NOx (NO, NO2) en los gases de escape
La presencia de este subsistema elimina la necesidad de utilizar EGR para alcanzar los estándares Euro-4, y su uso junto con otros sistemas para reducir la toxicidad hace posible alcanzar los estándares Euro-5 y Euro-6.
Como puede ver en el gráfico, cuando se utiliza este subsistema, el motor funciona en modos optimizados para reducir las partículas en los gases de escape (combustión optimizada para PM) y, en este caso, aumentar el contenido de NOx en los gases de escape se soluciona mediante el subsistema SCR.
El principio de funcionamiento del sistema SCR es tratar los gases de escape (EG) con una solución acuosa de urea en un convertidor catalítico reductor.
Los óxidos de nitrógeno NOx (NO, NO2) contenidos en los gases de escape se convierten en nitrógeno N2 tras una reacción química con el agente reductor AdBlue en el catalizador > y agua H2O.
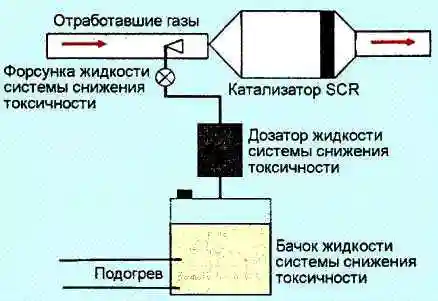
Líquido de control de emisiones (urea)
La solución acuosa de urea utilizada se conoce bajo la marca AdBlue
Reactivo AdBlue, producido mediante una tecnología especial a partir de urea altamente purificada y agua desmineralizada.
La proporción de urea en AdBlue es del 32,5%.
A esta concentración, el reactivo tiene el punto de congelación más bajo de -11 °C.
Cualquier desviación de la concentración de dacha conduce a un aumento en el punto de congelación.
El calentamiento del sistema de suministro de urea se puede realizar tanto mediante resistencias independientes como desde el sistema de refrigeración del vehículo (en este caso, se utiliza la válvula de calentamiento del depósito).
El consumo promedio de reactivos varía según el modelo de motor y debe promediar alrededor del 4 % del consumo de combustible diésel para motores Euro 4.
La vida útil del reactivo es de 1 año.
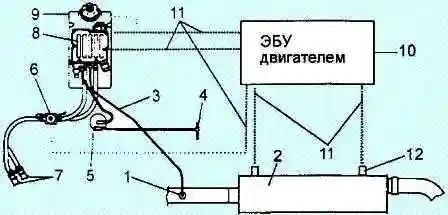
Precauciones
El reactivo no es inflamable y está clasificado como seguro según la directiva EC67/548/EEC.
La introducción de la sustancia en el organismo en pequeñas cantidades no supone un peligro.
Si AdBlue entra en el sistema digestivo.
Es necesario enjuagar la boca y beber abundante agua.
Si la sensación de malestar y malestar persiste, debe consultar a un médico.
El contacto prolongado o la inmersión de partes calientes en un tanque con una sustancia puede causar quemaduras en la piel.
Si es posible el contacto con la sustancia, se deben usar guantes de látex.
Aunque el producto no está clasificado como químico irritante, el contacto directo con los ojos puede causar molestias a corto plazo caracterizadas por lagrimeo o enrojecimiento conjuntival.
En caso de contacto directo de la solución con los ojos, lávelos inmediatamente con abundante agua y consulte a un médico.
Los derrames de reactivos deben limpiarse con cuidado para evitar lesiones, ya que la superficie del derrame se vuelve resbaladiza.
Debe evitar que el líquido entre en contacto con las piezas del automóvil.
Si esto sucede, el líquido debe lavarse con agua y los residuos deben eliminarse de la superficie del cuerpo.
Si AdBlue se seca y cristaliza en la superficie, provocará corrosión.
A altas temperaturas (aproximadamente 70 - 80 °C), el AdBlue se descompone, lo que da lugar a la formación de amoníaco y posibles olores.
La contaminación con materias extrañas y bacterias puede hacer que AdBlue quede inutilizable.
La urea escapada y cristalizada deja manchas blancas que se pueden quitar con agua y un cepillo (inmediatamente si es posible).
AdBlue tiene una gran capacidad de filtración, por lo que los componentes eléctricos y los conectores deben protegerse de AdBlue.
Utilice únicamente AdBlue según el estándar aprobado por el fabricante en el embalaje original.
Para evitar la contaminación, está prohibido reutilizar el AdBlue drenado del sistema.
No se permite el uso de agua, una solución acuosa de urea ordinaria y otros líquidos que no sean AdBlue en el sistema de neutralización, ya que esto puede provocar la falla del sistema de neutralización.
Cuando trabaje con AdBlue, siga las reglas establecidas.
La práctica muestra que varios contaminantes del propio fluido son la causa más común de falla de los sistemas SCR.
El líquido es muy sensible a los materiales con los que entra en contacto, en primer lugar, metales: zinc, aluminio, cobre, fundición y latón.
Al contacto con estos metales se forman sales que, si entran en el catalizador, pueden dañarlo.
Catalizador
Después de suministrar urea al catalizador en la sección de hidrólisis, la urea se descompone en amoníaco NH3 y dióxido de carbono CO2.
En el catalizador de reducción, el amoníaco NH3 reacciona con los óxidos de nitrógeno NOx para formar nitrógeno molecular N2 y agua H2O.
Para el funcionamiento normal del catalizador, debe calentarse a una temperatura de al menos 200°C.
Para controlar la temperatura del catalizador temperatura y temperatura de los gases de combustión, los sensores de temperatura de los gases de escape se utilizan en la entrada y salida del convertidor.
Para monitorear la eficiencia del catalizador, se utiliza un sensor de concentración de óxido de nitrógeno en la salida del convertidor.
Sistema de inyección de urea
La urea se suministra al sistema de escape mediante un dosificador de reactivo (urea), que incluye bomba, dosificador y elementos filtrantes.
Se usa un mezclador para distribuir uniformemente la urea en la corriente de gases de escape.
El depósito de urea dispone de un sensor de nivel con sensor de temperatura incorporado.
¡Atención!
Operar un automóvil sin reactivo AdBlue conduce a una violación del régimen de temperatura y la falla del sistema de neutralización.
La inyección de urea comienza cuando el catalizador alcanza la temperatura de funcionamiento, siempre que se proporcione una cantidad suficiente de urea líquida a temperaturas ambiente bajas.
La inyección de urea se interrumpe cuando el flujo de gases de escape es bajo (ralentí) y la temperatura de los gases de escape es demasiado baja.
Desventajas de SCR
La presencia de este sistema en un automóvil obliga al conductor a mantener el nivel de urea en el tanque, ya que está prohibida la operación de un automóvil con el tanque vacío y la infraestructura de ventas aún está poco desarrollada.
También existen ciertos requisitos para la calidad de los combustibles y lubricantes utilizados.
Funciones personalizadas
La configuración del sistema de gestión del motor con funciones adicionales depende del equipamiento del vehículo.
Estas funciones son programadas por el equipo de diagnóstico.
Algunas funciones adicionales se describen a continuación:
- - Sistema para mantener una velocidad constante (control de crucero). Esta función se puede activar incluso en vehículos que no la tenían originalmente.
Para ello, se configuran los botones de control correspondientes a este sistema, y se cambia el programa de la unidad de control.
- - Límite de velocidad. Es posible que esta característica se haya programado en la fábrica en vehículos diseñados para transportar niños.
Deshabilitar esta función, si el propósito del vehículo ha cambiado, también es posible reemplazando el programa de control.
- - Aumente la velocidad de ralentí del motor.
Esta función se puede activar en vehículos equipados con control de crucero.
Para hacer esto, se cambia el programa de la unidad de control, después de lo cual se establece la velocidad del motor en un vehículo parado usando los botones de control de crucero, freno motor (si está equipado).
- - Funciones necesarias para el funcionamiento del sistema de toma de fuerza: control del motor a velocidad constante, acelerador remoto.
- - Algunas funciones de protección necesarias para el funcionamiento del motor y otros sistemas: fijación de la velocidad máxima del motor, control de la carga de la batería, inmovilizador, intervalos de servicio, limitación de par (protección de engranajes), cambio descendente.