Двигун ВАЗ-2123 бензиновий чотиритактний, чотирициліндровий, восьмиклапанний, рядний, з верхнім розташуванням розподільчого валу
Порядок роботи циліндрів: 1—3—4—2, відлік — від шківа приводу допоміжних агрегатів
Тип системи живлення — розподілене упорскування палива
Керування двигуном здійснює контролер BOSCH M7.9.7 (норми токсичності Євро-4).
У системі випуску відпрацьованих газів встановлено каталітичний нейтралізатор.
Дело на двигуні (по ходу автомобіля) розташовано: ресивер з дросельним вузлом, датчиком положення дросельної заслінки та регулятором холостого ходу; впускна труба та випускний колектор; паливна рампа із форсунками; датчики детонації та температури охолоджуючої рідини системи управління; термостат; насос охолоджувальної рідини; стартер (закріплений на картері зчеплення); компресор кондиціонера (на автомобілі з кондиціонером).
Зліва на двигуні розташовані: генератор, насос гідропідсилювача рульового керування, свічки запалювання та дроту високої напруги, котушка запалювання, вимірювальний щуп рівня масла, масляний фільтр, датчики вказівника температури охолоджуючої рідини (у комбінації приладів) та недостатнього тиску масла.
Повітряний фільтр з датчиком масової витрати повітря закріплений у моторному відсіку ліворуч від двигуна.
Спереду — привід допоміжних агрегатів (полікліновим ременем), датчик положення колінчастого валу та датчик фаз.
Двигун із коробкою передач та зчепленням утворюють силовий агрегат, закріплений на трьох еластичних гумометалевих опорах.
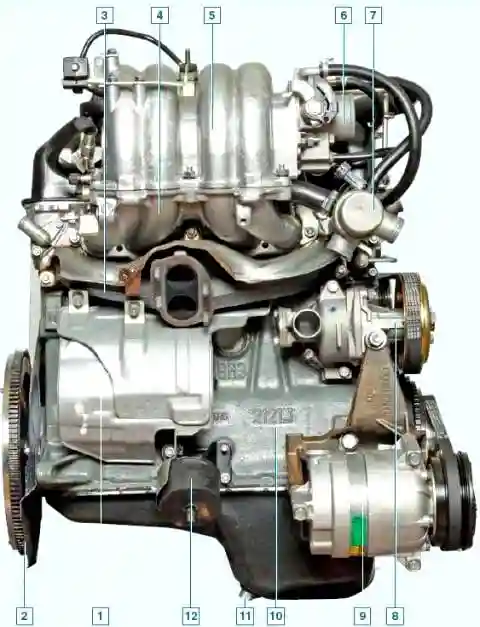
Вигляд двигуна праворуч: 1 - щиток стартера; 2 – маховик; 3 – випускний колектор; 4 - впускна труба; 5 – ресивер; 6 – дросельний вузол; 7- термостат; 8 - насос охолоджувальної рідини; 9 – компресор кондиціонера; 10 – блок циліндрів; 11 - пробка зливного отвору піддону картера; 12 - права опора силового агрегату
Блок циліндрів двигуна відлитий із спеціального низьколегованого чавуну, циліндри розточені безпосередньо в блоці.
Номінальний діаметр циліндра — 82,00 мм, допуск на обробку + 0,05 мм.
Розрахунковий мінімальний зазор між поршнем і циліндром (для нових деталей) повинен дорівнювати 0,025—0,045 мм.
Він визначається як різниця розмірів мінімального діаметра циліндра і максимального діаметра поршня і забезпечується установкою в циліндр поршня того ж класу, що й циліндр.
Для цього циліндри та поршні в залежності від розмірів, отриманих при механічній обробці, розбивають на п'ять класів через 0,01 мм.
Клас циліндра відповідно до його діаметра маркується латинськими літерами на нижній площині блоку циліндрів: А - 82,00-82,01, В - 82,01-82,02, С - 82,02-82,03, 13 - 82,03-82,04, Е - 82,04-82,05 мм.
Під час ремонту діаметр циліндра може бути збільшений розточкою на 04 або 08 мм під поршні збільшеного розміру.
Максимально допустиме зношування циліндра 0,15 мм на діаметр.
У нижній частині блоку циліндрів розташовано п'ять опор корінних підшипників колінчастого валу зі знімними кришками, які кріпляться до блоку спеціальними болтами.
Отвори в блоці циліндрів під підшипники обробляються при встановлених кришках, тому кришки не взаємозамінні і для відмінності марковані ризиками на зовнішній поверхні.
На торцевих поверхнях задньої опори є гнізда для завзятих напівкілець, що перешкоджають осьовому переміщенню колінчастого валу.
Спереду встановлюється сталеалюміневе півкільце (білого кольору), а ззаду — металокерамічне (жовте). При цьому пази на них мають бути звернені до колінчастого валу.
Напівкільця поставляються номінального та збільшеного на 0,127 мм розмірів.
Якщо осьовий зазор (люфт) колінчастого валу виходить за межі 0,06—0,26 мм, то необхідно замінити одне або обидва півкільця (максимально допустимий осьовий зазор колінчастого валу в експлуатації — 0,35 мм).
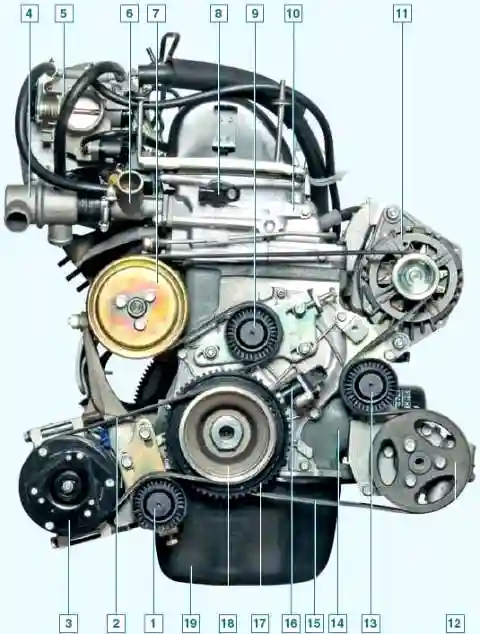
Вигляд двигуна спереду: 1 - натяжний ролик ременя приводу компресора кондиціонера; 2 - ремінь приводу компресора кондиціонера; 3 – муфта компресора кондиціонера; 4 – термостат; 5 – дросельний вузол; 6 - відвідний патрубок сорочки охолодження; 7- шків насоса охолоджуючої рідини; 8 - датчик фаз; 9 - натяжний ролик ременя приводу допоміжних агрегатів; 10 – головка блоку циліндрів; 11 - генератор; 12 - шків насоса гідропідсилювача рульового керування; 13 - опорний ролик ременя приводу допоміжних агрегатів; 14 - блок циліндрів; 15 – ремінь приводу допоміжних агрегатів; 16 - датчик положення колінчастого валу; 17 - шків приводу допоміжних агрегатів; 18 - шків приводу компресора кондиціонера; 19 - піддон картера
Вкладиші корінних та шатунних підшипників колінчастого валу — тонкостінні сталеалюмінієві.
Верхні вкладиші корінних підшипників першої, другої, четвертої та п'ятої опор з проточкою на внутрішній поверхні, а верхній вкладиш третьої опори та нижні вкладиші, що встановлюються у кришки, — без проточки.
Ремонтні вкладиші корінних та шатунних підшипників випускаються під шийки колінчастого валу, зменшені на 0,25, 0,5, 0,75 та 1,00 мм.
Номінальний розрахунковий діаметральний зазор між шийками колінчастого валу та вкладишами підшипників повинен становити:
- - для корінних підшипників - 0,026-0,073 мм (максимально допустимий зазор - 0,15 мм);
- - для шатунних підшипників - 0,02-0,07 мм (максимально допустимий зазор - 0,1 мм).
Колінчастий вал — з високоміцного чавуну, має п'ять корінних і чотири шатунні шийки.
Вал забезпечений вісьма противагами, відлитими разом з валом (повнопротивоваговий).
Для подачі масла від корінних шийок до шатунних у ньому просвердлені канали, закриті запресованими та зачеканими заглушками.
Ці канали служать також для очищення масла: під дією відцентрової сили тверді частинки та смоли, що пройшли через фільтр, відкидаються до заглушок.
Тому при ремонті валу і при балансуванні необхідно очищати канали від накопичених відкладень.
Заглушки повторно використовувати не можна — їх замінюють на нові.
На передньому кінці (шкарпетці) колінчастого валу на сегментній шпонці встановлені зірочка, що приводить газорозподільний механізм (ГРМ), і шків приводу допоміжних агрегатів (генератора, насоса гідропідсилювача рульового управління та насоса охолоджуючої рідини), який також є демпфером крутильних коліс .
На автомобілі з кондиціонером до шківа приводу допоміжних агрегатів гайкою колінчастого валу притягнуто шків приводу компресора кондиціонера.
На шківі приводу допоміжних агрегатів виконано зубчастий вінець для зчитування інформації датчиком положення колінчастого валу.
Венок має 58 зубів (коло вінця розбито на 60 зубів, але два відсутні, утворюючи западину, — це необхідно для отримання імпульсу синхронізації при кожному обороті колінчастого валу).
По зовнішній циліндричній поверхні шківа працює передній сальник колінчастого валу, встановлений у кришці приводу ГРМ, відлитої з алюмінієвого сплаву.
Кришка приводу ГРМ має приплив з отвором під датчик положення колінчастого валу.
Задній сальник запресований у відлитий з алюмінієвого сплаву тримач, який кріпиться до заднього торця блоку циліндрів.
Сальник працює по поверхні фланця колінчастого валу.
У задній торець колінчастого валу запресовано передній підшипник первинного валу коробки передач.
До фланця колінчастого валу шістьма болтами через загальну шайбу кріпиться маховик.
Він відлитий з чавуну і має напресований сталевий зубчастий вінець для пуску двигуна стартером.
Маховик встановлюють так, щоб конусоподібна лунка біля його вінця знаходилася навпроти шатунної шийки 4-го циліндра — це необхідно для визначення ВМТ після збирання двигуна.
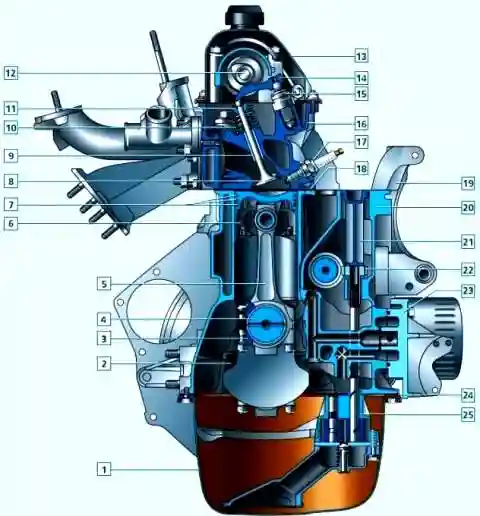
Поперечний розріз двигуна: 1 - піддон картера; 2 – кришка корінного підшипника; 3 – кришка шатуна; 4 - колінчастий вал; 5 – шатун; 6 – поршень; 7 поршневі кільця; 8 – клапан; 9 - напрямна втулка клапана; 18 – клапанні пружини; 11 – тарілка; 12 – розподільчий вал; 13 - кришка головки блоку циліндрів; 14 – важіль клапана; 15 - гідроопора; 18 – головка блоку циліндрів; 17 – свічка запалювання; 18 - прокладання головки блоку циліндрів; 19 – кронштейн генератора; 28 - блок циліндрів; 21 – фіксатор шестерні масляного насоса; 22 - шестерня масляного насосу; 23 - кронштейн масляного фільтра; 24 - прокладання піддону картера; 25 - масляний насос
Шатуни — сталеві, двотаврові перерізи, обробляються разом з кришками.
Щоб при складанні не переплутати кришки, на них, як і на шатунах таврується номер циліндра (він повинен знаходитися по один бік шатуна та кришки).
У отвори нижньої головки шатуна запресовані спеціальні болти; при розбиранні їх не можна вибивати з голівки.
У верхню головку шатуна запресована сталебронзова втулка.
По діаметру її отвору під поршневий палець шатуни поділяються на три класи з кроком 0,004 мм (так само, як і поршні).
Номер класу таврується на верхній головці шатуна.
Шатуни також поділяюся на 9 класів за масою, які маркуються фарбою різних кольорів на стрижнях шатунів.
Всі шатуни двигуна мають бути одного класу по масі, тобто позначені фарбою одного кольору.
Поршневий палець — сталевий, трубчастий переріз, плаваючий тип (вільно обертається в бобишках поршня і в головці шатуна), від випадіння зафіксований двома стопорними пружинними кільцями, розташованими в проточках бобишок поршня.
По зовнішньому діаметру розрізняють три класи пальців (через 0,004 мм), які маркуються фарбою:
- 1 - синій (21,970-21,974 мм), 2 - зелений (21,974-21,978 мм), 3 - червоний (21,978-21,982 мм).
Поршень — литий з алюмінієвого сплаву.
Спідниця поршня має складну форму: у поздовжньому перерізі вона бочкоподібна, а в поперечному — овальна.
У верхній частині поршня проточено три канавки під поршневі кільця.
Канавка маслознімного кільця має свердління для підведення масла, зібраного кільцем зі стінок циліндра, до поршневого пальця.
Отвір під поршневий палець зміщений на 1,2 мм від діаметральної площини поршня, тому при встановленні поршня необхідно орієнтуватися за вибитою стрілкою на його днищі: вона повинна бути спрямована у бік шківа колінчастого валу.
За зовнішнім діаметром (номінальний розмір) поршні розбивають на 5 класів: А - 81,965-81,975, В - 81,975-81,985, С - 81,985-81,995, D - 81,995-82,002,0 -5. Клас поршня таврується літерою на його днище.
У поршнів ремонтних розмірів на днищі вибивається трикутник (збільшення діаметра на 04 мм) або квадрат (збільшення діаметра на 0,8 мм).
У запасні частини постачають поршні трьох класів — A, C та Е (номінального та ремонтних розмірів), що цілком достатньо для підбору поршня до циліндра.
При цьому не рекомендується встановлювати новий поршень у зношений циліндр без розточування циліндра.
Проточка під верхнє поршневе кільце в новому поршні може виявитися трохи вищою, ніж у старому, і кільце зламається про «сходинку», що утворюється у верхній частині циліндра при його зносі.
За діаметром отвору під поршневий палець поршні поділяються на 3 класи: 1—21,982—21,986, 2 — 21,986—21,990, 3 — 21,990—21,994 мм.
Номер класу також вибивається на днище поршня.
У нових деталей клас отворів під палець у шатуні та поршні повинен бути ідентичний класу пальця.
Поршні двигуни випускаються одного класу за масою, тому окремо підбирати їх не потрібно.
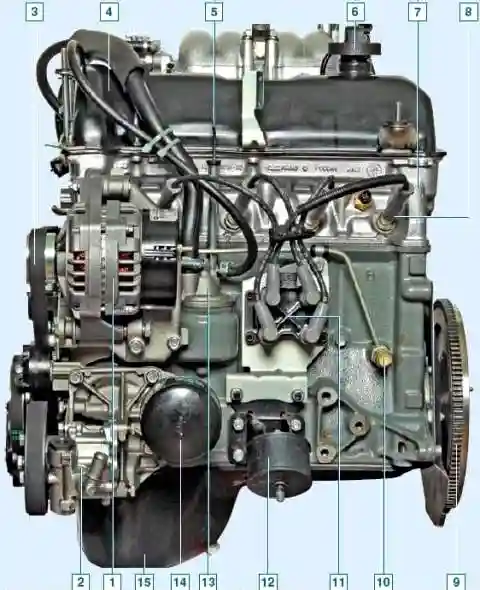
Вигляд двигуна зліва: 1 - генератор; 2 - насос гідропідсилювача керма; 3 – ремінь приводу допоміжних агрегатів; 4 – кришка головки блоку циліндрів; 5-покажчик рівня масла; 6 - кришка маслозаливної горловини; 7 – головка блоку циліндрів; 8 – свічка запалювання; 9 – маховик; 10 - датчик контрольної лампи недостатнього тиску олії; 11 - котушка запалювання; 12 – ліва опора силового агрегату; 13 - маслоотделитель системи вентиляції картера; 14 - масляний фільтр; 15 - піддон картера
Поршневі кільця розташовані в канавках поршня.
Два верхні кільця — компресійні. Вони перешкоджають прориву газів у картер двигуна та відводять тепло від поршня до циліндра.
Нижнє поршневе кільце — маслознімне.
Номінальний зазор по висоті між поршневими кільцями та канавками в поршні (вимірюється набором щупів) повинен становити:
- - для верхнього компресійного кільця - 0,04-0,07 мм; для нижнього - 003-006 мм;
- - для маслознімного - 0,02-0,05 мм.
гранично допустимі зазори при зносі — 0,15 мм.
Зазор у замку для всіх поршневих кілець повинен становити 0,25—0,45 мм.
Зазор вимірюють набором щупів, вставивши кільце в спеціальний калібр або циліндр двигуна і вирівнявши його днищем поршня.
Головка блоку циліндрів — із алюмінієвого сплаву, загальна для всіх чотирьох циліндрів.
Вона центрується на блоці циліндрів двома втулками і кріпиться 11 болтами.
Якщо довжина стрижня болта перевищує 117 мм, його слід замінити новим.
Між блоком та головкою встановлюється безсадкова металоармована прокладка.
Повторне використання прокладки не допускається.
У верхній частині головки блоку циліндрів на дев'яти шпильках закріплений алюмінієвий корпус підшипників розподільчого валу.
Він центрується на двох втулках, одягнених на крайні шпильки.
Зазор між шийками розподільчого валу та опорами корпусу не повинен перевищувати 0,2 мм.
Розподільний вал — литий чавунний з вибіленими кулачками, п'ятиопорний; приводиться в обертання однорядним роликовим ланцюгом від зірочки колінчастого валу.
Восьове переміщення обмежене завзятим фланцем, що входить у проточку передньої опорної шийки валу.
Для правильної установки фаз газорозподілу на зірочках є мітки.
При цьому мітка на зірочці колінчастого валу повинна збігтися з виступом на блоці циліндрів, а мітка на зірочці розподільчого валу — поєднатися з виступом на корпусі підшипників.
Зірочка розподільного валу встановлюється на вал тільки в одному положенні і затягується болтом з опорною та фіксуючою шайбами.
Вусик останньої входить в отвір у зірочці, а бічна частина відгинається на грань головки болта.
До зірочки приклепано металевий елемент — задатчик датчика фаз.
Сідла та напрямні втулки клапанів — чавунні, запресовані в головку блоку циліндрів.
У запасні частини поставляються ремонтні втулки зі збільшеним на 0,2 мм зовнішнім діаметром.
Отвори у втулках остаточно обробляються розгорткою після запресування.
Діаметр отвору втулок впускних клапанів — 8,022—8,040 мм, випускних — 8,029—8,047 мм.
На внутрішній поверхні втулки нарізані канавки для змащення: у втулки впускного клапана — на всю довжину, у випускного — до половини довжини отвору.
Зверху на втулки одягнені металорізові олійно-відбивні ковпачки (сальники клапанів) з браслетною сталевою пружиною.
Зазори між новими напрямними втулками та стрижнями клапанів повинні знаходитися в межах 0,022—0,055 мм для впускних клапанів та 0,029—0,062 мм для випускних (граничний зазор при зносі в процесі експлуатації становить 0,3 мм).
Клапани — сталеві; випускні — з головками із жароміцної сталі, із наплавленими фасками.
Клапани розташовані в ряд, похило до площини, що проходить через осі циліндрів.
Діаметр тарілки впускного клапана (37 мм) більший, ніж випускного (31,5 мм).
Клапани наводяться від кулачків розподільчого валу через важелі («рокери»).
Зазори клапанів не регулюються.
Одним кінцем важіль спирається на сферичну головку гідроопори (гідрокомпенсатора зазору), а іншим впливає на торець стрижня клапана.
На двигуні встановлені гідроопори фірми INA, які за конструкцією відрізняються від гідроопор, що застосовувалися раніше.
У головку циліндрів спочатку повертають сталеву втулку (корпус), а вже в неї на посадці, що ковзає, вставляють опору.
При такому способі складання виключається можливість деформації прецизійної пари гідроопори.
Для підведення моторного масла під тиском до гідроопорів між корпусами гідроопор і головкою блоку циліндрів встановлено чотири алюмінієві проставки — одна проставка для гідроопор двох клапанів кожного циліндра.
По каналу блоку циліндрів і головки блоку масло надходить до корпусу підшипників розподільного валу, а потім трубчастою сталевою рампою — до проставок гідроопор клапанів.
З'єднання трубок рампи з проставками ущільнені гумовими втулками.
Використання гідроопор фірми INA спричинило застосування нових важелів клапанів, у яких зменшився діаметр опорної сфери — з 12 мм (у колишніх важелів) до 11 мм.
Клапан закривається під дією двох пружин із протилежною навивкою, встановлених коаксіально (співвісно).
Нижніми кінцями вони спираються на опорні шайби, а верхніми — на тарілку, що фіксується двома конусними сухарями, що входять у проточку на кінці стрижня клапана.
Для зменшення коливань ланцюга газорозподільного механізму на його лівій гілки між зірочкою валика приводу масляного насоса та зірочкою розподільного валу на двох болтах встановлено пластмасовий заспокійник.
Права гілка ланцюга натягується пружинногідравлічним натягувачем, встановленим у головці блоку циліндрів.
Попередній натяг ланцюга (на двигуні, що не працює) забезпечується пружиною, робоче (після пуску двигуна) — підпором масла під тиском.
Олія в гідронатяжник подається по сталевій цільнотягнутій трубці діаметром 6 мм з наконечниками.
Починається ця магістраль від різьбового отвору на лівій стінці блоку циліндрів, до якого вкручено штуцер датчика аварійного тиску масла.
Правильно підібрана згинальна жорсткість трубки дозволила послабити її коливання, до того ж використовуються металеві тримачі з гумовими вставками, що пригнічують вібрацію.
Наконечник трубки кріпиться до корпусу натягувача за допомогою болта-штуцера, який застосовується для кріплення шланга переднього гальмівного механізму автомобілів заднього та повнопривідних сімейств ВАЗ.
Плунжер натягувача тисне на черевик, виготовлений, як і заспокоювач ланцюга, із зносостійкої пластмаси.
Башмак натягувача повертається на осі, розташованої в нижній частині блоку циліндрів, праворуч від зірочки колінчастого валу.
Від ланцюга газорозподільного механізму наводиться і валик приводу масляного насоса.
Кріплення його зірочки (30 зубів) аналогічне кріпленню зірочки розподільчого валу (38 зубів).
Валик обертається у втулках, розпокладених у блоці циліндрів, і від осьових переміщень утримується завзятим фланцем, що входить у проточку на його передній шийці.
Зубчастий вінець валика входить у зачеплення з шестернею приводу масляного насоса, встановленої вертикально у втулці блоку циліндрів.
У шестерні виконано поздовжній отвір зі шліцами, до якого знизу входить шліцевий хвостовик валика масляного насоса.
Масляний насос — шестерний, одноступінчастий, з редукційним клапаном; змонтований у корпусі, закріпленому у нижній частині блоку циліндрів.
Приймальний патрубок відлитий разом з нижньою частиною корпусу і закритий штампованою сіткою для грубого очищення олії від механічних домішок.
Номінальні зазори в масляному насосі повинні становити:
- - між зубцями шестерень - 0,15 мм (гранично допустиме значення - 0,25 мм);
- - між шестернями (за зовнішнім діаметром) та стінками корпусу насоса - 0,11-0,18 мм (гранично допустиме значення - 0,25 мм);
- - між торцями шестерень і площиною корпусу - 0,066-0,161 мм (гранично допустиме значення - 0,20 мм);
- - між веденою шестернею та її віссю - 0,017-0,057 мм (гранично допустиме значення - 0,10 мм);
- - між валом насоса та отвором у корпусі — 0,016—0,055 мм (гранично допустиме значення — 0,10 мм).
Змащення двигуна є комбінованим.
Під тиском масло подається через фільтр до корінних та шатунних підшипників колінчастого валу, гідроопорів важелів клапанів, гідронатягувачу ланцюга, підшипникам розподільчого валу та втулці валика приводу масляного насоса.
Розбризкуванням масло подається на стінки циліндрів (далі до поршневих кільців і пальців), до пар кулачок розподільчого валу — важіль, ланцюги та стрижні клапанів.
Масляний фільтр — повнопоточний, нерозбірний, з перепускним та протидренажним клапанами.
Система вентиляції картера - закрита, примусова. Під дією розрідження у впускному трубопроводі працюючого двигуна гази з його картера через масловідділювач потрапляють у впускний тракт шлангами двох контурів.
Через шланг (великого діаметру) основного контуру картерні гази відводяться на режимах часткових та повних навантажень роботи двигуна в простір перед дросельною заслінкою.
Через шланг контуру холостого ходу картерні гази відводяться в простір за дросельною заслінкою як на режимах часткових та повних навантажень роботи двигуна, так і на режимі холостого ходу.