We examined the engine disassembly in the article - Engine disassembly.
In this article, we will consider the defect detection of parts and the preparation of the main parts for assembly.
Cylinder block
The cylinder block of the VAZ-2112 engine also has the number "21083" like the engines 2110 and 2111, but they are not interchangeable: the holes for the cylinder head screws have a M10x1.25 thread (unlike M12x1.25 for engine blocks 2110 and 2111 ) and less depth.
Another difference is related to the more intense thermal conditions of the 2112 engine compared to the 2110 and 2111 engines.
To cool the pistons during engine operation, their bottoms are washed from below with oil through special nozzles pressed into the second, third, fourth and fifth main bearing supports.
Cylinders are bored directly in the block.
The nominal diameter of 82 mm can be increased by 0.4 or 0.8 mm during repairs.
The class of the cylinder is marked on the lower plane of the block in Latin letters in accordance with the diameter of the cylinder in mm: A - 82.00-82.01, B - 82.01-82.02, C - 82.02-82.03, D - 82.03-82.04, E - 82.04-82.05.
The maximum allowable cylinder wear is 0.15 mm per diameter.
Wash the cylinder block thoroughly and clean the oil passages.
Blow and dry with compressed air, inspect the cylinder block.
Cracks in bearings or other areas of the cylinder block are not allowed.
If there is a suspicion that coolant has entered the crankcase, then check the tightness of the cylinder block on a special stand.
To do this, after plugging the holes in the cooling jacket of the cylinder block, inject water at room temperature into it at a pressure of 0.3 MPa (3 kgf / cm 2).
There should be no water leakage from the cylinder block for two minutes.
If oil gets into the coolant, then without completely disassembling the engine, check for cracks in the cylinder block in the areas of the oil channels.
To do this, drain the coolant from the cooling system, remove the cylinder head, fill the cooling jacket of the cylinder block with water and supply compressed air to the vertical oil channel of the cylinder block.
If air bubbles appear in the water filling the cooling jacket, replace the cylinder block.
Check the split plane of the cylinder block with the head using a ruler and a set of feeler gauges.
The ruler is set along the diagonals of the plane and in the middle in the longitudinal direction and across.
The flatness tolerance is 0.1 mm.
Check if the wear of the cylinders exceeds the maximum allowable - 0.15 mm.
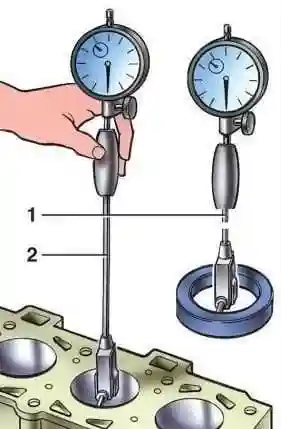
Measurement of cylinders with a bore gauge
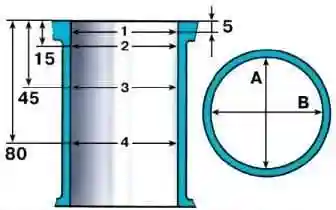
Cylinder diameter is measured by a bore gauge in four zones, both in the longitudinal and transverse directions of the engine.
The caliber 67.8125.9502 is used to set the inside gauge to zero.
In the zone of belt 1, the cylinders practically do not wear out.
Therefore, by the difference in measurements in the first and other zones, one can judge the amount of cylinder wear.
If the maximum wear value is more than 0.15 mm, bore the cylinders to the nearest repair size, leaving an allowance of 0.03 mm for the honing diameter.
Then honing the cylinders, maintaining such a diameter that when installing the selected repair piston, the estimated clearance between it and the cylinder is 0.025–0.045 mm.
Checking the piston
Clean the piston from carbon deposits and remove all deposits from the lubrication channels of the piston and connecting rod.
Inspect the details carefully.
Cracks of any nature on the piston, piston rings, pin, on the connecting rod and its cover are not allowed.
If there are deep marks on the working surface of the liners, replace the liners with new ones.
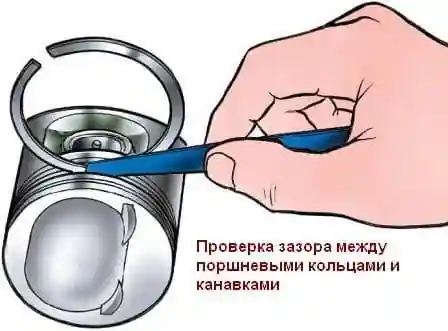
Check the gap between the piston rings and the grooves with a set of feeler gauges, as shown in the figure, inserting the ring into the corresponding groove.
The nominal (calculated) gap for the top compression ring is 0.04-0.075 mm, for the lower one - 0.03–0.065 mm and for the oil scraper - 0.02–0.055 mm.
Maximum allowable gaps for wear - 0.15 mm.
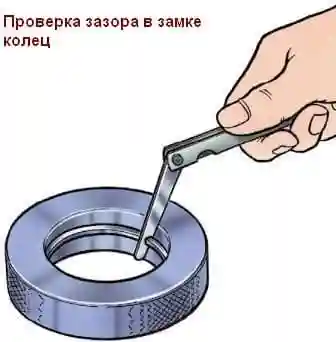
Check the gap in the lock of the piston rings with a set of feeler gauges, inserting the rings into a gauge having a bore diameter equal to the nominal diameter of the ring with a tolerance of ±0.003 mm.
For normal size rings with a diameter of 82 mm, caliber 67.8125.9502 can be used. The gap should be between 0.25-0.45 mm for all new rings.
Maximum wear gap 1 mm.
Crankshaft
The crankshaft of the 2112 engine differs from the crankshaft of the 2110 and 2111 engines in the form of counterweights and increased strength.
Therefore, it is not allowed to install the crankshaft from engines 2110 and 2111 in the engine 2112.
To supply oil from the main journals to the connecting rods, channels are drilled in the crankshaft, the outlets of which are closed with pressed plugs.
At the front end of the crankshaft, a camshaft drive gear pulley is mounted on a segment key, a generator drive pulley is attached to it, which is also a crankshaft vibration damper.
Two teeth out of 60 are missing on the gear ring of the pulley - the cavities are used for the operation of the crankshaft position sensor.
Inspect the crankshaft. Cracks anywhere on the crankshaft are not allowed.
On surfaces mating with the working edges of the seals, scratches, nicks and marks are not allowed.
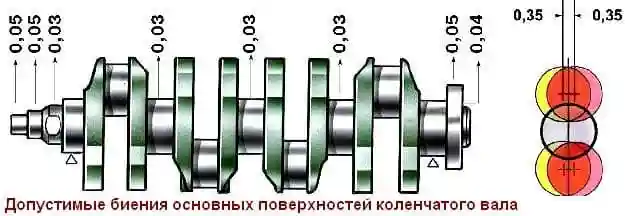
Install the crankshaft with extreme main journals on two prisms and check the runout with an indicator:
- - main journals and seating surface for the drive gear of the oil pump (no more than 0.03 mm);
- - landing surface for the flywheel (no more than 0.04 mm);
- - seating surface for pulleys and surfaces mating with oil seals (no more than 0.05 mm).
Measure the diameters of the main and connecting rod journals.
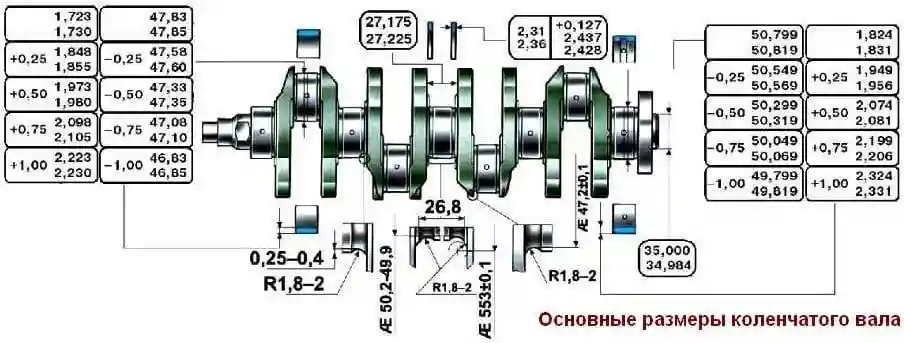
The necks should be ground if their wear is more than 0.03 mm or the ovality of the necks is more than 0.03 mm, and also if there are scuffs and scratches on the necks.
Grind the necks with a reduction in diameter to the nearest repair size.
When grinding, maintain the dimensions of the journal fillets similar to those shown in Figure 6 for normal crankshaft dimensions.
The ovality and taper of the main and connecting rod journals after grinding should be no more than 0.005 mm.
The displacement of the axes of the connecting rod journals from the plane passing through the axes of the connecting rod and main journals after grinding should be within ± 0.35 mm.
To check, install the shaft with extreme main journals on prisms and set the shaft so that the axis of the connecting rod journal of the first cylinder is in a horizontal plane passing through the axes of the main journals.
Then, use an indicator to check the vertical displacement of the crankpins of the 2nd, 3rd and 4th cylinders relative to the crankpin of the 1st cylinder.
After grinding the necks, polish them with diamond paste or GOI paste.
After grinding and subsequent finishing of the necks, remove the plugs of the oil channels, and then process the sockets of the plugs with a cutter A. 94016/10, put on the spindle A. 94016.
Rinse the crankshaft and its passages thoroughly to remove abrasive residues and blow with compressed air.
Using drift A.86010, press in new plugs and score each at three points with a center punch.
On the first cheek of the crankshaft, mark the amount of reduction in the main and connecting rod journals (for example, K 0.25; W 0.50).
Inserts. No adjustment operations can be performed on the liners.
When scuffing, scratches, or peeling, replace the liners with new ones.
The gap between the liners and the crankshaft journals is checked by calculation (by measuring the details).
It is convenient to use a calibrated plastic wire to check the gap. In this case, the validation method is as follows:
- - carefully clean the working surfaces of the liners and the corresponding neck and place a piece of plastic wire on its surface;
- - install a connecting rod with a cap or a main bearing cap on the neck (depending on the type of neck being checked) and tighten the nuts or fastening bolts.
Conrod nuts tighten the bolts to a torque of 51 Nm (5.2 kgf m), and the bolts of the main bearing caps to a torque of 80.4 Nm (8.2 kgf m);
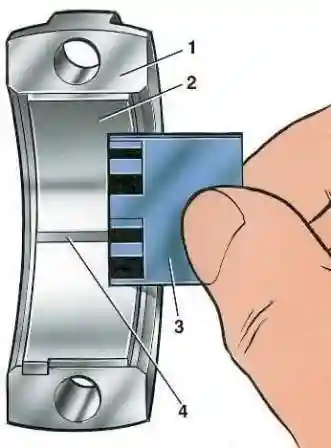
- - remove the cover and use the scale printed on the package to determine the size of the gap by the flattening of the wire.
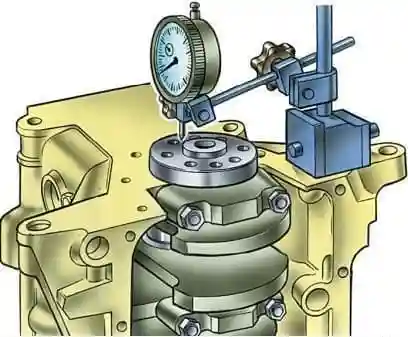
The nominal design clearance is 0.02–0.07 mm for connecting rod journals and 0.026–0.073 mm for main journals.
If the gap is less than the limit (0.1 mm for connecting rod and 0.15 mm for main journals), then these liners can be used again.
If the gap is greater than the limit, replace the liners on these necks with new ones.
If the crankshaft journals are worn out and ground to a repair size, then replace the liners with repair ones (increased thickness).
Thrust half rings. As well as on liners, no fitting operations can be performed on half rings.
In case of scuffing, risks or delaminations, replace the half rings with new ones.
Half rings are also replaced if the axial clearance of the crankshaft exceeds the maximum allowable - 0.35 mm.
For new half-rings, select a nominal thickness or increased by 0.127 mm to obtain an axial clearance in the range of 0.06–0.26 mm.
Check the free axial play of the crankshaft.
To do this, turn the cylinder block with its rear side up and install a stand with an indicator on it so that the indicator leg rests against the crankshaft flange.
Moving the shaft up and down (for example, with screwdrivers), measure the free axial movement of the shaft with an indicator
Flywheel
Check the condition of the toothed rim and replace the flywheel if the teeth are damaged.
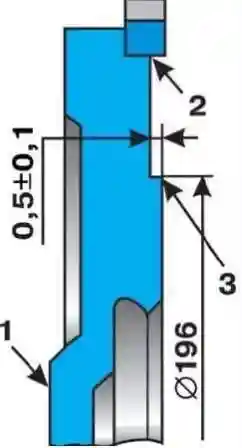
If the flywheel has discoloration on surface 3, check the rim tightness on the flywheel.
The rim must not rotate with a torque of 590 Nm (60 kgf m) or move axially under a force of 3.9 kN (400 kgf).
On surface 1 of the flywheel adjacent to the crankshaft flange, and on surface 3 under the clutch disc, scratches and scuffs are not allowed.
The non-flatness tolerance of surface 3 is 0.06 mm.
Remove scratches and scuffs on surface 3 with a groove, removing a layer of metal no more than 1 mm thick.
At the same time, also grind surface 2 without affecting the gear rim and maintaining a dimension of (0.5 ± 0.1) mm.
When turning, it is necessary to ensure that surfaces 2 and 3 are parallel with respect to surface 1.
Tolerance of non-parallelism 0.1 mm.
Mount the flywheel on the arbor, centering it on the bore against surface 1, and check the runout of planes 2 and 3.
In the places indicated by the arrows in the figure, the indicator should not show beats exceeding 0.1 mm.