The air conditioner compressor is a very complex, high-tech device.
Some components of the pump part of the compressor are made to order.
Therefore, component manufacturers do not supply spare parts for compressor pump parts.
The only compressor unit that can be repaired in the garage is the electromagnetic drive clutch.
Compressor clutch failure is a very common problem in car operation.
Usually, the pulley bearing starts to fall off first.
The reason is incorrect tension of the drive belt, water leakage when driving through deep puddles, slippage of the pressure plate and, as a result, overheating of the bearings, etc. maybe.
As the bearing wears, the pulley begins to play.
When the backlash reaches a critical value, the inner surface of the pulley begins to rub against the surface of the electromagnetic coil body during rotation.
As a result of friction, the parts heat up, the insulation of the coil windings begins to burn, an electrical short occurs - the solenoid fails.
In the most advanced cases, bearing jams and the inner race of the bearing rotate on the compressor cover seating neck.
Then the compressor needs to be replaced, which is very expensive.
To avoid unnecessary costs, pay attention when inspecting the car for noise that is not characteristic of the operation of the air conditioning compressor.
If you suspect a bad pulley bearing, remove the drive belt and turn the pulley by hand.
The pulley should rotate smoothly, silently, without jamming on the bearing.
There must be no axial or radial play.
If necessary, replace the bearing without waiting for it to be completely removed.
Removing the air conditioning compressor
As described in the previous article, we remove the air conditioner from the air conditioning system.
Install the car on a lift or viewing hole
Disconnect the negative battery terminal
Removing the engine mud guard
Remove the accessory drive belt.
If you notice the following during inspection, replace the belt:
- - signs of wear on the surface of the gear, cracks, cuts, folds or layers of rubber on the fabric;
- - cracks, folds, depressions or bumps on the outer surface of the belt;
- - weakening or overlapping on the edges of the tape;
- - Traces of oil on the surface of the belt.
The belt must be replaced with traces of engine oil on any surface, as oil rubber will quickly fail.
Repair the cause of the impact immediately (usually due to leaking motor shaft seals).
Unscrew the bolt securing the flange of the low pressure pipe to the compressor
Unscrew the bolt securing the flange of the high pressure pipe to the compressor
Disconnect the pipes
After disconnecting the hoses, close the openings immediately to prevent dirt and moisture from entering the hoses and the compressor.
Disconnect the solenoid coil power switch.
We unscrew the four bolts securing the air conditioning compressor to the engine block and remove them from the mounting holes.
A/C compressor installation
Install the compressor in reverse order.
Technological plugs of new compressor flanges should only be opened before connecting the nozzles.
Lubricate the new O-rings with compressor oil.
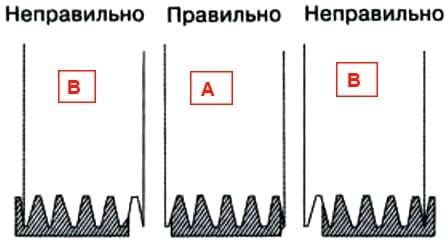
When installing the compressor drive belt, make sure the wedge lines line up with the slots on the pulley.
When buying a new compressor, ask the seller how much oil was filled in the compressor and the type of oil.