In most cases, repair of the cylinder head consists of lapping or replacing valves and their guide bushings, replacing or grinding valve seats
Moreover, to perform work related to the repair of valve guides and seats, special tools and equipment are required.
In case of such malfunctions as a violation of the tightness of the channels of the jacket of the cooling system and warping of the mating surface to the cylinder block, the block head is replaced.
To complete the task, you will need tools: wrenches for 10, 12, 17, a spark plug wrench, a magnetized flat-blade screwdriver (or tweezers) for removing valve spring cotters, a valve spring compressor tool.
Preparing the car for work.
We remove the exhaust manifold (article - Removing elements of the Renault Duster exhaust system)
We remove the intake pipe and the fuel rail (article - Removing and installing the Renault Duster engine receiver)
Check the operation of the hydraulic compensators, if necessary, flush or replace them with new ones (article - Removing the camshafts and hydro bearings of the Renault Duster valves).
Install the valve spring compressor, compress the springs, remove the spring cotters,
-springs (see "Replacing Renault Duster valve stem seals").
Remove the valves from the guide bushings.
After prolonged use, a mushroom-shaped burr may form on the upper end of the valve.
Remove this burr with a needle file before removing the valve from the valve guide.
It is forbidden to knock the valve out of the guide sleeve with a hammer through the mandrel without removing the burr, as this will inevitably damage the inner surface of the sleeve.
Remove tar deposits from the top surface of the head and from the intake ports.
These deposits can be softened and washed away with kerosene or diesel fuel.
Clean the combustion chambers and exhaust channels from carbon deposits.
Remove carbon deposits with a round metal brush mounted in an electric drill chuck.
Pre-soak the soot with kerosene.
Clean the inside surfaces of the valve guides with a thin cylindrical brush of copper wire clamped in an electric drill chuck.
Remove burnt gasket residue from the cylinder head contact surface.
It is forbidden to clean the mating surface of the head with metal brushes or sandpaper.
Use a hardwood or plastic spatula after softening the rest of the gasket with solvent.
After cleaning, inspect the head of the block to prevent its operation with damaged threaded holes, cracks (especially between valve seats and in exhaust passages), corrosion, inclusions of foreign materials, shells and fistulas.
Using a feeler gauge and a metal ruler mounted on edge, check the flatness of the surface of the head to the block in the longitudinal and transverse directions, as well as diagonally.
If the gap between the edge of the ruler and the surface of the head is greater than 0.05 mm, replace the head.
Clean the surfaces of the flanges of the head flanges for installing the intake pipe and exhaust manifold from residues of gaskets and carbon deposits.
Check for deformation of the inlet pipe and exhaust manifold mounting flanges, replace the deformed head.
Damaged cuts repair the screw holes by threading with taps or installing a repair sleeve (screw).
Determine the wear of the valve guides by measuring the inner diameter of the valve guide bore and the diameter of the valve stem and determine the gap by the difference between these dimensions.
The maximum allowable wear clearance for intake valves is 0.10 mm, for exhaust valves it is 0.15 mm.
If the gap remains greater than the limit value even when installing new valves, replace the guide bushings.
Have the guide bushings replaced by a specialist workshop that has the proper tools and equipment.
Check the condition of the valve seats.
On the working chamfers of the seats, there should be no signs of wear, pitting, corrosion or other defects.
Valve seats can be replaced at a specialist workshop.
Minor damage (minor scratches, scratches, etc.) can be removed by lapping the valves.
More significant defects in valve seats are eliminated by grinding.
Saddles must be ground in a specialized workshop, as this requires special tools and equipment.
If significant defects in the seats cannot be corrected by grinding, replace the seats.
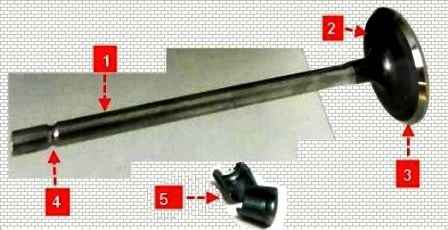
Remove carbon from the valves and inspect them.
Deformation of the valve stem 1 and cracks on its plate 2 are not allowed.
Replace the valve if damaged.
Check whether the working bevel 3 is too worn or damaged.
Grinding of the working chamfer of the valves is allowed (in repair shops with the appropriate equipment).
After grinding, the thickness of the cylindrical part of the plate must be at least 0.5 mm for intake valves and at least 1.0 mm for exhaust valves.
Minor scratches and scratches on the chamfer can be removed by lapping the valve against the seat.
Check the concentricity of the valve disc and the seat: apply a thin layer of paint (for example, Prussian blue) to the chamfer of the valve head, insert it into the guide sleeve and, pressing it lightly against the seat, turn it.
By traces of paint on the bevel of the seat, you can judge the concentricity of the valve and seat.
Check the condition of the grooves of the valve stem under the crackers.
If there are traces of chipping of the edges of the grooves and wear of the cylindrical part, replace the valve.
Replace valve stem seals regardless of their condition.
Inspect the valve springs.
Cracks and loss of spring elasticity are not allowed.
One of two types of springs can be installed.
The nominal free length of the first type of spring is (46.52) mm, the second type is (46.642) mm.
The length with fully compressed turns is 26.0 and 23.63 mm, respectively.
Springs whose length in the free state is less than the maximum permissible value, as well as twisted springs (the deviation of the spring axis from the vertical in the free state is more than 4˚) and with cracks, replace.
Check the condition of the spring plates. Replace the plates with significant wear on the support grooves for the springs.
Install all removed parts and components of the cylinder head in the reverse order of removal.
Always replace the gaskets of the cylinder head, intake pipe and exhaust manifold with new ones, since gaskets removed from the engine, even outwardly undamaged gaskets, may be heavily compressed and will not provide a tight seal.
Lapping of cylinder head valves
The valves are lapped on the removed cylinder head. to remove the valves from the guide bushings of the cylinder head, it is necessary to remove the valve springs by compressing them with a special tool and removing crackers from the spring plates (see "Replacing Renault Duster valve stem seals" ).
For lapping the valves, it is most convenient to use a special mechanical device (reversible drill).
Also, ready-made manual valve holders are available.
If there are no ready-made fixtures, you can use a fixture made according to the drawing.
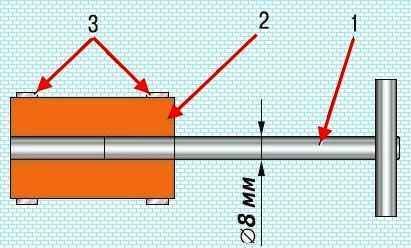
Instead of a rubber hose and clamps, a tip can be welded to the fixture stem, in the side wall of which a through threaded hole is made, into which a bolt is screwed to fix the valve stem.
In addition, you will need: lapping paste, kerosene, a weak spring, passing through the valve seat hole along the outer diameter.
Clean the valve from carbon deposits.
Apply a continuous, thin layer of lapping paste to the valve bevel.
Place a pre-selected spring on the valve stem and insert the valve into the guide sleeve from the side of the combustion chamber, lubricating the valve stem with a layer of graphite grease.
Graphite grease prevents the guide bushing from getting abrasive from the lapping paste into its holes and facilitates the rotation of the valve during lapping.
Put a valve lapping tool (or a rubber tube to connect the valve to the reversible drill) on the valve stem.
Turning on the drill at the minimum speed (in reverse mode) or rotating the device (in the case of manual lapping) alternately in both directions by half a turn, lap the valve, periodically pressing it against the seat, then loosening the pressing force.
Lap the valve until a matte gray continuous monophonic band with a width of at least 1.5 mm appears on its chamfer.
At the same time, a shiny belt with a width of at least 1.5 mm should also appear on the valve seat after lapping.
After lapping, wipe the valve and seat thoroughly with a clean cloth and rinse to remove any remaining lapping paste.
Check the tightness of the valve by installing it in the head with springs and crackers.
Then lay the head on its side and pour kerosene into the channel that is closed by the valve.
If kerosene does not seep into the combustion chamber within 3 minutes, the valve is tight.