The driveline consists of front and rear shafts that transmit torque from the transfer case to the drive axles.
Each cardan shaft has needle bearing universal joints at the ends
On long-wheelbase modifications of UAZ-3153 vehicles, instead of the rear shaft, a cardan gear of two shafts with an intermediate support mounted on the frame cross member is installed
The rear driveshaft consists of a pipe, to one end of which a hinge yoke is welded, and to the other end a splined tip that enters the splined hole of the second hinge yoke
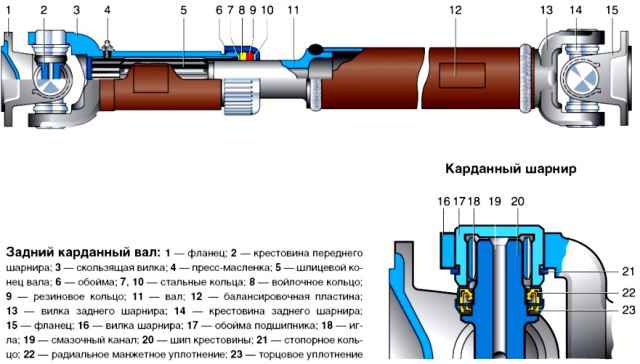
This connection compensates for the change in the length of the cardan shaft during suspension operation
The front driveshaft is of the same design, except for the part of the pipe running under the clutch housing, which is replaced by a small diameter solid rod
This is done to prevent the shaft from touching the crankcase when the front suspension is working
To protect against dirt and retain grease, there are rubber cuffs in the cages of the hinge bearings, and rubber mechanical seals are installed on the spikes of the crosses.
Spline joints are sealed with rubber and felt rings.
Hinges and splines are lubricated through grease fittings screwed into the joints of the hinges and the sliding forks of the shafts
Gimbal Lubrication
We work on a lift or a viewing ditch
In the latter case, hang out the rear wheel and turn off the front wheel drive
Shift into neutral
We clean the cardan shafts, hinges and grease fittings on the crosses of the hinges and the spline connection from dirt.
At the same time, we turn the cardan shaft to access the grease fittings
We inject grease into the grease fittings of the hinges with a syringe until it appears from under the seals of all four bearings of each hinge
If this does not happen, the oiler valve may be clogged or the seal of any bearing is faulty (grease comes out only from under this seal)
To clean the valves of the oiler, unscrew the oiler with pliers
We wash the oiler in kerosene and blow it with compressed air
By pressing a thin rod on the valve ball, we make sure that it is movable and closes the oiler channel under the action of a spring
Replace a faulty oiler
We also replace a damaged bearing seal
We also lubricate the spline connection, do not pump too much grease here (waiting for the grease to come out from under the seal)
If necessary, unscrew the splined grease nipple with an 8 wrench and check as above
We lubricate the spline connection and the hinges of the front driveshaft in the same way
Possible driveline malfunctions and troubleshooting
Fault
probable cause
Device method anenii
Gimbal vibration (appears as a hum and intermittent noise and increases with increasing vehicle speed)
- Shaft imbalance
Balance the shaft. If this is not possible, then replace the shaft assembly with hinges
- Cardan shaft deformation
Replace shaft
- Severe wear of the propeller shaft spline
Replace shaft
- Wear of holes in the ears of the forks and flanges of the cardan shafts
Replace shaft, flanges or sliding yoke
Knocking or knocking in the driveline when shifting gears or engine braking
- Loosening the fasteners of the driveline
Tighten fasteners
- Wear of the splines of the axle drive flange
Replace flange
- Severe wear of the propeller shaft spline
Replace shaft
- Strong wear of the cross. The presence of longitudinal dents on the trunnions
Replace the cross complete with bearings and cuffs
Install the collar so that its spring faces the mechanical seal pressed onto the cross