Розбір двигуна ми розглянули у статті – Розбір двигуна.
У цій статті ми розглянемо дефектацію деталей та підготовку основних деталей до складання.
Блок циліндрів
Блок циліндрів двигуна ВАЗ-2112 теж має номер "21083" як і у двигунів 2110 і 2111, але вони незамінні: отвори під гвинти головки циліндрів мають різьблення М10х1, 25 (на відміну від М12х1, 22 для блоків 1 ) та меншу глибину.
Інша відмінність пов'язана з більш напруженим тепловим режимом двигуна 2112 порівняно з двигунами 2110 та 2111.
Для охолодження поршнів під час роботи двигуна їх днища омиваються знизу маслом через спеціальні форсунки, запресовані у другу, третю, четверту та п'яту опори корінних підшипників.
Циліндри розточені безпосередньо в блоці.
Номінальний діаметр 82 мм при ремонті може бути збільшений на 0,4 або 0,8 мм.
Клас циліндра маркується на нижній площині блоку латинськими літерами відповідно до діаметра циліндра в мм: А – 82,00-82,01, В – 82,01-82,02, С – 82,02-82,03, D - 82,03-82,04, Е - 82,04-82,05.
Максимально допустиме зношування циліндра становить 0,15 мм на діаметр.
Ретельно вимийте блок циліндрів та очистіть масляні канали.
Продувши та просушивши стисненим повітрям, огляньте блок циліндрів.
Тріщини в опорах або інших місцях блоку циліндрів не допускаються.
Якщо є підозра на потрапляння охолоджуючої рідини в картер, то на спеціальному стенді перевірте герметичність блоку циліндрів.
Для цього, заглушивши отвори охолоджуючої сорочки блоку циліндрів, нагнітайте в неї воду кімнатної температури під тиском 0,3 МПа (3 кгс/см 2).
Протягом двох хвилин не повинно спостерігатися витоку води з блоку циліндрів.
Якщо спостерігається попадання олії в охолоджувальну рідину, то без повного розбирання двигуна перевірте, чи немає тріщин у блоку циліндрів у зонах масляних каналів.
Для цього злийте охолоджувальну рідину із системи охолодження, зніміть головку циліндрів, заповніть сорочку охолодження блоку циліндрів водою і подайте стиснене повітря у вертикальний масляний канал блоку циліндрів.
У разі появи бульбашок повітря у воді, що заповнює сорочку охолодження, замініть блок циліндрів.
Перевірте площину роз'єму блоку циліндрів з головкою за допомогою лінійки та набору щупів.
Лінійка встановлюється за діагоналями площини та в середині в поздовжньому напрямку та впоперек.
Допуск площинності становить 0,1 мм.
Перевірте, чи не перевищує знос циліндрів максимально допустимий – 0,15 мм.
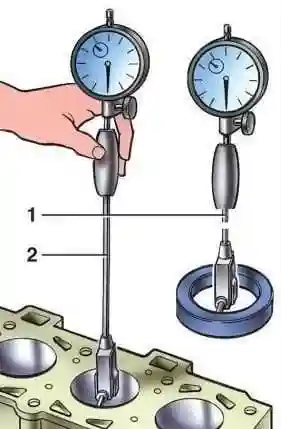
Вимірювання циліндрів нутроміром
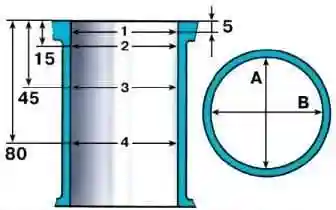
Діаметр циліндра вимірюється нутроміром у чотирьох поясах, як у поздовжньому, так і в поперечному напрямку двигуна.
Для встановлення нутроміра на нуль застосовується калібр 67.8125.9502.
У зоні пояса 1 циліндри практично не зношуються.
Тож по різниці вимірів у першому та інших поясах можна судити про величину зносу циліндрів.
Якщо максимальна величина зношування більше 0,15 мм — розточіть циліндри до найближчого ремонтного розміру, залишивши припуск 0,03 мм на діаметр під хонінгування.
Потім відхонінгуйте циліндри, витримуючи такий діаметр, щоб при встановленні обраного ремонтного поршня розрахунковий зазор між ним і циліндром був 0,025–0,045 мм.
Перевірка поршня
Очистіть поршень від нагару та видаліть всі відкладення з мастильних каналів поршня та шатуна.
Ретельно огляньте деталі.
Тріщини будь-якого характеру на поршні, поршневих кільцях, пальці, на шатуні та його кришці не допускаються.
Якщо на робочій поверхні вкладишів є глибокі ризики, замініть вкладки на нові.
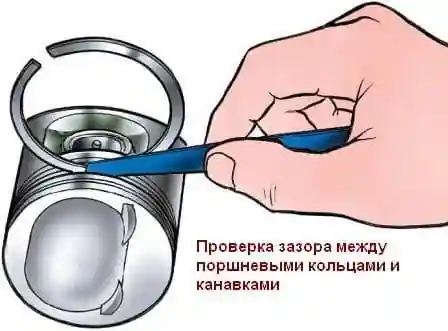
Зазор між поршневими кільцями та канавками перевіряйте набором щупів, як показано на малюнку, вставляючи кільце у відповідну канавку.
Номінальний (розрахунковий) зазор для верхнього компресійного кільця становить 0,04–0,075 мм, для нижнього – 0,03–0,065 мм та для маслознімного – 0,02–0,055 мм.
Гарно допустимі зазори при зносі – 0,15 мм.
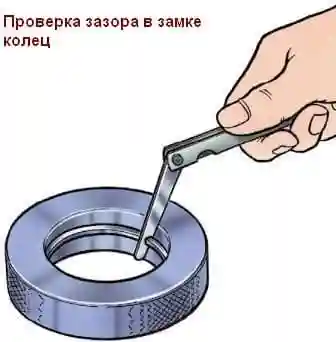
Зазор у замку поршневих кілець перевіряйте набором щупів, вставляючи кільця в калібр, що має діаметр отвору, що дорівнює номінальному діаметру кільця з допуском ±0,003 мм.
Для кілець нормального розміру діаметром 82 мм можна застосовувати калібр 67.8125.9502. Зазор повинен бути в межах 0,25-0,45 мм для всіх нових кілець.
Вкрай допустимий зазор при зносі 1 мм.
Колінчастий вал
Колінчастий вал двигуна 2112 відрізняється від колінчастого валу двигунів 2110 і 2111 формою противаг і підвищеною міцністю.
Тому не допускається встановлення колінчастого валу від двигунів 2110 та 2111 у двигун 2112.
Для подачі олії від корінних шийок до шатунних у колінчастому валі просвердлені канали, вихідні отвори яких закриті запресованими заглушками.
На передньому кінці колінчастого валу на сегментній шпонці встановлено зубчастий шків приводу розподільчого валу, до нього кріпиться шків приводу генератора, який також є демпфером крутильних коливань колінчастого валу.
На зубчастому вінці шківа два зуби з 60 відсутні – западини служать для роботи датчика положення колінчастого валу.
Огляньте колінчастий вал. Тріщини в будь-якому місці колінчастого валу не допускаються.
На поверхнях, що сполучаються з робочими кромками сальників, не допускаються подряпини, вибоїни та ризики.
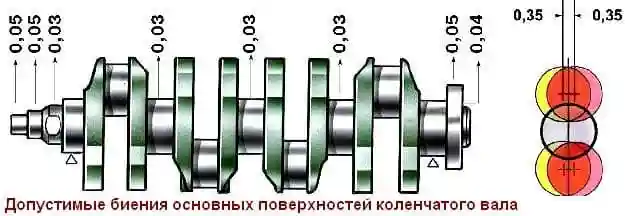
Встановіть колінчастий вал крайніми корінними шийками на дві призми та перевірте індикатором биття:
- – корінних шийок та посадкової поверхні під провідну шестерню масляного насоса (не більше 0,03 мм);
- – посадкова поверхня під маховик (не більше 0,04 мм);
- – посадкова поверхня під шківи та поверхонь, що сполучаються з сальниками (не більше 0,05 мм).
Виміряйте діаметр корінних і шатунних шийок.
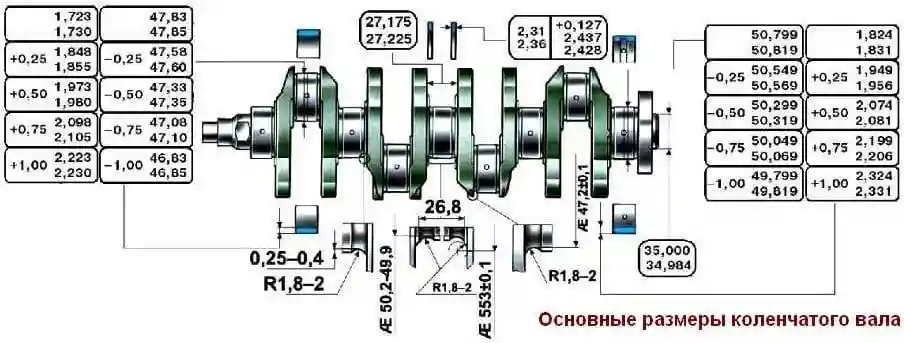
Шийки слід шліфувати, якщо їх знос більше 0,03 мм або овальність шийок більше 0,03 мм, а також, якщо на шийках є задираки та ризики.
Шліфуйте шийки зі зменшенням діаметра до найближчого ремонтного розміру.
При шліфуванні витримуйте розміри жолобників шийок, аналогічні вказаним на малюнку 6 для нормальних розмірів колінчастого валу.
Овальність та конусність корінних та шатунних шийок після шліфування має бути не більше 0,005 мм.
Зміщення осей шатунних шийок від площини, що проходить через осі шатунних та корінних шийок, після шліфування має бути в межах ±0,35 мм.
Для перевірки встановіть вал крайніми корінними шийками на призми і виставте вал так, щоб вісь шатунної шийки першого циліндра знаходилася в горизонтальній площині, що проходить через осі корінних шийок.
Потому індикатором перевірте зміщення у вертикальному напрямку шатунних шийок 2, 3 і 4 циліндрів щодо шатунної шийки 1-го циліндра.
Прошліфувавши шийки, відполіруйте їх за допомогою алмазної пасти або пасти ГОІ.
Після шліфування та подальшого доведення шийок видаліть заглушки масляних каналів, а потім обробіть гнізда заглушок фрезою А. 94016/10, одягненою на шпиндель А. 94016.
Ретельно промийте колінчастий вал та його канали для видалення залишків абразиву та продуйте стиснутим повітрям.
Оправкою А.86010 запресуйте нові заглушки та зачеканьте кожну в трьох точках кернером.
На першій щоці колінчастого валу маркуйте величину зменшення корінних і шатунних шийок (наприклад, К 0,25; Ш 0,50).
Вкладиші. На вкладишах не можна робити ніяких підгоночних операцій.
При задирах, ризиках або відшаруваннях замініть вкладки новими.
Зазор між вкладишами та шийками колінчастого валу перевіряють розрахунком (промірявши деталі).
Зручно для перевірки зазору користуватися каліброваним пластмасовим дротом. У цьому випадку метод перевірки є наступним:
- – ретельно очистіть робочі поверхні вкладишів та відповідної шийки та покладіть відрізок пластмасового дроту на його поверхню;
- – встановіть на шийці шатун з кришкою або кришку корінного підшипника (залежно від виду шийки, що перевіряється) і затягніть гайки або болти кріплення.
Гайки шатунних болтів затягуйте моментом 51 Нм (5,2 кгс·м), а болти кріплення кришок корінних підшипників моментом 80,4 Нм (8,2 кгс·м);
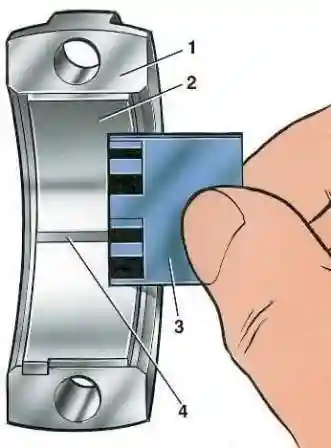
- – зніміть кришку та за шкалою, нанесеною на упаковці, по сплющуванню дроту визначте величину зазору.
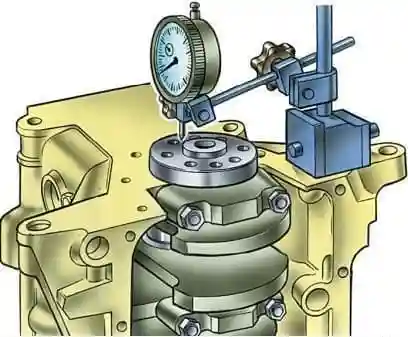
Номінальний розрахунковий зазор становить 0,02–0,07 мм для шатунних та 0,026–0,073 мм для корінних шийок.
Якщо зазор менший за граничний (0,1 мм для шатунних і 0,15 мм для корінних шийок), то можна знову використовувати ці вкладиші.
При більшому зазорі граничного замініть на цих шийках вкладки новими.
Якщо шийки колінчастого валу зношені та шліфуються до ремонтного розміру, то вкладиші замініть ремонтними (збільшеною товщиною).
Наполегливі півкільця. Так само як і на вкладишах, на півкільцях не можна робити ніяких підгонкових операцій.
При задирах, ризиках або відшаруваннях замінюйте півкільця новими.
Напівкільця замінюються також, якщо осьовий зазор колінчастого валу перевищує максимально допустимий – 0,35 мм.
Нові півкільця підбирайте номінальної товщини або збільшеної на 0,127 мм, щоб отримати осьовий зазор в межах 0,06–0,26 мм.
Перевірте вільний хід колінчастого валу.
Для цього поверніть блок циліндрів задньою стороною вгору і встановіть на неї стійку з індикатором так, щоб ніжка індикатора упиралася у фланець колінчастого валу.
Переміщаючи вал вгору та вниз (наприклад, викрутками), заміряйте індикатором вільний осьовий хід валу
Маховик
Перевірте стан зубчастого обода і замініть маховик у разі пошкодження зубів.
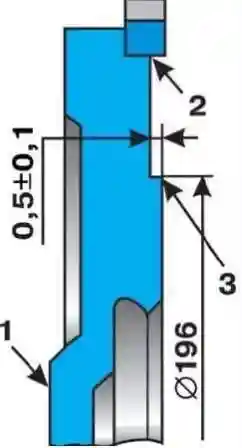
Якщо маховик має кольори втечі на поверхні 3, необхідно перевірити натяг обода на маховику.
Обід не повинен прокручуватися при крутному моменті 590 Н·м (60 кгс·м) або зрушуватися в осьовому напрямку під зусиллям 3,9 кН (400 кгс).
На поверхні 1 маховика, що прилягає до фланця колінчастого валу, і на поверхні 3 під ведений диск зчеплення не допускаються подряпини та задираки.
Допуск неплощинності поверхні 3 становить 0,06 мм.
Дряпини та задирки на поверхні 3 видаліть проточкою, знімаючи шар металу товщиною не більше 1 мм.
При цьому проточіть також і поверхню 2, не торкаючись зубчастого обіду і витримуючи розмір (0,5 ±0,1) мм.
При проточці необхідно забезпечити паралельність поверхонь 2 та 3 щодо поверхні 1.
Допуск непаралельності 0,1 мм.
Встановіть маховик на оправку, центруючи його по отвору з упором на поверхню 1, і перевірте биття площин 2 і 3.
У місцях, вказаних стрілками на малюнку, індикатор не повинен показувати биття, що перевищує 0,1 мм.