The main dimensions of the connecting rod and piston group are shown in Figure 1.
The piston is cast aluminum. The mass of the pistons is strictly maintained in the manufacture.
Therefore, when assembling the engine, it is not necessary to select pistons of the same group by weight.
According to the outer diameter, the pistons are divided into five classes (A, B, C, D, E) through 0.01 mm. The outer surface of the piston has a complex shape.
It is barrel-shaped in height, and oval in cross section.
Therefore, it is only necessary to measure the piston diameter in a plane perpendicular to the piston pin, at a distance of 55 mm from the piston crown.
According to the diameter of the hole for the piston pin, pistons are divided into three classes (1, 2, 3) through 0.004 mm.
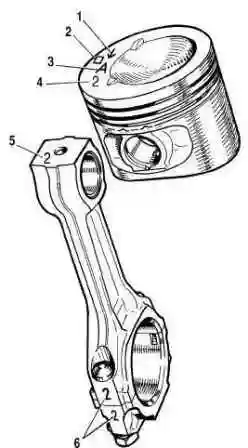
Piston diameter classes and piston pin bores are stamped on the piston crown
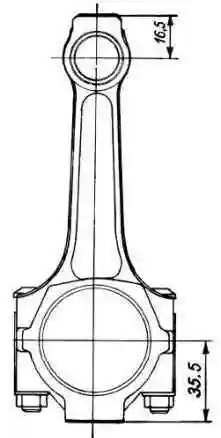
Oversize pistons are manufactured with an outer diameter increased by 0.4 and 0.8 mm.
The bottoms of these pistons are marked with a triangle or a square.
The triangle corresponds to an increase in the outer diameter by 0.4 mm, and the square corresponds to 0.8 mm.
The arrow on the bottom of the piston shows how to correctly orient the piston when it is installed in the cylinder.
It should be directed towards the camshaft drive.
The piston pin is steel, hollow, floating type, the father-in-law freely rotates in the piston bosses and the connecting rod bush.
The pin is fixed in the piston with two steel retaining rings.
According to the outer diameter, the fingers are divided into three classes through 0.004 mm.
The class is marked with paint on the end of the finger: the blue mark is the first, the green mark is the second, and the red mark is the third class.
Piston rings - made of cast iron.
Top Compression Ring - Barrel chrome-plated outer surface.
Scraper type lower compression ring.
Oil scraper ring - with chrome-plated working edges and with an expanding coil spring (expander).
On the rings of repair sizes, the digital marking "40" or "80" is put, which corresponds to an increase in the outer diameter by 0.4 or 0.8 mm.
Connecting rod - steel, forged.
The connecting rod is machined together with the cap and therefore they are not interchangeable individually.
In order not to confuse the covers and connecting rods during assembly, they are stamped with the number 6 (see Figure 2) of the cylinder in which they are installed.
When assembling, the numbers on the connecting rod and the cap must be on the same side
A steel-bronze bushing is pressed into the upper head of the connecting rod.
According to the diameter of the hole of this bushing, the connecting rods are divided into three classes through 0.004 mm (the same as the pistons).
Class 5 number is stamped on the upper head of the connecting rod.
By the mass of the upper and lower heads, the connecting rods are divided into classes (table), marked with paint on the rod of the connecting rod.
Connecting rods of the same weight class must be installed on the engine.
You can adjust the mass of connecting rods by removing metal from the bosses on the heads to the minimum dimensions of 16.5 and 35.5 mm (Figure 3).
Connecting rod weight classes for upper and lower heads
Mass of connecting rod heads, g. |
class |
Color marking |
|
---|---|---|---|
Top |
Lower |
||
186±2 |
519±3 |
A |
white |
525±3 |
B |
blue |
|
531±3 |
С |
red |
|
190±2 |
519±3 |
D |
black |
525±3 |
E |
purple |
|
531±3 |
F |
green |
|
194±2 |
519±3 |
G |
yellow |
525±3 |
H |
brown |
|
531±3 |
I |
orange |
Since the release of 2012, the masses of the connecting rod heads have changed a little
Mass of connecting rod heads, g. |
class |
Color marking |
|
---|---|---|---|
Top |
Lower |
||
186±2 |
527±3 |
A |
white |
533±3 |
B |
blue |
|
539±3 |
С |
red |
|
190±2 |
527±3 |
D |
black |
533±3 |
E |
purple |
|
539±3 |
F |
green |
|
194±2 |
527±3 |
G |
yellow |
533±3 |
H |
brown |
|
539±3 |
I |
orange |
Selection of a piston to a cylinder
The calculated minimum clearance between the piston and the cylinder (for new parts) is 0.025 - 0.045 mm.
It is defined as the difference between the minimum cylinder size and the maximum piston size and is provided by installing pistons of the same class as the cylinders.
The maximum allowable gap (when parts are worn) is 0.15 mm.
If a used engine has a clearance greater than 0.15 mm, then it is necessary to reselect the pistons to the cylinders so that the clearance is as close as possible to the calculated one.
Pistons of classes A, C, E are available as spare parts.
These classes are enough to match a piston to any cylinder when repairing an engine, since pistons and cylinders are divided into classes with a slight overlap in size.
For example, class B and D cylinders can be fitted with a class C piston.
Disassembly and assembly
Disassembly
Remove the piston pin circlips from the piston, remove the pin and disconnect the connecting rod from the piston.
Remove the piston rings.
The connecting rod bolts are pressed into the connecting rod.
Therefore, in order not to disturb the fit of the bolt in the connecting rod, it is not allowed to press the bolts out of the connecting rods when disassembling the engine and the connecting rod and piston group.
If some parts of the connecting rod and piston group are not damaged and slightly worn, then they can be reused.
Therefore, when disassembling, mark them in order to later assemble a group with the same parts and install in the same engine cylinder.
Assembly
Before assembling, put your finger on the piston and connecting rod.
For new parts, the class of the pin holes in the connecting rod and piston must be identical to the class of the pin.
For used parts, for proper mating, it is necessary that the piston pin, lubricated with engine oil, enter the piston or connecting rod hole by simply pressing the thumb (Figure 4) and not fall out of it if you hold the piston as shown in Figure 5.
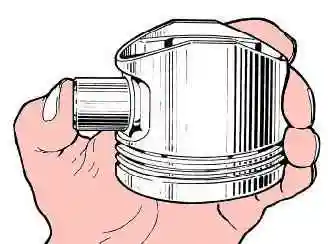
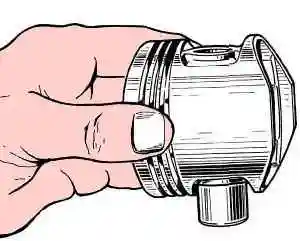
Replace the drop-down finger with another one of the next category.
If a third category pin was inserted into the piston, then replace the piston pin and connecting rod.
The connecting rod and piston group is assembled in the reverse order of disassembly.
After installing the piston pin, lubricate it with engine oil through the holes in the piston bosses.
Install the piston rings in the following order.
Lubricate the piston grooves and piston rings with engine oil.
Orient the piston rings so that the top ring lock is at a 45˚ angle to the piston pin axis, the lower compression ring lock is at approximately 180˚ to the top compression ring lock axis, and the oil scraper ring lock is at approximately 90˚ to the axis of the lock of the upper compression ring
Install the lower compression ring with the groove down (see Figure 1).
If the ring is marked “Top” or “TOP”, then install the ring with the mark up (towards the piston bottom).
Before installing the oil scraper ring, check that the joint of the spring expander is located on the side opposite the ring lock.
Disassembly and assembly of the connecting rod and piston group can be see here.
Checking the technical condition
Clean the piston from carbon deposits and remove all deposits from the lubrication channels of the piston and connecting rod.
Inspect the details carefully.
Cracks of any nature on the piston, piston rings, pin, on the connecting rod and its cover are not allowed.
If there are deep marks on the working surface of the liners, replace the liners with new ones.
Check the gap between the piston rings and the grooves with a set of feeler gauges, as shown in Figure 6, inserting the ring into the corresponding groove.
The calculated clearance (rounded to 0.01 mm) for new parts is 0.04-0.07 mm for the upper compression ring, 0.03-0.06 mm for the lower one and 0.02-0 for the oil scraper .05 mm.
Maximum allowable gaps for wear -0.15 mm.
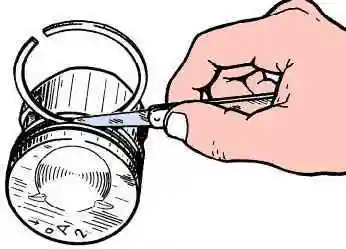
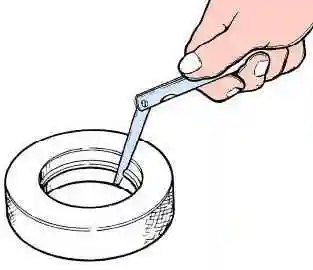
Check the gap in the lock of the piston rings with a set of feeler gauges, inserting the rings into a gauge (Figure 7) having a hole diameter equal to the nominal diameter of the ring with a tolerance of 0.003 mm.
For normal size rings with a diameter of 82 mm, caliber 67.8125.9502 can be used.
Gap should be between 0.25 - 0.45 mm for all new rings. The maximum allowable wear clearance is 1 mm.