Discutimos el desmontaje del motor en el artículo - Desmontaje del motor.
En este artículo, consideraremos la detección de defectos de piezas y la preparación de las piezas principales para el montaje.
Bloque de cilindros
El bloque de cilindros del motor VAZ-2112 también tiene el número "21083" como los motores 2110 y 2111, pero no son intercambiables: los orificios para los tornillos de la culata tienen una rosca M10x1.25 (a diferencia de M12x1.25 para bloques de motor 2110 y 2111) y menor profundidad.
Otra diferencia está relacionada con las condiciones térmicas más intensas del motor 2112 en comparación con los motores 2110 y 2111.
Para enfriar los pistones durante el funcionamiento del motor, sus fondos se lavan desde abajo con aceite a través de boquillas especiales presionadas en los soportes del cojinete principal segundo, tercero, cuarto y quinto.
Los cilindros se perforan directamente en el bloque.
El diámetro nominal de 82 mm se puede aumentar en 0,4 o 0,8 mm durante las reparaciones.
La clase del cilindro está marcada en el plano inferior del bloque en letras latinas de acuerdo con el diámetro del cilindro en mm: A - 82.00-82.01, B - 82.01-82.02, C - 82.02-82.03, D - 82.03-82.04, E - 82.04-82.05.
El desgaste máximo permitido del cilindro es de 0,15 mm por diámetro.
Lave bien el bloque de cilindros y limpie los conductos de aceite.
Sople y seque con aire comprimido, inspeccione el bloque de cilindros.
No se permiten grietas en los cojinetes u otras áreas del bloque de cilindros.
Si sospecha que ha entrado refrigerante en el cárter, compruebe la estanqueidad del bloque de cilindros en un soporte especial.
Para ello, tras tapar los orificios de la camisa de refrigeración del bloque de cilindros, inyectar agua a temperatura ambiente en el mismo a una presión de 0,3 MPa (3 kgf/cm 2)
No debe haber fugas de agua del bloque de cilindros durante dos minutos.
Si entra aceite en el refrigerante, entonces, sin desmontar completamente el motor, verifique si hay grietas en el bloque de cilindros en las áreas de los canales de aceite.
Para hacer esto, drene el refrigerante del sistema de enfriamiento, retire la culata, llene la camisa de enfriamiento del bloque de cilindros con agua y suministre aire comprimido al canal de aceite vertical del bloque de cilindros.
Si aparecen burbujas de aire en el agua que llena la camisa de enfriamiento, reemplace el bloque de cilindros.
Compruebe el plano de división del bloque de cilindros con la culata utilizando una regla y un juego de galgas de espesores.
La regla se coloca a lo largo de las diagonales del plano y en el centro en la dirección longitudinal y transversal.
La tolerancia de planitud es de 0,1 mm.
Compruebe si el desgaste de los cilindros supera el máximo permitido - 0,15 mm.
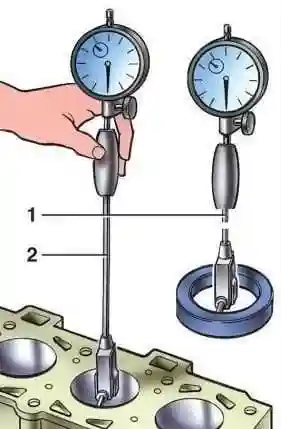
Medición de cilindros con calibre de diámetros
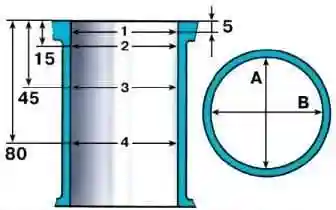
El diámetro del cilindro se mide con un calibre de diámetro interior en cuatro zonas, tanto en la dirección longitudinal como transversal del motor.
El calibre 67.8125.9502 se utiliza para poner a cero el calibre interior.
En la zona de la correa 1, los cilindros prácticamente no se desgastan.
Por lo tanto, por la diferencia de medidas en la primera y otras zonas, se puede juzgar la cantidad de desgaste del cilindro.
Si el valor de desgaste máximo es superior a 0,15 mm, taladre los cilindros al tamaño de reparación más cercano, dejando un margen de 0,03 mm para el diámetro de bruñido.
A continuación, bruñir los cilindros, manteniendo un diámetro tal que al instalar el pistón de reparación seleccionado, la holgura estimada entre este y el cilindro sea de 0,025 a 0,045 mm.
Comprobación del pistón
Limpie el pistón de los depósitos de carbón y elimine todos los depósitos de los canales de lubricación del pistón y la biela.
Inspeccione los detalles cuidadosamente.
No se permiten grietas de cualquier naturaleza en el pistón, anillos de pistón, bulón, en la biela y su tapa.
Si hay marcas profundas en la superficie de trabajo de los revestimientos, reemplácelos por otros nuevos.
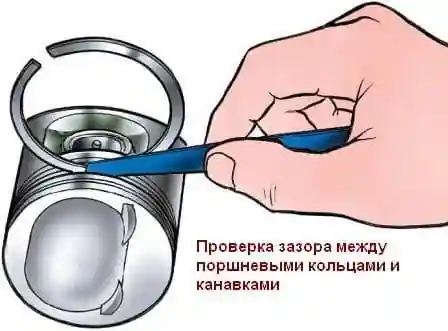
Compruebe la distancia entre los anillos del pistón y las ranuras con un juego de galgas de espesores, como se muestra en la figura, insertando el anillo en la ranura correspondiente.
Espacio nominal (calculado) para la parte superior el anillo de compresión es de 0,04-0,075 mm, para el inferior - 0,03-0,065 mm y para el rascador de aceite - 0,02-0,055 mm.
Separaciones máximas permitidas para el desgaste: 0,15 mm.
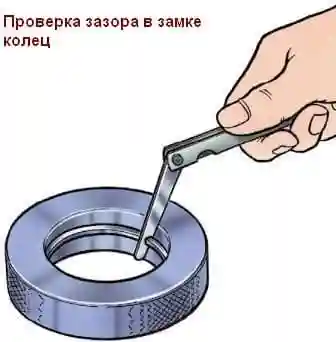
Compruebe la holgura en el bloqueo de los segmentos del pistón con un juego de galgas de espesores, insertando los segmentos en un calibre que tenga un diámetro interior igual al diámetro nominal del segmento con una tolerancia de ±0,003 mm.
Para anillos de tamaño normal con un diámetro de 82 mm, se puede utilizar el calibre 67.8125.9502. El espacio debe estar entre 0,25 y 0,45 mm para todos los anillos nuevos.
Distancia máxima de desgaste 1 mm.
Cigüeñal
El cigüeñal del motor 2112 se diferencia del cigüeñal de los motores 2110 y 2111 en forma de contrapesos y mayor resistencia.
Por lo tanto, no está permitido instalar el cigüeñal de los motores 2110 y 2111 en el motor 2112.
Para suministrar aceite desde los muñones principales a las bielas, se perforan canales en el cigüeñal, cuyas salidas se cierran con tapones prensados.
En el extremo delantero del cigüeñal, una polea del engranaje impulsor del árbol de levas está montada en una chaveta de segmento, se adjunta una polea impulsora del generador, que también es un amortiguador de vibraciones del cigüeñal.
Faltan dos dientes de 60 en la corona dentada de la polea; las cavidades se utilizan para el funcionamiento del sensor de posición del cigüeñal.
Inspeccione el cigüeñal. No se permiten grietas en ninguna parte del cigüeñal.
En las superficies que se acoplan con los bordes de trabajo de los sellos, no se permiten rayones, muescas ni marcas.
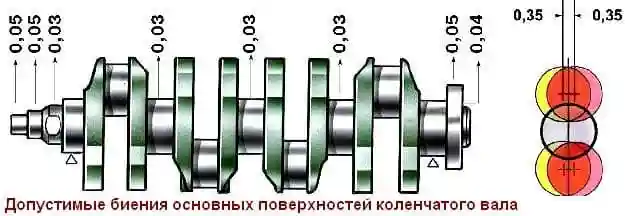
Instale el cigüeñal con muñones principales extremos en dos prismas y verifique el descentramiento con un indicador:
- - muñones principales y superficie de asiento para el engranaje impulsor de la bomba de aceite (no más de 0,03 mm);
- - superficie de apoyo para el volante (no más de 0,04 mm);
- - superficie de asiento para poleas y superficies que se acoplan con sellos de aceite (no más de 0,05 mm).
Mida los diámetros de los muñones principal y de biela.
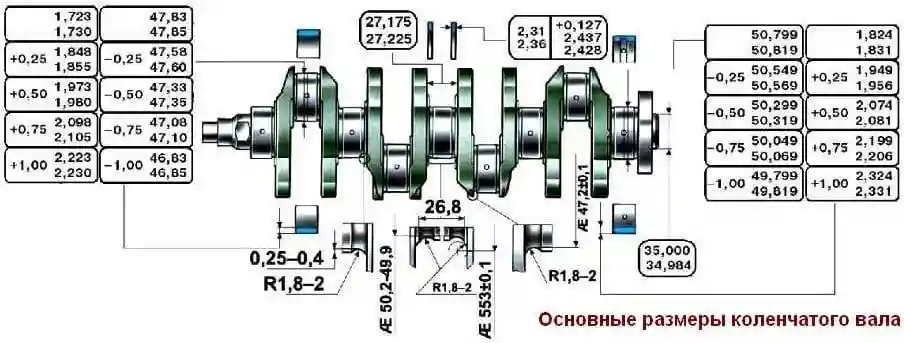
Los cuellos deben rectificarse si su desgaste es superior a 0,03 mm o la ovalidad de los cuellos es superior a 0,03 mm, y también si hay rozaduras y arañazos en los cuellos.
Esmerile los cuellos con una reducción de diámetro al tamaño de reparación más cercano.
Al esmerilar, mantenga las dimensiones de los filetes de muñón similares a las que se muestran en la Figura 6 para las dimensiones normales del cigüeñal.
La ovalidad y la conicidad de los muñones principal y de biela después de rectificar no debe ser superior a 0,005 mm.
El desplazamiento de los ejes de los muñones de biela desde el plano que pasa por los ejes de la biela y los muñones principales después del rectificado debe ser de ± 0,35 mm.
Para verificar, instale el eje con los muñones principales extremos en prismas y ajuste el eje de modo que el eje del muñón de la biela del primer cilindro esté en un plano horizontal que pase por los ejes de los muñones principales.
Luego, utilice un indicador para comprobar el desplazamiento vertical de las muñequillas de los cilindros 2.°, 3.° y 4.° con respecto a la muñequilla del 1.er cilindro.
Después de esmerilar los cuellos, pulirlos con pasta de diamante o pasta GOI.
Después del rectificado y posterior acabado de los cuellos, retire los tapones de los canales de aceite y luego procese los casquillos de los tapones con un cortador A. 94016/10, coloque el husillo A. 94016.
Enjuague bien el cigüeñal y sus conductos para eliminar los residuos abrasivos y sople con aire comprimido.
Usando el punzón A.86010, presione los tapones nuevos y marque cada uno en tres puntos con un punzón central.
En la primera mejilla del cigüeñal, marque la cantidad de reducción en los muñones principal y de biela (por ejemplo, K 0,25; W 0,50).
Inserciones. No se pueden realizar operaciones de ajuste en los liners.
Cuando raspe, raye o pele, reemplace los revestimientos por otros nuevos.
El espacio entre las camisas y los muñones del cigüeñal se verifica mediante cálculo (midiendo los detalles).
Es conveniente utilizar un hilo de plástico calibrado para comprobar el hueco. En este caso, el método de validación es el siguiente:
- - limpiar cuidadosamente las superficies de trabajo de los liners y el cuello correspondiente y colocar un trozo de alambre plástico sobre su superficie;
- - instale una biela con sombrerete o un sombrerete de cojinete de bancada en el cuello (según el tipo de cuello que se esté comprobando) y apriete las tuercas o tornillos de fijación.
Apriete las tuercas de los tornillos de biela a un par de 51 Nm (5,2 kgf m) y los tornillos de las tapas de los cojinetes de bancada a un par de 80,4 Nm (8,2 kgf m);
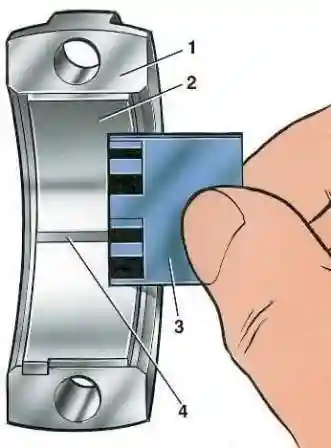
- - retire la cubierta y use la escala impresa en el paquete para determinar el tamaño del espacio por el aplanamiento del cable.
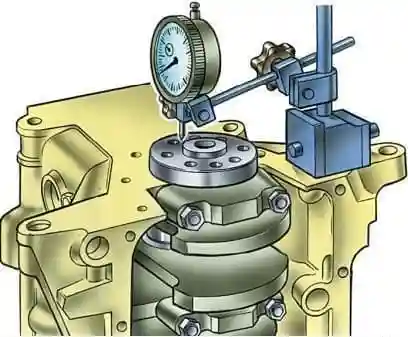
La holgura de diseño nominal es de 0,02 a 0,07 mm para los muñones de biela y de 0,026 a 0,073 mm para los muñones principales.
Si el espacio es inferior al límite (0,1 mm para la biela y 0,15 mm para los muñones principales), estos revestimientos se pueden usar nuevamente.
Si el espacio es mayor que el límite, reemplace los revestimientos de estos cuellos por otros nuevos.
Si los muñones del cigüeñal están desgastados y rectificados a un tamaño de reparación, reemplace los revestimientos por otros de reparación (mayor espesor).
Semicojinetes de empuje. Al igual que en las camisas, no se pueden realizar operaciones de montaje en medias anillas.
En caso de rozaduras, riesgos o delaminaciones, reemplace los medios anillos por otros nuevos.
Los medios anillos también se reemplazan si el juego axial del cigüeñal excede el máximo permitido: 0,35 mm.
Para medios anillos nuevos, seleccione un espesor nominal o aumentado en 0,127 mm para obtener un juego axial en el rango de 0,06–0,26 mm.
Compruebe el juego axial libre del cigüeñal.
Para hacer esto, gire el bloque de cilindros con su parte trasera hacia arriba e instale un soporte con un indicador en él para que la pata del indicador descanse contra la brida del cigüeñal.
Mover el eje hacia arriba y hacia abajo (por ejemplo, con destornilladores), medir el movimiento axial libre del eje con un indicador
Volante
Compruebe el estado de la corona dentada y reemplace el volante si los dientes están dañados.
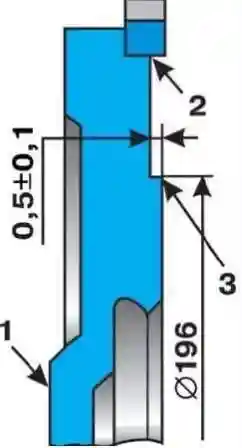
Si el volante presenta decoloración en la superficie 3, verifique el ajuste de la llanta en el volante.
La llanta no debe girar con un par de 590 Nm (60 kgf·m) ni moverse axialmente bajo una fuerza de 3,9 kN (400 kgf).
En la superficie 1 del volante adyacente a la brida del cigüeñal y en la superficie 3 debajo del disco de embrague, no se permiten rayones ni rozaduras.
La tolerancia de falta de planitud de la superficie 3 es de 0,06 mm.
Elimine rayones y rozaduras en la superficie 3 con una ranura, eliminando una capa de metal de no más de 1 mm de espesor.
Al mismo tiempo, rectificar también la superficie 2 sin afectar a la corona dentada y manteniendo una dimensión de (0,5 ± 0,1) mm.
Al girar, es necesario asegurarse de que las superficies 2 y 3 estén paralelas con respecto a la superficie 1.
Tolerancia de no paralelismo 0,1 mm.
Monte el volante en el eje, centrándolo en el orificio contra la superficie 1, y verifique el descentramiento de los planos 2 y 3.
En los lugares indicados por las flechas en la figura, el indicador no debe mostrar pulsaciones superiores a 0,1 mm.